We use cookies and other tracking technologies to improve your browsing experience on our website, By clicking "Accept All," you agree to allow cookies to be placed to enhance your browsing experience on this website to show you personalized content and targeted ads, to analyze our website traffic, and to understand where our visitors are coming from. You can manage your cookie settings below. Clicking "Confirm" indicates your agreement to adopt the current settings.
ABA Blown Film Machine – What’s the Advantage?
For PE bag production, single layer blown film machine has been the most common type of extruder to use. It is probably still the best machine for products such as fruit and vegetable bags (perforated bag-on-roll) that use mainly virgin materials with low film thickness ranging from 6 to 18 microns. Single layer machine is also the favorable choice for biodegradable bag production.
Single Layer vs ABA Extruder for Bag Production, Which One is Better?
Even though single layer extruder is more than enough for general bag production, ABA co-extrusion (3 layer) machine has its advantage over one layer machine for certain applications like garbage bags, shopping and T-shirt bags that are higher in thickness (20 to 100 microns) or require more film strength. In markets such as Australia and the UK, producing larger-sized garbage bags with ABA co-extrusion lines has already become the industrial standard.
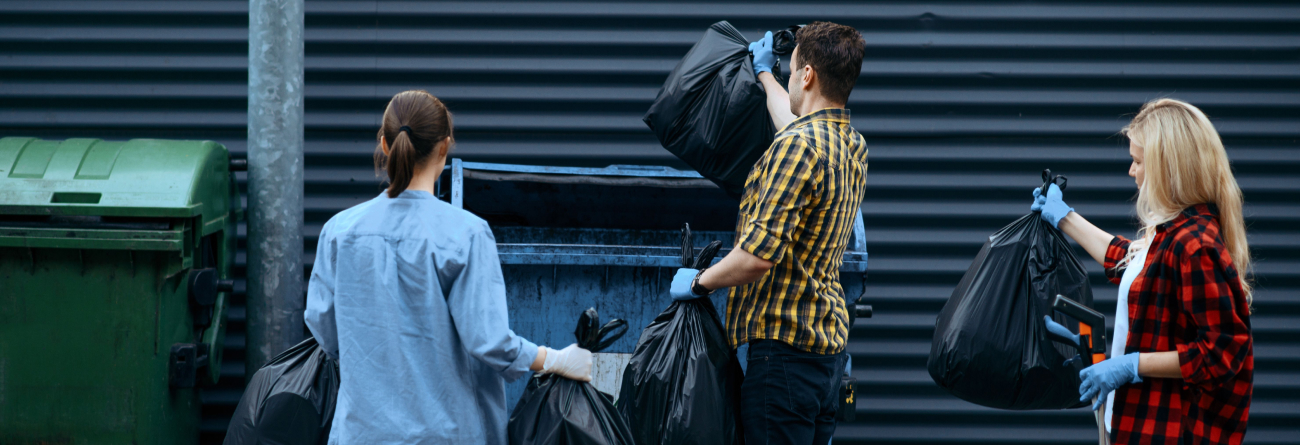
Using More Recycled Materials
A Simple Structure Comparison - Single vs ABA Extrusion Machines
Single Extrusion Machine
|
ABA Co-Extrusion Machine
|
|
Number of Extruders | 1 | 2 |
Film layer produced | 1 layer | 3 layers (A-B-A) |
Film strength | Lower comparing to ABA and ABC | Higher than mono layer at the same film thickness, same as ABC in most PE bag applications |
Applications |
|
|
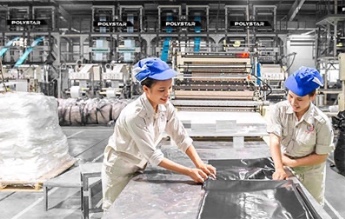
What makes the ABA Machine Special For Bag Production?
