We use cookies and other tracking technologies to improve your browsing experience on our website, By clicking "Accept All," you agree to allow cookies to be placed to enhance your browsing experience on this website to show you personalized content and targeted ads, to analyze our website traffic, and to understand where our visitors are coming from. You can manage your cookie settings below. Clicking "Confirm" indicates your agreement to adopt the current settings.
Vietnamese Film Producer Reduces Raw Material Cost Significantly
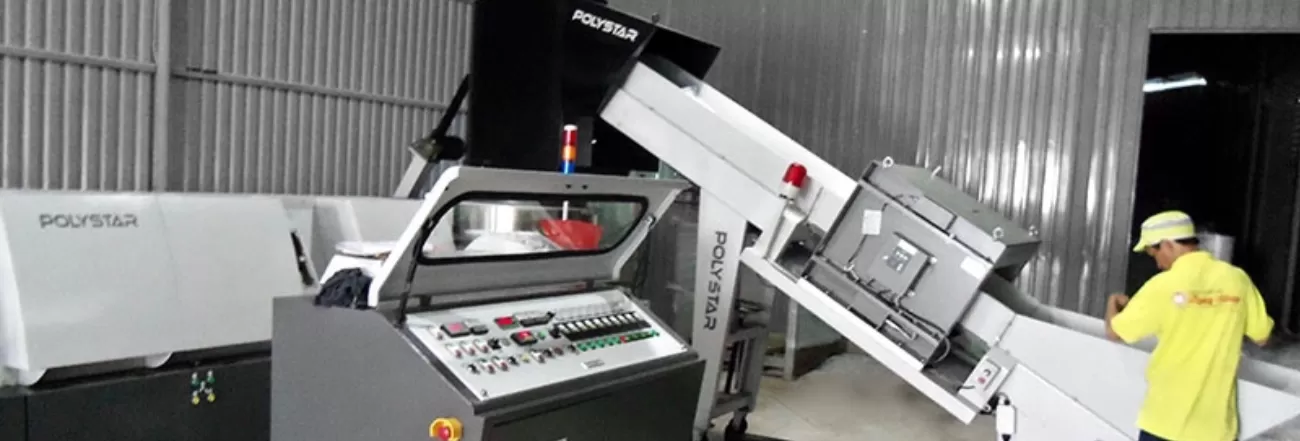
In June 2016, one of the leading Vietnamese flexible packaging film producers installed a POLYSTAR recycling line to recover its in-house film waste generated from blown film and cast film lines. Since the commissioning of the machine in Ho Chi Minh, the company has already recovered more than 1,000 tons of post-industrial film waste, turning rejected post-industrial film scraps back to high-quality pellets for immediate reprocessing in the film extrusion lines.
The flexible packaging film maker produces a wide variety of products including shrinkable film and various types of PE and PP film, both printed and non-printed. With the addition of the new POLYSTAR it can now process all of its in-house waste to ensure the quality of the recycled pellets is consistently high.
POLYSTAR's Demand is Growing in the Vietnamese Market
During the past 13 months, POLYSTAR has already sold more than 10 lines to the Vietnamese market. Another 500kg/hr line will be installed in Hanoi this November.
Beside the Vietnamese market, POLYSTAR has significantly increased its markets share in the Asian market in recent years, working with renowned film producers in Indonesia, Thailand, Malaysia and Vietnam. It has established itself as a premier recycling solution provider thanks to proven success, positive customer feedback and references.
POLYSTAR’s HNT-V is an one-step plastic recycling technology, combining cutting, extrusion and pelletizing. The production waste enters the plastic waste recycling machine from the conveyor belt (for film scraps and rigid plastic regrind) and also through nip roll feeder (for film-on-rolls) at the same time.
Material input is controlled automatically based on the load of the cutter compactor. Through natural heat and friction, the cutter compactor then cuts and densifies the material into a semi-molten condition (a brief gentle heating just below the agglomeration point) for the subsequent extrusion process.
The POLYSTAR recycling line can reprocess a variety of films including printed and non printed high density polyethylene (HDPE), low density (LDPE), polypropylene (PP) and BOPP. Different film compositions, ranging from monolayer, multi-layer to laminated films with different degrees of printing percentage can be recycled into high quality pellets without significant changes in properties.
Cutter Compactor Integrated Recycling Machine - An Advantage for your Business
The cutter compactor subsequently feeds the compacted material directly and consistently into the extruder then into the degassing, filtering and pelletizing processes.
The recycling line is able to turn a variety of films products (of different thickness and printed percentage) into high quality pellets. The Vietnamese packaging supplier is using these recycled pellets for production of T-shirt bags and garbage bags. According to the Vietnamese film producer, it allows the company to save up to 30% in raw material procurement.
POLYSTAR supplies different types of plastic recycling machines for the plastic industry with various types of crushing and shredding technology integration. Both cutter compactor and single shaft shredder integration are provided to meet different recycling applications from the plastic film, woven/raffia and injection sectors. Ranging from monolayer to complex 3 or 5 multi-layered film can be processed with different types of POLYSTAR recycling technology, with a range of output selection from 50kg/hr to 1000kg/hr.