We use cookies and other tracking technologies to improve your browsing experience on our website, By clicking "Accept All," you agree to allow cookies to be placed to enhance your browsing experience on this website to show you personalized content and targeted ads, to analyze our website traffic, and to understand where our visitors are coming from. You can manage your cookie settings below. Clicking "Confirm" indicates your agreement to adopt the current settings.
PP Woven Sack Recycling Machine Commissioned in Nigeria
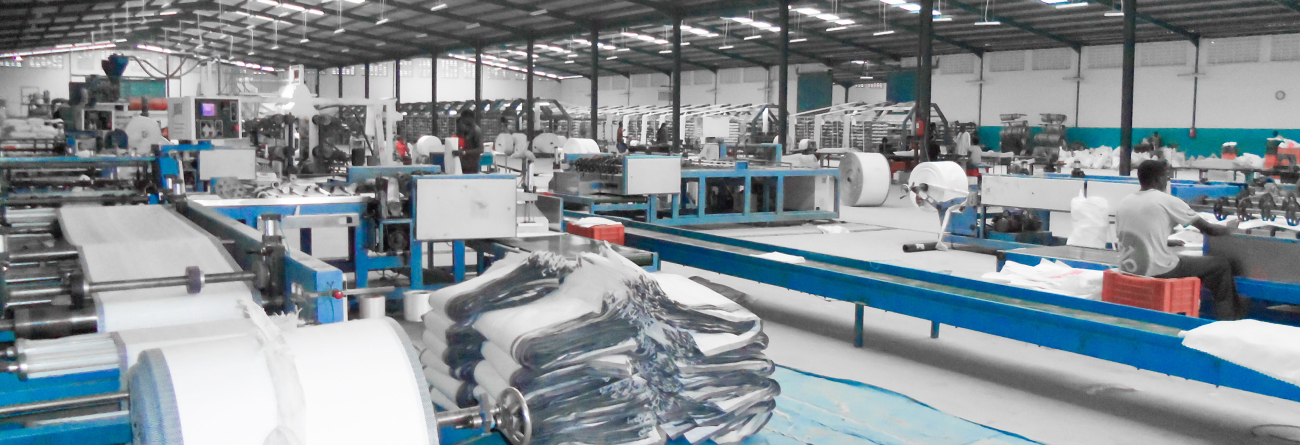
The best way to recycle PP bags / PP sacks
One of the leading PP (polypropylene) woven packaging manufacturers in Nigeria has recently acquired the Repro-One PP sack recycling machine to process its post-industrial waste. The company has focused on the production of PP woven bags and PP jumbo bags for over 20 years. On average, the production lines generate 2 ~ 5% waste from tape extrusion lines, printing lines, and start-up lumps.
It has been costly for the company to send the scraps outside for recycling, as the quality of the recycled pellets is not always consistent and becomes problematic when used again in tape extrusion lines. There are also extra storage, transportation, and logistics costs involved. Since the first PP recycling machine was installed earlier this year, the producer has been recycling 100% in-house and the investment is coming back very quickly. According to the company's factory manager, adding recycling to the production cycle has been a lot easier than expected. It now fits well as a part of all the PP woven sack machinery in operation, further reducing the production cost, and increasing reusability back to the production lines.
PP Woven Bags Recycling System Without Pre-crushing Needs
In-house recycling of PP woven production has become more popular recently among woven bag producers. Many of the producers are looking for a PP woven bag recycling line that can recycle in-house PP waste. Repro-One plastic recycling machines became more and more popular by PP woven bag manufacturers. Due to the high demand for PP woven bag plastic recycling machines, POLYSTAR has been providing PP woven bag plastic recycling machines since 2011. In June 2012, POLYSTAR commissioned its twelfth set of plastic recycling machines in Africa.
POLYSTAR also installed many PP woven bag plastic recycling machines in African countries, such as Egypt, Nigeria, South Africa, Sudan, Swaziland, Kenya, Malawi, and Ethiopia. This PP woven bags recycling system which was produced by POLYSTAR received very positive feedback from the users.
What Makes the Repro-One Special for Recycling PP Bags/Woven Sacks?