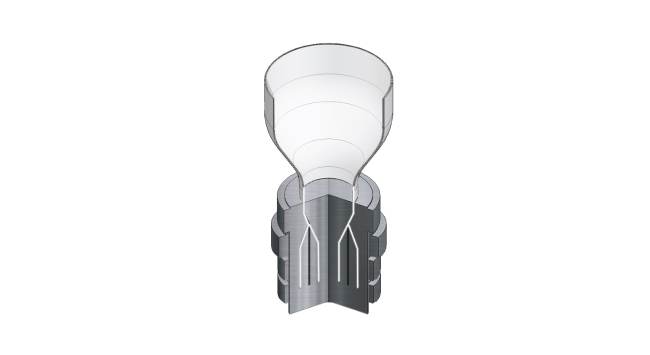
Cost Saving
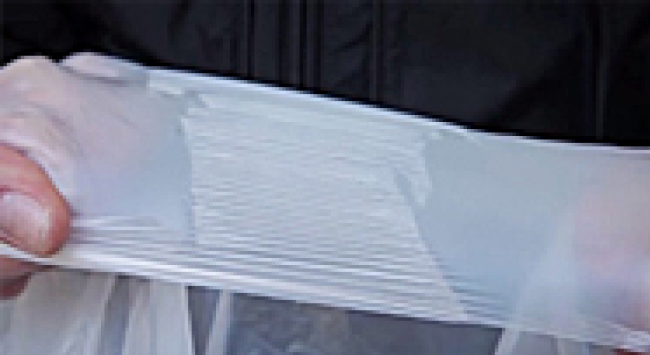
Stronger Film
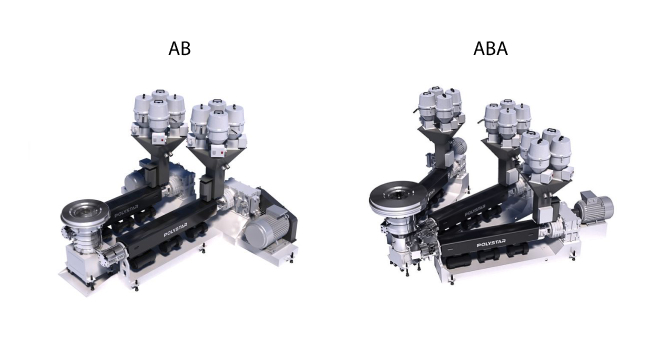
Lower Cost than ABC
A Simple Cost Comparison- Single vs ABA Extrusion Machines
Single Extrusion Machine
|
ABA Co-Extrusion Machine
|
|
Machine Cost | Lower | Higher |
Raw material cost | Higher Less recycled material or CaCO3 can be used for film production |
Lower More recycled material or CaCO3 can be used for film production |
Advantages | Lower cost on machine investment, lower power consumption and less space occupied. | Higher in film strength comparing to mono layer. Lower machine cost comparing to ABC while meeting the requirement for higher film strength and the ability to use more recycled material to reduce cost. |
Suggestions | Mono layer is enough for many applications. Especially for thinner film. | ABA is the better choice when producers are looking to produce film with higher strength.Best for thicker HDPE and LDPE film Cost-effective. |
The Main Advantages of ABA Comparing to Single Layer Machines are
- Cost saving
Virgin material is applied mainly on the outer (thin) layers which is relatively a small percentage of the film composition. These thin layers can cover the middle layer well enough for shiny film surface and good sealing.
- Stronger
Higher resistance comparing to single layer film products of the same thickness.
- Better material mixing
With co-extrusion process to produce better quality film (in which the material is more evenly distributed on the surface), especially when using recycled materials. The effect is very similar to ABC for bag applications.
Bag producers in India, Türkiye and Russia Leading the Way for Using ABA
Vietnam, Indonesia and GCC are on the Rise
The usage of ABA co-extrusion machines for shopping bag production has already been very popular for years in markets like India, Türkiye and Russia. In the gulf region such as Saudi Arabia and Oman where thicker shopping bags are produced are also in high demand. In Asia, Vietnamese producers who focus on exports markets for Australia, Europe and the US are also adding ABA machines their production.
