We use cookies and other tracking technologies to improve your browsing experience on our website, By clicking "Accept All," you agree to allow cookies to be placed to enhance your browsing experience on this website to show you personalized content and targeted ads, to analyze our website traffic, and to understand where our visitors are coming from. You can manage your cookie settings below. Clicking "Confirm" indicates your agreement to adopt the current settings.
Turkish Flexible Package and Courier Bag Producer Now Recycles Production Wastes In-house
Global polymer price increase and the obstacles to reach out the resources, push many manufacturers to find alternative solutions. One of the most effective methods is in-house recycling of factory production wastes.
Istanbul, Esenyurt based flexible package and courier bag producer Sürmeli Plastik has also started to recycle its own production wastes within the factory by Repro-Flex 100. 15 years old fast-growing bag manufacturer has a variety of product lines including flexible packages, patch and soft handle bags, punched-out handle bags, courier bags, exam bags, gift packages, shrink films and document pouches. These productions took place in 6.000 m2 indoor area meets the customers from domestic and abroad markets, the bag producer manufactures especially for the European well-known brands.
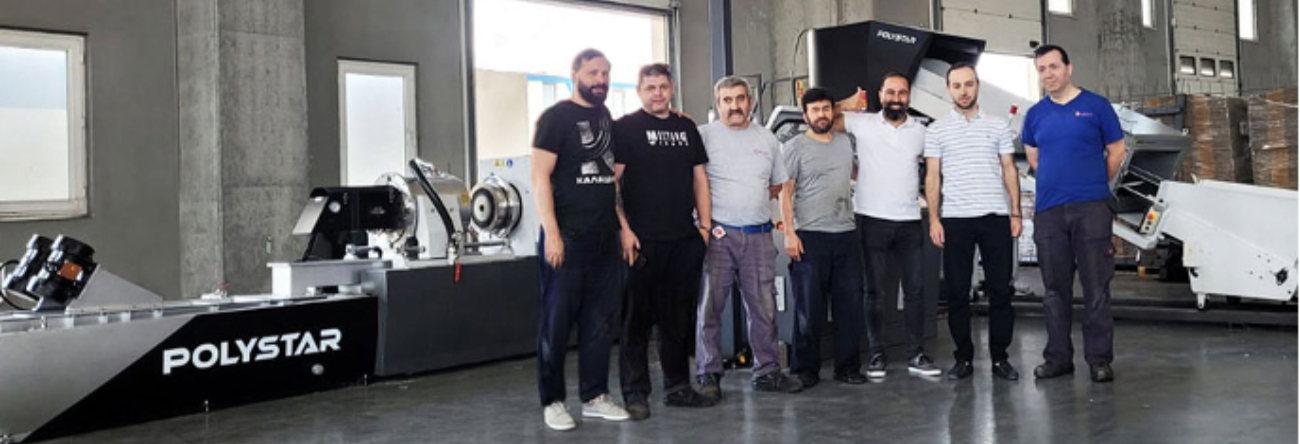
( Repro-Flex 100 Installation in Istanbul )
Which Machine is Most Suitable for In-house Recycling?
The plastic scraps from the cargo bags, shopping bags and gift bags to recycle are made of several variations of PE materials, and contain OPP and PP adhesive tapes on them. Moreover, these plastic scraps are clean (not contaminated by dirt, oil, etc.), dry (no moisture from the washing lines) and have varied printed surface. Some of the bags are slightly printed, and some of them have up to 50% of printed surfaces.
The crucial question in bag producers’ mind was ‘What is the right machine to recycle several different types of bags?’ For that reason, the producer has evaluated the machines that the outsourced recycling companies have been running (including local, European and POLYSTAR recycling machines). Among them, the final pellets quality found stable and satisfactory from the two recyclers who are using POLYSTAR Repro-Flex plastic recycling machines.
Properties of the materials that you can reprocess with Repro-Flex
Repro-Flex(Single Stage)
|
Repro-Flex Plus(Two Stage)
|
|
Humidity | 3% | 5% |
Printed Surface Area | 30%(Standard Dual-piston Filtration) 60%(Filter Repositioned technology) |
Less than 1% |
Contamination | Less than 1% | Less than 1% |
The plastic bag manufacturers asked POLYSTAR for a feasible solution for its varied recycling needs. After evaluating Repro-Flex recycling machine’s standard, filter repositioned and two-stage (Repro-Flex Plus) options, the bag producer found out Repro-Flex model with filter repositioning technology is the right fit for its requirements.
How does Repro-Flex Plastic Recycling Machine work?
