We use cookies and other tracking technologies to improve your browsing experience on our website, By clicking "Accept All," you agree to allow cookies to be placed to enhance your browsing experience on this website to show you personalized content and targeted ads, to analyze our website traffic, and to understand where our visitors are coming from. You can manage your cookie settings below. Clicking "Confirm" indicates your agreement to adopt the current settings.
Thailand - 100% In-House Recycling, Minimal Property Change in Pellets
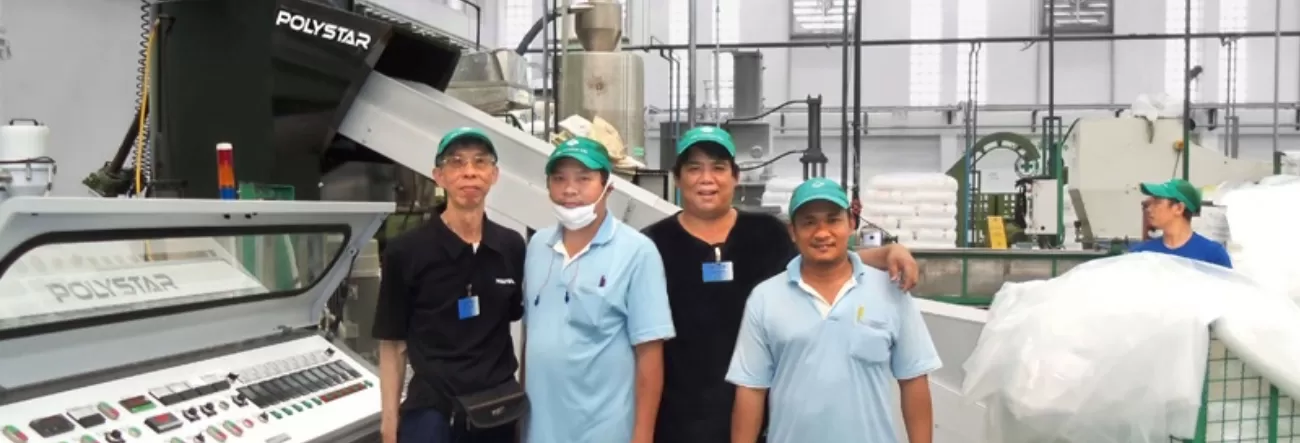
Established in 1980, the ISO 9001-certified HDPE and LDPE bag producer has earned multiple prestigious awards including the Exporter Award and Thai Quality Product. The Bangkok-based PE film manufacturer is one of the market leaders for frozen food bags, sandwich bags, hanging bags, hole punching bags, garbage bags, and disposable and zip bags. Despite its previous successes, the Thai PE bag producer is determined to continuously develop and improve its production to maintain its leader status in product quality.
Transforming Waste into Premium Quality Pellets
The investment of adding a POLYSTAR plastic recycling machine fits perfectly in the quality improvement plan, as production waste is now being processed 100% in-house efficiently with the best possible quality. The return on investment is particularly short because much fewer raw materials are needed for high-end quality film products.
Amongst many economic and technical benefits of using a POLYSTAR recycling line for post-industrial, in-house reprocessing, these are the ones that have the most immediate, strongest impacts on the Thai PE film producer at the moment:
Uniform-sized plastic pellets - POLYSTAR's high-tech pelletizing system ensures that the recycled pellets' sizes are as uniform (same size) as possible. The round-shaped, virgin-like recycled pellets are optimal for reprocessing in extrusion as the shape, size, properties, and color are very close to virgin material.
Minimal material degradation - a higher percentage of recycled pellets can be reused in the production process compared to the recycling machines that the company previously owned. The special screw design, advanced filtration and degassing system ensure that the material is processed at an optimal temperature.
Extremely Simple Operation, One-step Recycling Technology
The production waste enters the plastic waste recycling machine from the conveyor belt (for film scraps and rigid plastic regrind) and also through the nip roll feeder (for film-on-rolls) at the same time. The input is controlled automatically based on the load of the cutter compactor. Through natural heat and friction, the cutter compactor then cuts and densifies the material into a semi-molten condition (a brief gentle heating just below the agglomeration point), which is ideal for the extrusion process that follows. The cutter compactor subsequently feeds the compacted material directly and consistently into the extruder and then into the degassing, filtering, and pelletizing processes.
Minimal Property Change: Recycling without quality loss - Recycled pellets used immediately in blown film lines
With POLYSTAR's plastic recycling technology, the recycled HDPE and LDPE pellets are put directly back into the blown film extrusion process. The gentle recycling process results in minimal material degradation without significant property change. The virgin-like recycled pellets have a reusability of 95% up to 100%.
Part of the film products such as HDPE and LDPE T-shirts and garbage bags are made of a high percentage of recycled material and the quality of the end product remains high.
This new installation was the fifth HNT-V plastic recycling model that POLYSTAR has commissioned in Thailand in the previous 5 months.