We use cookies and other tracking technologies to improve your browsing experience on our website, By clicking "Accept All," you agree to allow cookies to be placed to enhance your browsing experience on this website to show you personalized content and targeted ads, to analyze our website traffic, and to understand where our visitors are coming from. You can manage your cookie settings below. Clicking "Confirm" indicates your agreement to adopt the current settings.
Dominican Republic – In-House Recycling Ensures Sustainability of Production Waste
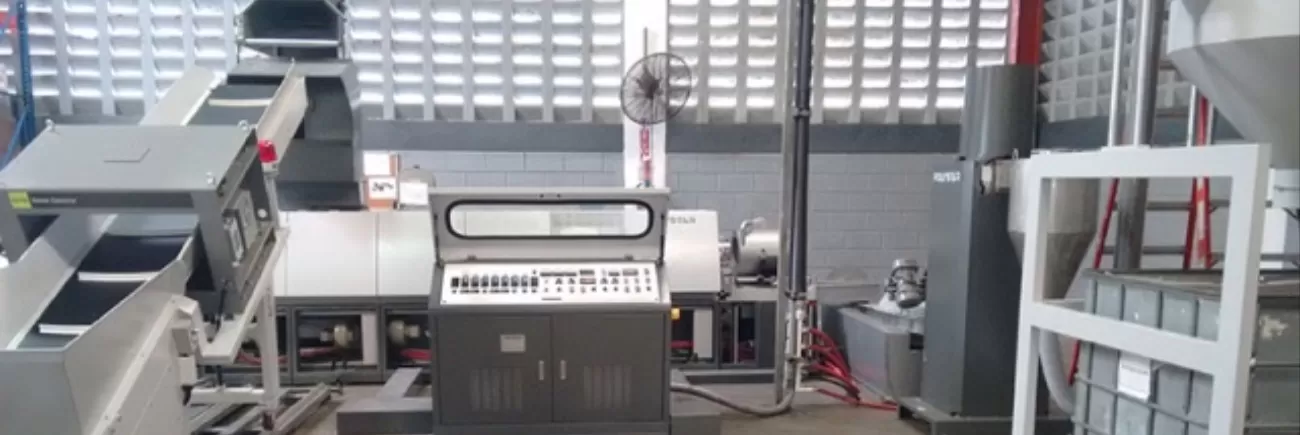
Located in Santo Domingo, Dominican Republic, the packaging film producer has stepped up its in-house recycling effort by working with POLYSTAR.
The 37-year-old plastic producer provides a wide range of plastic packaging and printing products including high and low-density polyethylene film, shrink film, stretch film, flexo printed film, T-shirt bags, garbage bags, patch handle bags, side sealing bags, laminated film, cluster bags, banana film, and many others.
The newly installed POLYSTAR plastic waste recycling machine can effectively and flexibly reprocess a variety of film products including heavily printed, lightly printed as well as non-printed HDPE, LDPE, PP, and BOPP film waste. Different film compositions ranging from monolayer, two-layer, and multi-layer to laminated films with different degrees of printing percentage are reprocessed efficiently in POLYSTAR's Repro-Flex model which produces high-quality recycled pellets.
100% Sustainability: Recycling Without Quality Loss - Recycled Pellets Used for Immediate Blown Film Extrusion
Top Productivity, Flexibility, and User-Friendliness
The One-step Recycling Technology with Easy Operation
The production waste enters the plastic waste recycling machine from the conveyor belt (for film scraps and rigid plastic regrind) and also through the nip roll feeder (for film-on-rolls) at the same time. The input is controlled automatically based on the load of the cutter compactor. Through natural heat and friction, the cutter compactor then cuts and densifies the material into a semi-molten condition (a brief gentle heating just below the agglomeration point), which is ideal for the extrusion process that follows. The cutter compactor subsequently feeds the compacted material directly and consistently into the extruder and then into the degassing, filtering, and pelletizing processes.
In-house recycling Significantly Reduces Production and Labor Cost
Recycling has allowed the company to save about 20~30 percent in raw material procurement. The reclaim of valuable secondary raw material has become indispensable for plastic producers today to stay competitive in the market.
The successful case proves how in-house recycling can be done efficiently and intelligently. The in-house recycling solution saves production and labor cost at the same time with a fast return on investment.