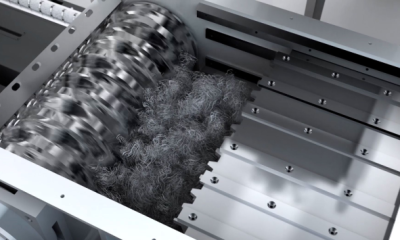
1. One-step, simple solution for PP woven, non-woven, and raffia recycling
A single-step process with shredder + extruder + pelletizer all integrated into one simple, easy-to-operate recycling machine.
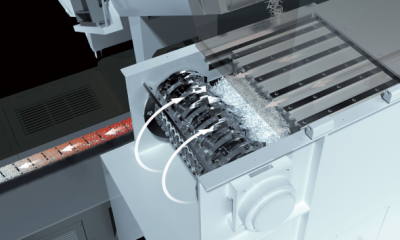
2. Higher reusability back to production lines
This gentle and short, one-step process ensures minimal material degradation, which allows producers to reuse a higher percentage of the recycled pellets back into the production lines and still meet the industrial standards (for example, strength and elasticity of jumbo bags for US exports).
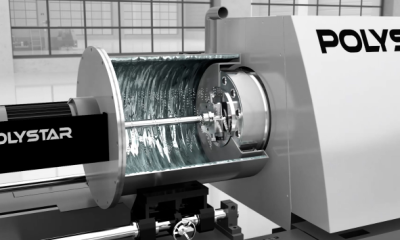
3. Simple-to-use, automatic pelletizing system for PP woven bag recycling
The pelletizing system of the Repro-One prevents PP pellets from sticking to one another, ensuring stable production and output without having to constantly stop the machine for adjustment.
The die-face cutting design of our PP woven bag recycling machine was redesigned specifically to recycle PP woven sacks, bags, and PP raffia waste that are high in MI (melting index). In the past, pelletizing PP material with die-face cutting technology was not as easy as processing HDPE and LDPE.
The Improved Pelletizing Technology has the Following Features and Automation
-
Automatic pelletizing speed adjustment
Prevents pellets from sticking due to the higher melting index of PP material. Produces more uniform-sized pellets without labor intervention.
-
Automatic blade pressure adjustment
Allows the pressure between the pelletizing blades and the die head to remain constant. As a result, there is less machine downtime, easier and faster to change blades.
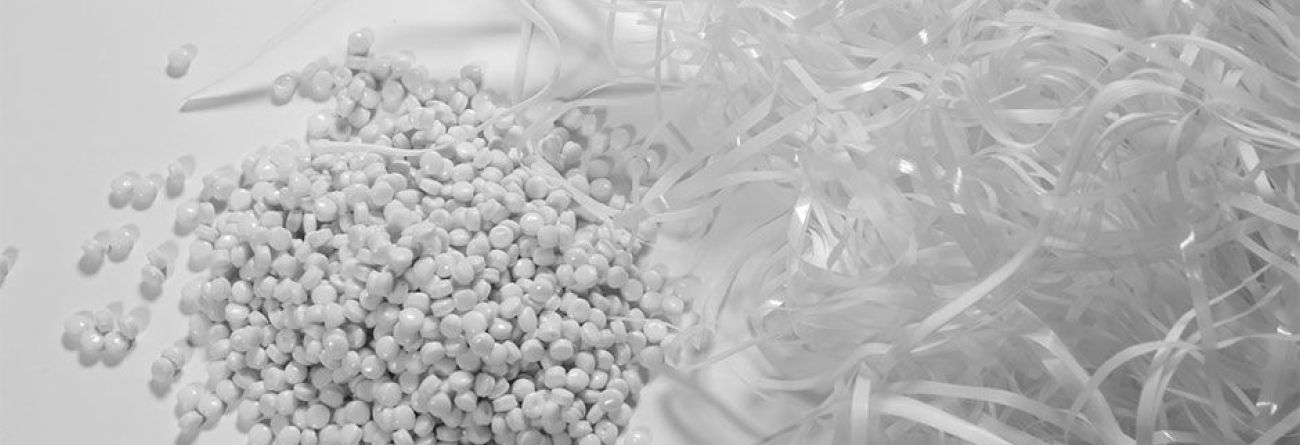