We use cookies and other tracking technologies to improve your browsing experience on our website, By clicking "Accept All," you agree to allow cookies to be placed to enhance your browsing experience on this website to show you personalized content and targeted ads, to analyze our website traffic, and to understand where our visitors are coming from. You can manage your cookie settings below. Clicking "Confirm" indicates your agreement to adopt the current settings.
Stretch Film Plastic Recycling Machine - How In-house Recycling Improves Pellets Reusability?
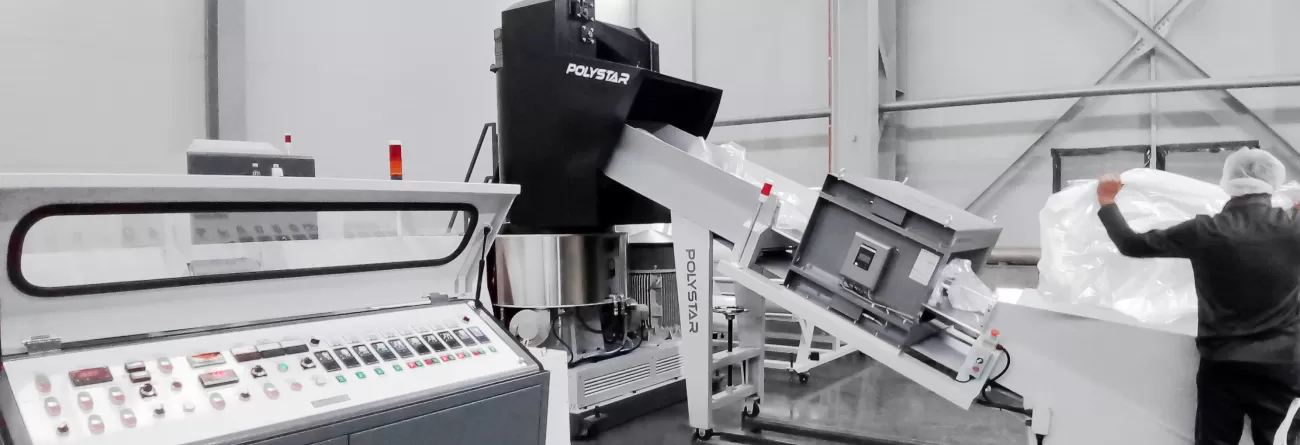
As the largest LLDPE stretch and PE film producer in Taiwan with monthly production of 3,000 tons (achieved with several 5-layer cast film machines from Germany), in-house recycling is valued highly by the 30-year-old film producer as part of the production process to ensure quality and consistency in the end-product remain high.
Ever since the company’s major expansion in 1991, it has been carefully selecting only the best and world-class machine manufacturers in the market as its partners. The company was the first Taiwanese film producer to bring in a five-layer casting extruder from Germany and is now equipped with several multi-layer cast film and printing machines from Europe.
Consistency in Pellets Quality to Re-use in PE Stretch Film Manufacturing
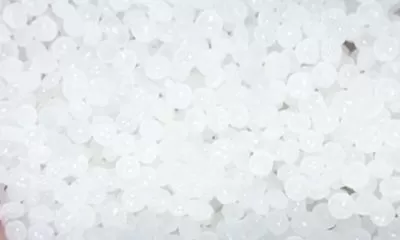
Simple operation and maintenance
Consistency and quality in the recycled pellets
How to Recycle Stretch Film Efficiently?
The defected film-on-rolls are fed automatically via the nip rolls on top of the cutter-compactor, which is then compacted and fed directly into the recycling extruder for further processing and pelletizing. The rest of the occasionally generated scraps are fed via the conveyor belt. The two-way feedings are controlled automatically and simultaneously to prevent over-feeding or insufficient feeding of material into the machine.
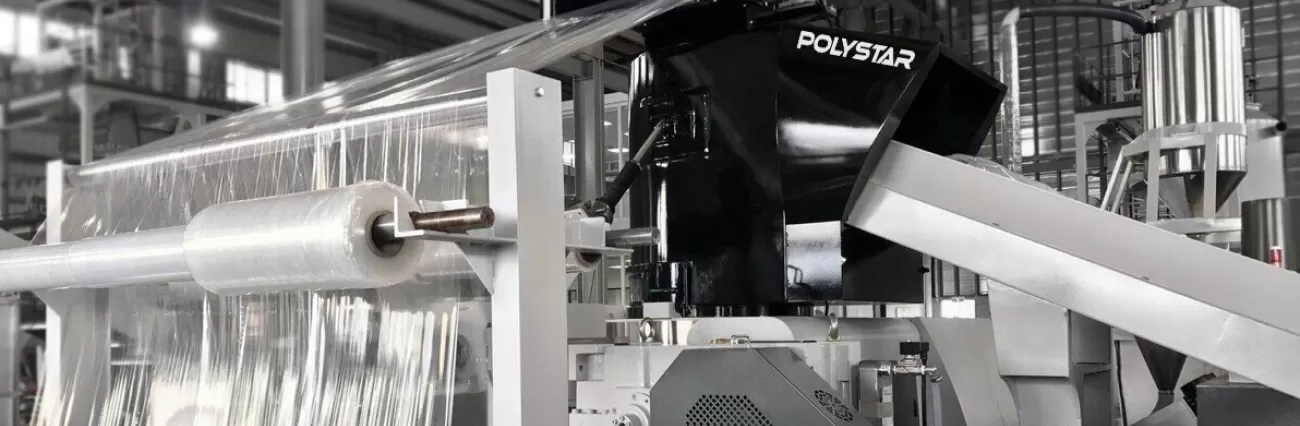
( Internal waste is generated during the production of pallet wrap, shrink wrap, stretch wrap and stretch film)