We use cookies and other tracking technologies to improve your browsing experience on our website, By clicking "Accept All," you agree to allow cookies to be placed to enhance your browsing experience on this website to show you personalized content and targeted ads, to analyze our website traffic, and to understand where our visitors are coming from. You can manage your cookie settings below. Clicking "Confirm" indicates your agreement to adopt the current settings.
Al Dana Angle Plastic Factory Closes the Loop of Circular Economy with POLYSTAR in Saudi Arabia
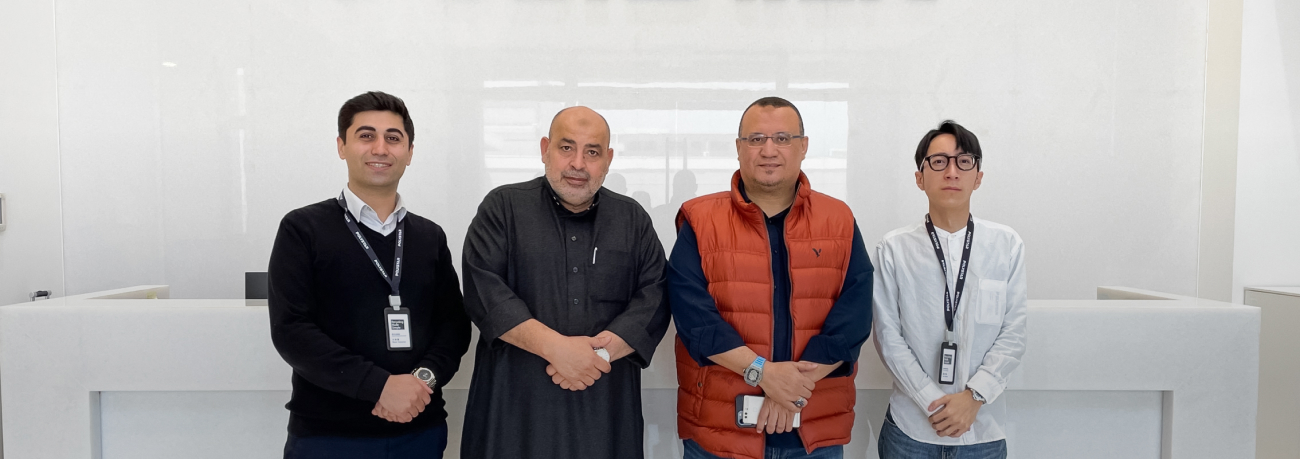
Repro-Flex 85 now mainly processes the LDPE and HDPE film and bag scraps from Al Dana Angle’s production. These wastes turn into high-quality recycled pellets and are used to produce 100% recycled garbage bags. By that, the bag producer not only eliminates plastic waste and achieves its ESG responsibility, but also turns its waste into more profitable value-added products.
Operator Friendly Recycling Machine for In-house Recycling
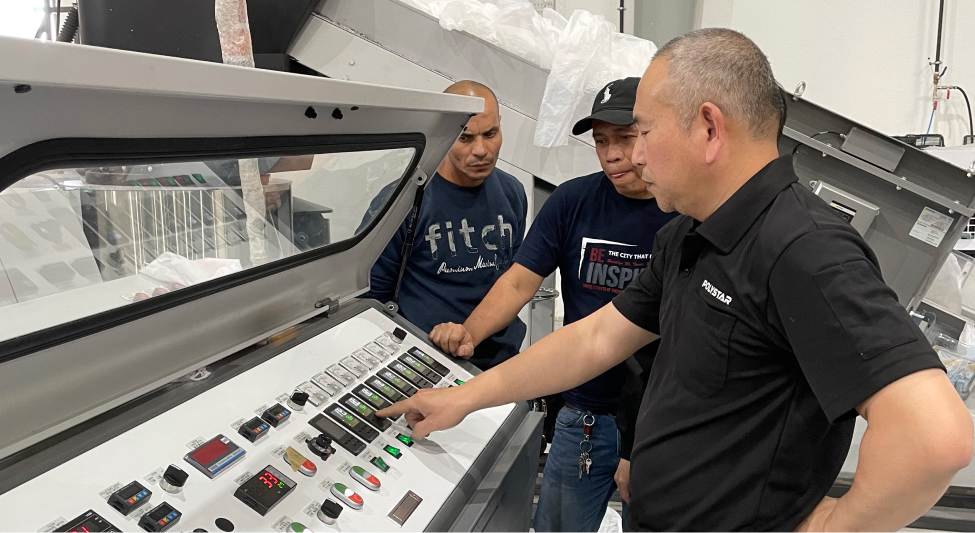
Benefiting the user-friendly design of the POLYSTAR plastic recycling machine, initially Al Dana Angle was able to install and start operating the machine with the online installation and training support of the POLYSTAR after-sales service team.
