We use cookies and other tracking technologies to improve your browsing experience on our website, By clicking "Accept All," you agree to allow cookies to be placed to enhance your browsing experience on this website to show you personalized content and targeted ads, to analyze our website traffic, and to understand where our visitors are coming from. You can manage your cookie settings below. Clicking "Confirm" indicates your agreement to adopt the current settings.
South African Recycler Chose Repro-Flex
__23K30f8dbE.jpg)
One of the professional recyclers in South Africa has adopted POLYSTAR’s latest recycling technology Repro-Flex, currently processing post-industrial waste of BOPP, CPP, HDPE and LDPE printed and non-printed, producing more than 550 pounds/hour with the extremely compact recycling machine.
The East London-based recycler has had experience with Italian recycling technology has chosen POLYSTAR after its meeting in K-Show 2013.
Since K show 2013, more than 100 sets POLYSTAR’s cutter compactor recycling machine have been installed worldwide in 70 countries throughout Asia, Africa, Europe, Middle East and Latin America.
Many clients have already ordered their second and third line in 2014 and 2015 after having experienced their first line for 1 ~ 1.5 years. From Germany to the US, from Saudi Arabia to Canada, customers from all around the world are providing positive feedback on their experience with POLYSTAR’s re-engineered recycling machine since 2013.
Overview of POLYSTAR’s latest Repro-Flex Integrated Recycling System
No pre-cutting required: The cutter-compactor design is ideal for light-weight material (film and film flakes)
- One-stage extruder alone can handle highly printed film - less material
- Degradation, energy, and space-saving compared to traditional recycling systems
- Improved filtration and degassing units can handle highly printed material
- Self-adjusting pelletizing speed for higher quality and more uniform-sized pellets
- A more compact design with a higher output
- Improved die-face pelletizing system for PP, BOPP, and OPP film/woven/raffia wastes
Repro-Flex's Advantages over Competitors
1. An Integrated system without the need for pre-crushing
The integration of the cutter compactor directly with the extruder eliminates the need for pre-crushing plastic film. The feeding is therefore much faster and more stable. High throughput with the light-weighted film flakes can be easily achieved by going through densification and compacting process first.
2. High Productivity
A 100mm screw (single stage) can achieve more than 400kg in post-industrial LDPE, where as in the conventional line a producer can hardly achieve 300kg
3. High Automation with Flexible Waste Feeding Methods
The machine can process scrap material on a conveyor and film-on-roll on nip roll film feeder simultaneously. This automates the entire process and is beneficial for producers in terms of labor cost saving, space saving and lowering energy consumption. The machine generates very low noise as it does not require a separate crusher to process the film waste in advance.
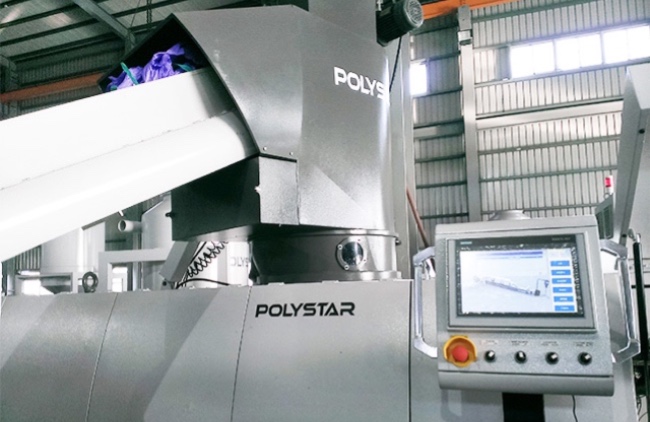
4. Lower Operation Cost (Less Space, Lower Energy Consumption, and Lower Labor Cost)
The POLYSTAR machine can process heavily printed PE/PP film in just one single extrusion stage. This replaces the traditional "two stage" mother-baby extruder pelletizer with less material degradation, as the extrusion process is done in a single stage. At the same time the machine consumes less energy and takes up less space because of its compactness (requires one extruder less and less motor power). In addition, only one person at the feeding section is sufficient for operating the machine.
5. Filtration and Degassing
A continuous filter with two flowing channels reduces operator intervention.
The double-degassing and high-vacuum can effectively process highly printed and humid material. The re-positioning of the filter and degassing eliminates the problem of material leaking in the vent (degassing) area in conventional lines. This allows producers to achieve higher production and process printed film more efficiently