Repro-Flex is a cutter compactor integrated compact and one-step plastic recycling machine. The machine combines cutting, extrusion and pelletizing processes into one compact and efficient recycling line. The cutter compactor of the recycling machine prepares (pre-conditions) the material into an ideal condition for the extrusion process and feeds the material directly into the extruder with a centrifugal force. Compared to the conventional recycling machines, this integrated system does not require a separate crusher (agglomerator), and therefore, eliminates the problem of inconsistent feeding (over-feeding or insufficient feeding).
-
Consistent feeding and pelletizing are the key for high quality pellets
Repro-Flex is designed for maximizing feeding and pelletizing speeds and pressures automatically, without the requirement of operator intervention. The waste material can be fed to the compactor by the belt conveyor and the nip roll feeder at the same time. The feeding is controlled automatically based on how full the cutter compactor is. The cutter compactor then feeds the material directly and consistently into the extruder screw. The integration of the cutter compactor and screw extruder ensures extremely fast and stable feeding, the tangentially connected extruder is continuously filled with pre-compacted material. This results in a much higher production output comparing to conventional recycling systems on the market.
What materials can Repro-Flex Reprocess?
Repro-Flex specially designed for reprocessing variety of post-industrial and post-consumer plastic materials. These include printed and non-printed PE & PP film, multi-layered film, shrink film, stretch film, PE and EPE, EPS, EPP foam, PP raffia regrind, thermoformed PS, PP materials, soft irrigation pipe, pre-shredded regrind, washed and dried film flakes from washing lines.
-
PE & PP Film
-
PP Raffia Regrind
-
Printed film
Simple Machine Installation and Training
This June, Repro-Flex 100 cutter compactor plastic recycling machine has already installed in bag producers’ factory located in Istanbul, Esenyurt and started running to recycle in-house wastes generated from the production of flexible packages, handle bags, courier bags, exam bags, gift packages, shrink films and document pouches with 300~350 kg/hr output capacity. The plastic recycled pellets will be traded in the market to create circular economy and profit for the bag producer.
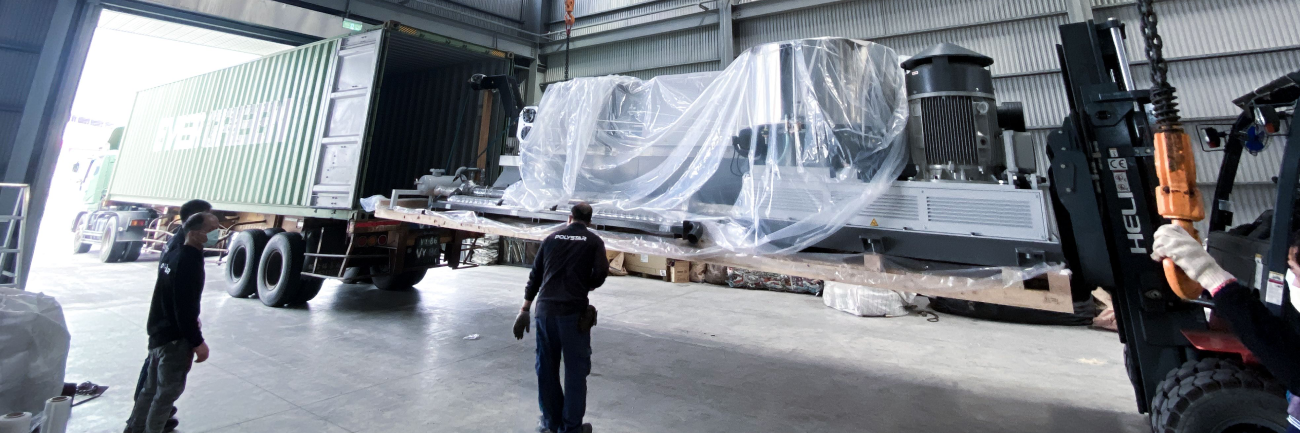
POLYSTAR machines are designed for not only easy operation but also easy installation, which can be completed within 2~3 days upon arrival. When the recycling machines unloaded from the container, customers only need to assemble the three main sections that are disassembled for easy transportation. POLYSTAR also provides fully detailed 3D explosive drawings (with each part clearly marked and labeled), as well as pre-recorded instruction videos of installation, start-up, operation, trouble shooting and regular maintenance videos in which the customers operators have full access by simply scanning a QR code from their mobile phones. The user-friendly design allows operators to quickly become familiar with the machine operation.
Although the easy installation, because this was the first recycling machine of the plastic bag producer, our local Turkish agent carried out the installation process with the operators of the customer. Thanks to user-friendly interface, the operators of the bag producer was able to be trained in a short time and now run the machine smoothly.
Read more