We use cookies and other tracking technologies to improve your browsing experience on our website, By clicking "Accept All," you agree to allow cookies to be placed to enhance your browsing experience on this website to show you personalized content and targeted ads, to analyze our website traffic, and to understand where our visitors are coming from. You can manage your cookie settings below. Clicking "Confirm" indicates your agreement to adopt the current settings.
US Recycler Shares His Experience Using POLYSTAR
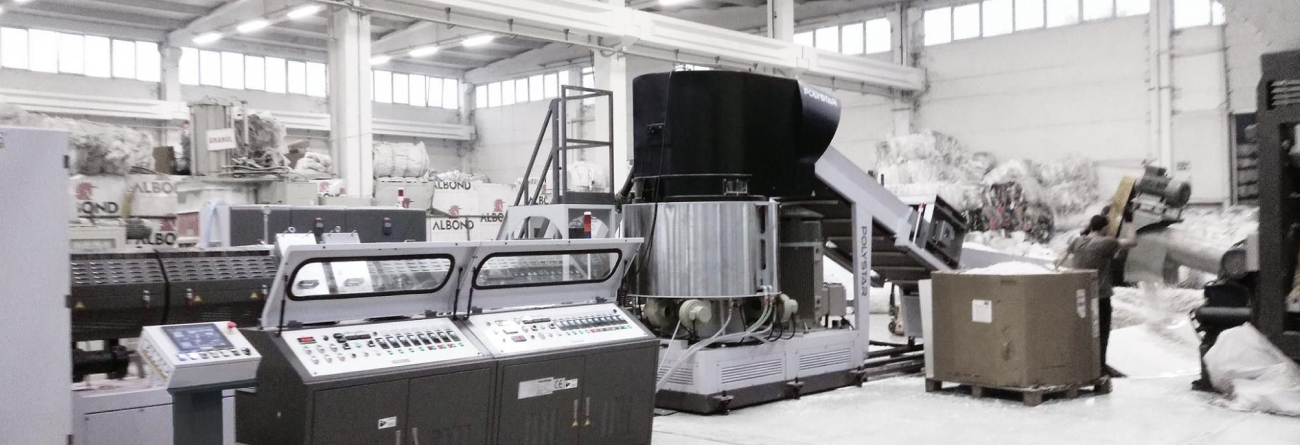
Can you give me your opinion of your POLYSTAR?
Which Model is it?
I have a two-stage extrusion pelletizing system with a cutter compactor. I have added a separate shredder as the PP material we now process is much more difficult to shred and slowed the rate down. When we were processing LDPE, LLDPE, and HDPE film (post-industrial, post-commercial, and post-consumer) we did not have any problem with the compactor maintenance rate.
We have run BOPP film with just the shred drum at over 1500 lbs/hr. We also have a melt filter on the line to remove labels, etc. and it works well with the POLYSTAR. You will likely be processing your own film so you would not need the melt filter unless you were to use recycled content from post-consumer or post-commercial film back into your film.
Output in reality compared to nameplate output kg/h?
We cannot operate the line at nameplate which is 1700 lbs/hr but can operate the line at over 1600 lbs/hr with some materials based upon bulk density. Bulk density often depends upon screen size with a regular shredder and with a shred drum the toughness of the material partly determines how finely it is shredded along with the condition of the blades and how tightly the shredded material is packed into the screw. You will likely find the LLDPE film runs at a slightly slower rate than the LDPE film for this reason. BOPP film will run at 1500 lbs/hr on my line with the shred drum with sharp blades.
Part of the rate determination is the learning curve with the cutter compactor. We have found with ours (I do not know if this will apply to yours) that we can run the shred drum at elevated temperatures to increase the rate and use the water injection system to keep the plastic in the shred drum from melting completely. After the operators have experience doing this they become very adept at maintaining rate. The double vacuum system removes the water from the melt very effectively and we ran wet material all the time when we were running post-consumer LDPE. In fact, we ran wet PP today and it runs fine with the double degassing system. I would definitely recommend the double degassing unit if you will run printed film.
With a compactor the rate at which you feed it is everything. If you overfeed the compactor you will have problems and if the feeding rate varies much you will have problems.
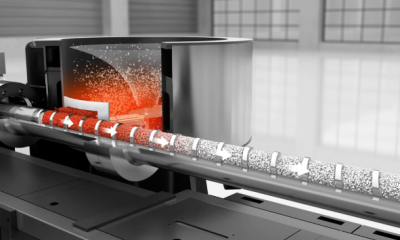