We use cookies and other tracking technologies to improve your browsing experience on our website, By clicking "Accept All," you agree to allow cookies to be placed to enhance your browsing experience on this website to show you personalized content and targeted ads, to analyze our website traffic, and to understand where our visitors are coming from. You can manage your cookie settings below. Clicking "Confirm" indicates your agreement to adopt the current settings.
Efficient In-House Recycling in Chile
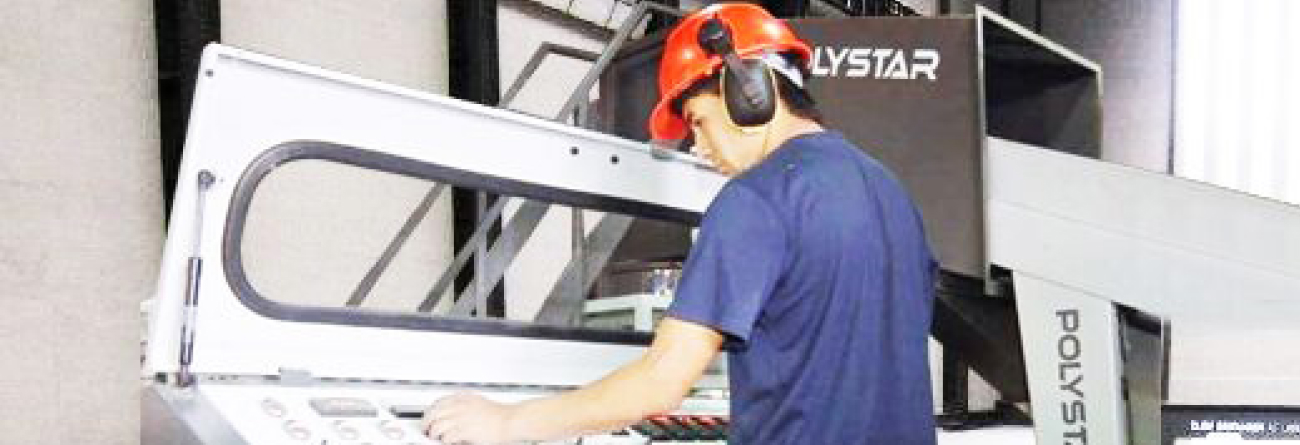
Temuplas, a plastic manufacturer of high and low-density polyethylene bags, with operations in Temuco City, Chile, has acquired POLYSTAR’s recycling pelletizing technology for recovering its in-house production waste.
The increase in the price of primary raw materials forces plastic producers to minimize the use of virgin materials to save costs.
"We decided to bring our recycling plant to process our film waste and at the same time, create surplus production capacity that allows us to collect industrial waste from other producers",
said Mr. Ortiz, general manager of the Chilean company.The successful case of Temuplas shows that even a medium (smaller) sized plastic producer can also recycle its in-house waste thoroughly and efficiently and with a speedy return on investment.
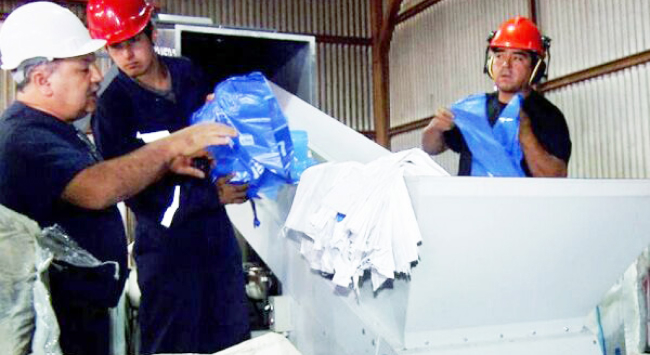
With POLYSTAR’s recycling technology, the recycled pellets are put back into the blown film production process. The soft recycling process results in minimal material degradation without notable property change.
Examples of the waste are PE edge trim and roll (from the blown film), HDPE and LDPE film scraps, leftover waste from punches, and both printed and non-printed film from the production waste processed. Some of the film products such as garbage bags are made of 100% recycled pellets, and the quality of the end product remains superb.
A High-Performing, User-Friendly, One-Step Recycling Technology
“With POLYSTAR’s recycling machine, we are currently processing 300kg per hour at a very stable and consistent rate. POLYSTAR has made recycling much simpler for us”,
says Marcelo Zurita, production manager of Temuplas.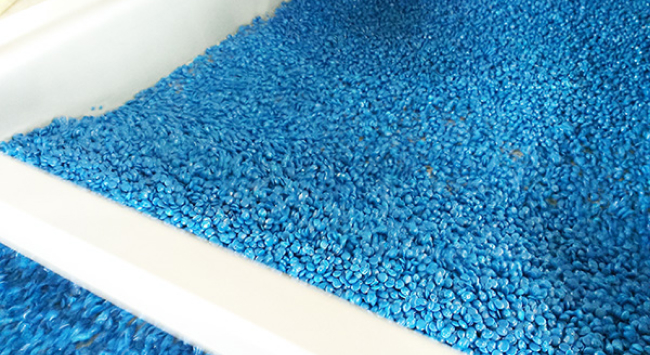
The one-step technology (cutting + extrusion + pelletizing) requires minimal space labor intervention. The waste material enters the machine from the belt conveyor (for film scraps and rigid plastic regrind) and nip roll feeder (for film-on-rolls) at the same time.
The feeding is controlled automatically based on how full the cutter compactor is. The cutter compactor then cuts, dries, and compacts the material into a semi-molten condition (brief heating just below the agglomeration point), which is optimal for the extrusion process that follows. The cutter compactor then feeds the compacted material directly and consistently into the extruder screw.