During the Saudi PPPP exhibition, the POLYSTAR technician paid a visit to the bag producer’s factory for further improvements in operation. Our technician stated that Al Dana Angle operators learned how to use the machine very quickly, operating the machine well and producing perfect recycled pellets.
What are the Benefits of Having an In-house Plastic Recycling Machine?
The new plastic recycling machine has created several benefits for Al Dana Angle’s business as well as for the environment. The common benefits of having an in-house recycling machine in plastic production factories can be summarized below:
1. Eliminating waste and ecological footprint
Production scraps and rejected products can be recycled within the factories. This eliminated the risk of plastic waste being disposed of in nature or landfills. Since plastic waste is less likely to expose contaminants, this also increases the chance of 100% recyclability.
2. Creating reusable plastic pellets for production
The plastic waste can be transformed into recycled pellets and used in the production lines within the factories to produce plastic products containing a certain percentage or up to 100% recycled content.
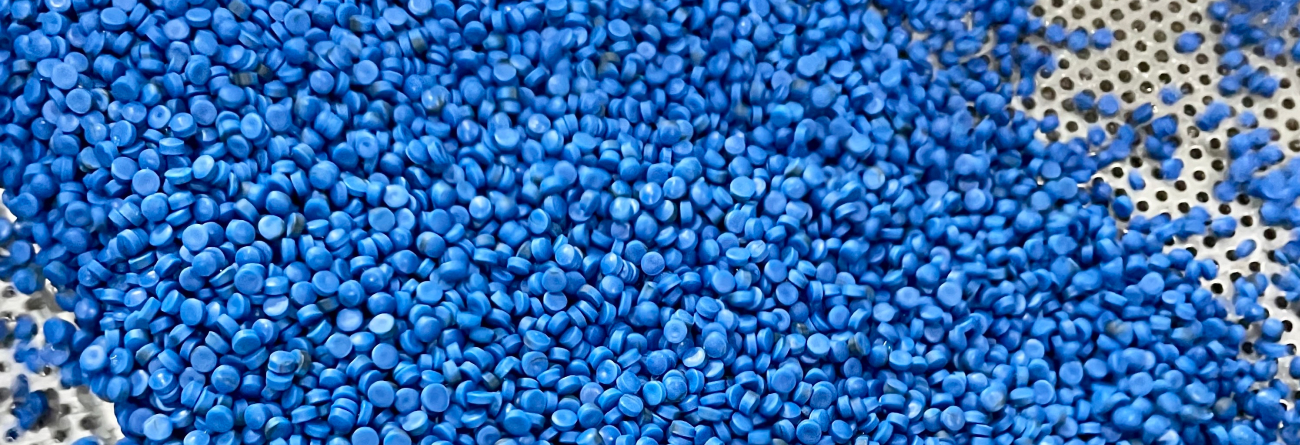
( Recycled Pellets Sourced from Al Dana Angle’s Plastic Production Wastes )
3. Reducing waste handling and material cost
Internal recycling within the factory and creating reusable recycled pellets reduces the cost of buying more virgin materials. Also eliminates the costs of outsourced recycling, buying recycled pellets from outside, waste disposal, and waste transportation costs.
4. Higher quality control on the materials
In-house recycling provides higher quality control on the materials for the plastic producers. One reason is the input waste plastic formula is known and less likely mixed with other types of materials. Another reason is the waste is less likely contaminated since it stays within the factories.
5. Saving factory space
Producers can flexibly decide when to recycle their plastic waste and eliminate occupying the factory space due to over accumulation. The saved factory space can be allocated for other primary operations and product storage.
6. Higher brand reputation and ESG Score
Recycling plastic production scraps and using recycled content in production is becoming a necessity and has been regulated by the authorities in many countries. With the escalating ecological awareness, customers also tend to buy products from companies that adopt these concepts. Therefore, in-house recycling is one of the easy ways to carry your company to the future while increasing your brand reputation and ESG (Environmental, Social, and Governance) score.
( Al Dana Angle Produces garbage bag rolls with 100% recycled pellets )