We use cookies and other tracking technologies to improve your browsing experience on our website, By clicking "Accept All," you agree to allow cookies to be placed to enhance your browsing experience on this website to show you personalized content and targeted ads, to analyze our website traffic, and to understand where our visitors are coming from. You can manage your cookie settings below. Clicking "Confirm" indicates your agreement to adopt the current settings.
A New Recycling Line for Heavily Printed Film Installed in the Philippines
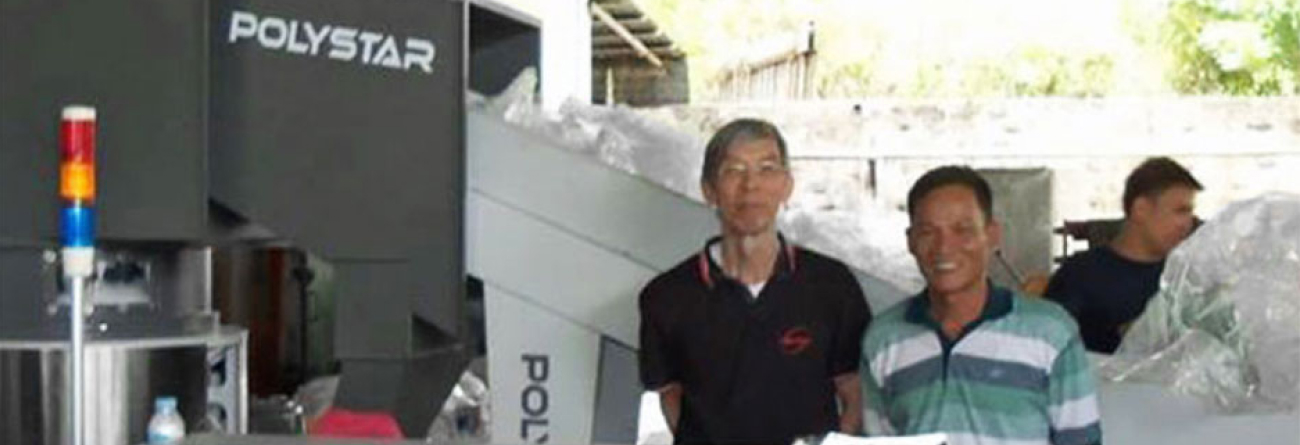
In June, POLYSTAR successfully installed a new recycling line "Repro-Print" in the Philippines. The Philippine-based film manufacturer supplies fully printed film products for food and beverage packaging. The company is equipped with high-performing machines from renowned European suppliers such as Alpine (film extrusion) and printing machines from Fischer & Krecke. The newly-acquired POLYSTAR pelletizing lines are currently processing fully printed rejected film waste generated from in-house. The recycled pellets are put directly back into the film extrusion lines for reprocessing.
POLYSTAR offers a much-improved system for post-industrial film recycling (particularly HDPE, LDPE, PP, and BOPP heavily printed)
Applications:
- Heavily printed HDPE, LDPE, PP, BOPP, and PS film scraps and film on-roll, with film surface fully printed up to 95%. Also suitable for processing lightly printed and unprinted flexible packaging materials.
- Also applicable for raffia, woven bags, and pre-washed film flakes that contain a higher percentage of humidity level.
New Features
The new system "Repro-Print" has three significant improvements from the previous model
-
1. Triple Degassing
In addition to the double degassing in the first extruder, the venting area (the connection between the first and second extruder) serves as a third degassing section to further remove the ink and extra humidity level from the material. -
2. Improved cutter compactor for faster and more stable material feeding
An improved design of the cutter compactor now works superbly with printed BOPP film. The compactor cuts, dries, and compacts the material, enabling a fast and stable feeding from the compactor directly into the extruder
-
3. Filtration before degassing: The re-positioning of filtration before degassing
Ensures a superior degassing effect, producing excellent quality pellets from heavily printed material.