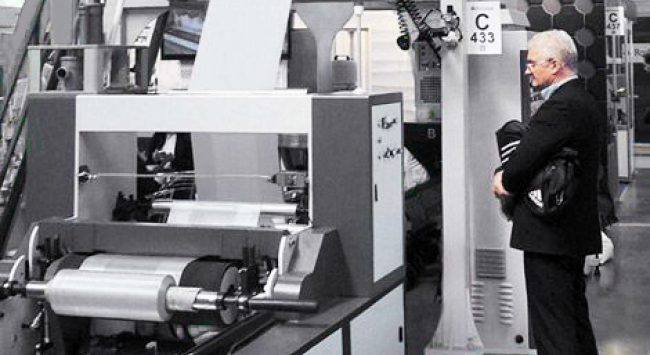
3 of the Most Popular ABA Models for Bag Production
ABA Model |
Extruders
|
Film width range
|
Film width range
|
Machine cost
|
Eco-X Mini 45-55-800 | Ø 45mm + Ø 55mm | 200-650 mm |
T-shirt bags, shopping bags
|
Lowest
|
Eco-X 45-55-1100 | Ø 45mm + Ø 55mm | 200-1000 mm |
Garbage bags, shopping bags
|
In the middle
|
Eco-X 55-65-1500 | Ø 55mm + Ø 65mm | 400-1300 mm |
Garbage bags, shrink film
|
Highest
|
Layer ratio | 1 : 3 : 1 to 1 : 6 : 1 |
Single Layer Machine is Still Better for Some Applications
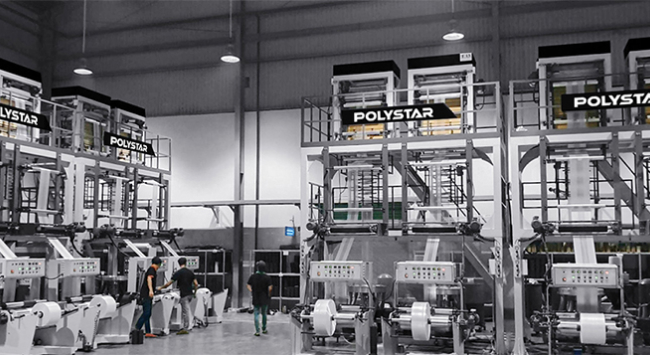
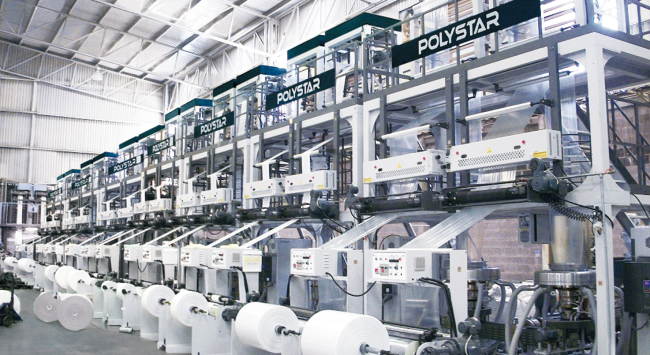
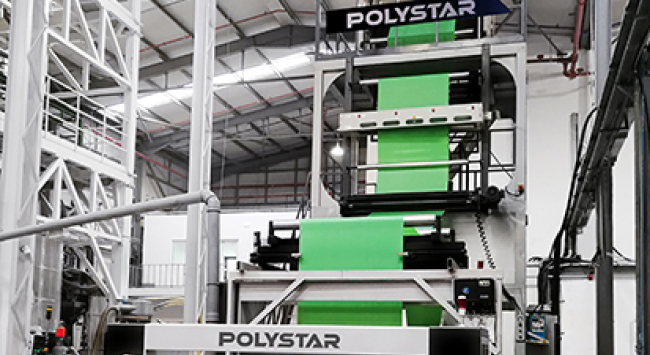
A Combination of ABA and Single Layer Usage is the Key
-
Indonesia-based producer Cahaya Kharisma who produces over 2,000 tones of plastic bags per month, uses both ABA 3-layer extrusion and single layer extrusion machines for different types of bags, having found the right machine for each specific product to maximize production efficiency and reduce cost.
-
A producer in Vietnam is using up to 80% of recycled materials in mono layer extruder, thanks to the special screw design.
Read More
- PE bag producers step up in quality and efficiency in Vietnam - Successful stories
- Mexican Shopping Bag Producer Installed 13th POLYSTAR - Successful stories