We use cookies and other tracking technologies to improve your browsing experience on our website, By clicking "Accept All," you agree to allow cookies to be placed to enhance your browsing experience on this website to show you personalized content and targeted ads, to analyze our website traffic, and to understand where our visitors are coming from. You can manage your cookie settings below. Clicking "Confirm" indicates your agreement to adopt the current settings.
Double-head Blown Film Machines are Highly Efficient for T-shirt Bag Makers
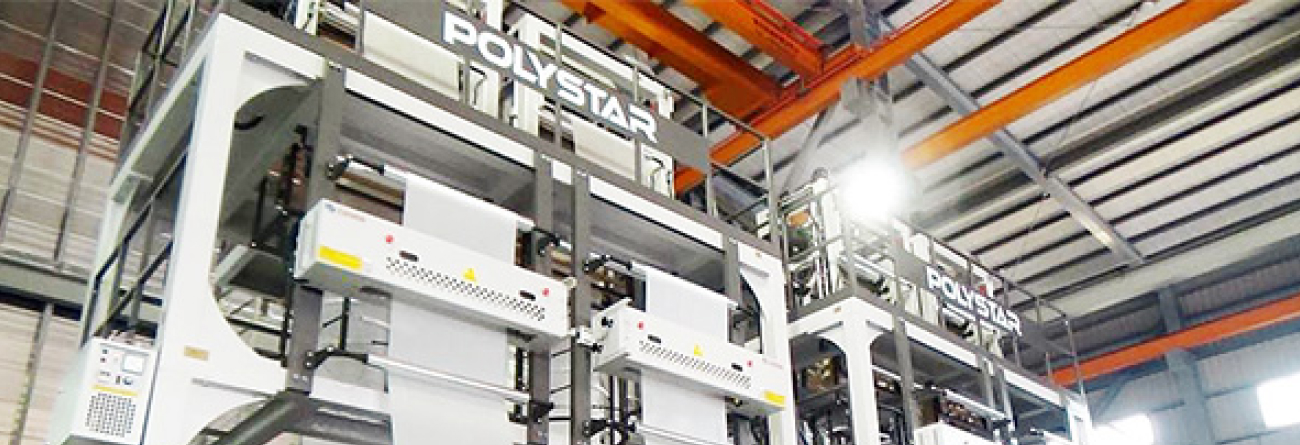
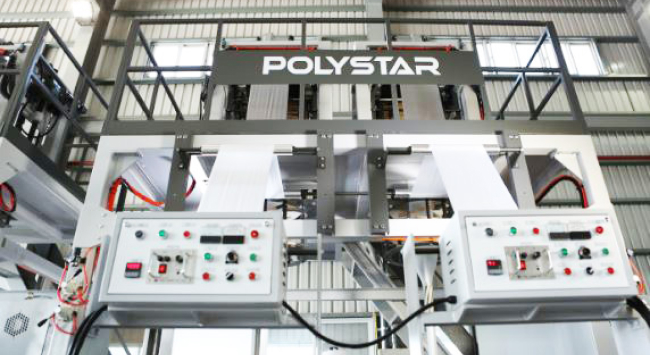
Best Blown-film Range for T-shirt Bags
Single Die Head vs. Double Die Head Extruder
Compared to extruders with a single die head, the double die extruders can achieve higher production capacity when producing film rolls that are small in width, as the high extrusion output is dispersed into two separate channels of the die heads instead of one.
POLYSTAR designs and customizes this type of double-head blown film machine with different screw diameters and roller widths depending on the customers’ requirements. Available in screw diameters of 55mm, 60mm, 65mm, and 75mm and film width from 400mm up to 1000mm on each winder. The double-head blown film machine also allows producers to switch between HDPE and LDPE production as well as produce different film widths on the same machine on each winder simultaneously.
Screw Design for Stable Output on Both HDPE/LDPE
A special screw design is used to provide good mixing and stable output for both HDPE and LDPE materials. Bimetallic treatment is applied to process a higher percentage of recycled material and CaCO3 compound. POLYSTAR uses Siemens/ABB energy-saving motors for the extruders which can reduce energy consumption by up to 5%.
POLYSTAR has installed more than 200 sets of double-head blown film machines in Latin America in more than 15 countries throughout Central and South America.