We use cookies and other tracking technologies to improve your browsing experience on our website, By clicking "Accept All," you agree to allow cookies to be placed to enhance your browsing experience on this website to show you personalized content and targeted ads, to analyze our website traffic, and to understand where our visitors are coming from. You can manage your cookie settings below. Clicking "Confirm" indicates your agreement to adopt the current settings.
A New Milestone - Success in the Chilean Recycling Market
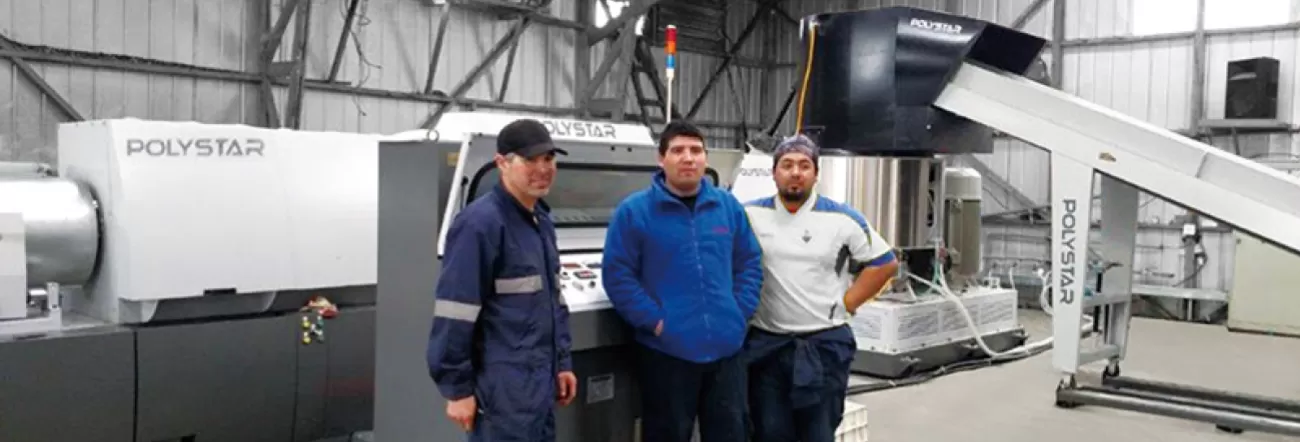
Following a successful exhibition at FullPlast (Chile), POLYSTAR has reached a new milestone with the 15th installation of its new-generation recycling machine in the Chilean market, in only 22 months.
With strong after-sale and technical support from its local Chilean representative, POLYSTAR has established itself as a premium brand of recycling line that offers reliable and high-performing equipment in the market with proven success and satisfied customers.
Efficient In-house Recycling
In the example of Temuplas, a plastic manufacturer of high and low-density polyethylene bags, with operations in Temuco city, Chile, has acquired POLYSTAR’s plastic recycling machine for recovering its in-house production waste as well as waste collected from outside. The increase in the price of raw materials forces the plastic producer to cut down the use of virgin materials to reduce costs.
Recycling has allowed Temuplas to save about 30 percent in raw material buying. The reuse of valuable secondary raw materials has become indispensable for plastic producers today to stay competitive.
Recycling Withoug Quality Loss: Ideal Recycled Pellets for Blown Film Extrusion
With POLYSTAR’s recycling technology, the recycled pellets are put back into the blown film production process. The soft recycling process results in minimal material degradation without notable property change.
Examples of the waste are PE edge trim and roll (from the blown film), HDPE and LDPE film scraps, leftover waste from punches, and both printed and non-printed film from the production waste are processed.
Some of the film products such as garbage bags are made of 100% recycled pellets, and the quality of the end product remains superb.
A High-Performing, User-Friendly, One-Step Recycling Technology
The waste material enters the plastic recycling machine from the belt conveyor (for film scraps and rigid plastic regrind) and nip roll feeder (for film-on-rolls) at the same time. The feeding is controlled automatically based on how full the cutter compactor is. The cutter compactor then cuts, dries and compacts the material into a semi-molten condition (a gentle heating just below the agglomeration point), which is optimal for the extrusion process that follows. The cutter compactor then feeds the compacted material directly and consistently into the extruder screw.