We use cookies and other tracking technologies to improve your browsing experience on our website, By clicking "Accept All," you agree to allow cookies to be placed to enhance your browsing experience on this website to show you personalized content and targeted ads, to analyze our website traffic, and to understand where our visitors are coming from. You can manage your cookie settings below. Clicking "Confirm" indicates your agreement to adopt the current settings.
Two-stage Recycling Machine
Two-stage. One-step
Recycling Processes of Repro-FlexPlus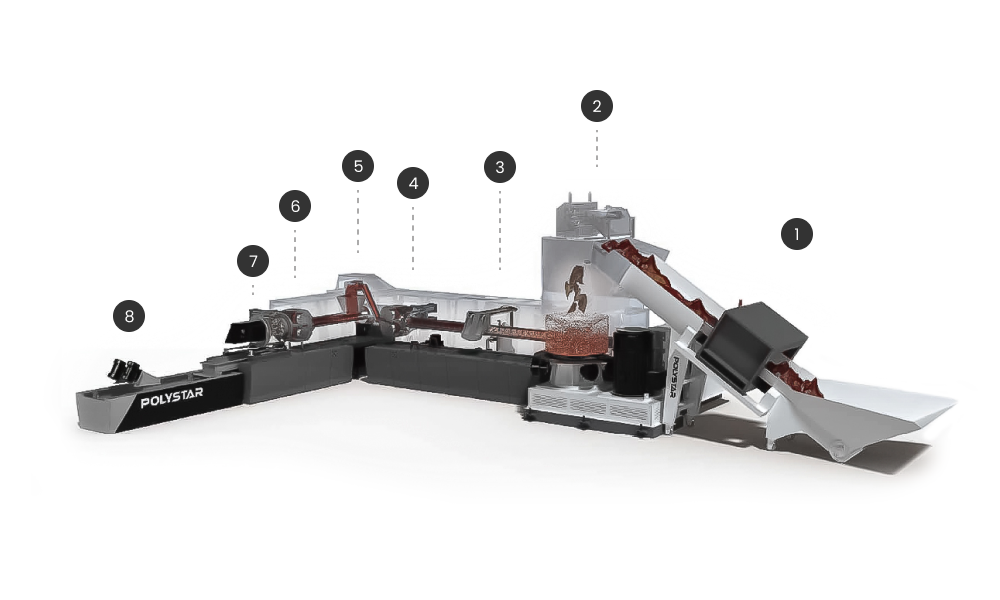
-
1. Belt Conveyor Feeding
With belt conveyor: Feeding of scraps is easy and automatically controlled -
1. Nip Roller Feeding
Film-on-rolls can be fed with a nip roll feeder at the same time. -
2. Cutting and Compacting
Cutter compactor with rotary knives & direct feeding to extruder: Cuts, dries, and compacts the material which enables a fast and stable feeding from the compactor directly into the extruder.
-
3. Degassing
Two-zone degassing (double-vented degasification): Able to process films with larger printed area and some water content. -
4. Filtration
Screen change with dual channel system :
For non-stop operation and prevents material from leaking. -
5. Third Degassing
In addition to the double degassing in the first extruder, the venting area (the connection between the first and second extruder) serves as a third degassing section to further remove the ink and extra humidity level from the material.
-
6. Second Filtration
The extra filtration on the second extruder ensures better pellet quality. Therefore, giving more stable production when re-used again in production lines. -
7. Die Face Pelletizing
Automatic pelletizing speed adjustment: Produces more uniform-sized pellets without labor intervention.Automatic blade pressure adjustment: Less machine downtime, easier to change and adjust knife. -
8. Recycled Pellets
The recycled plastic pellets can be put directly back into the production line such as blown film extrusion and pipe extrusion and injection molding.
Advantages of Two-stage Recycling Machine
-
Special Design:
Two-stage cutter compactor integrated plastic recycling machine for heavily printed film, laminated film, and post-consumer waste. This plastic pelletizing system includes two extruders, three degassing zones, and two filtration units to enhance filtration and degassing ability. This makes plastic recycling machines superior to recycle such as heavily printed PE/PP films, multilayer laminated films, humid pre-washed HDPE/PP flakes, and many other post-consumer wastes.
-
Integrated Cutter Compactor:
For recyclers who process washed and fully printed post-consumer waste, POLYSTAR offers an option of adding a second extruder to the Repro-Flex model. Also having a cutter compactor built in and operating with the same working principles, the two-stage model Repro-Flex Plus has a total of three degassing zones and two filtration steps throughout the entire recycling process. This model is also ideal for processing post-industrial laminated/multi-layered waste.
-
Reduces Ink and Moisture Level:
When processing post-consumer materials, the cutter-compactor reduces the ink and moisture level of the material coming from the washing lines, such as washed flakes (from film and woven bags) as well as regrind waste from milk and shampoo bottles. At the same time, it stabilizes the material being fed into the extrusion pelletizing line to ensure consistent production output and better pellets quality.
Plastic Recycling Machine designed for processing up to 95% printed surface material
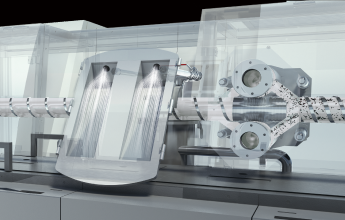
1. Filtration before Degassing
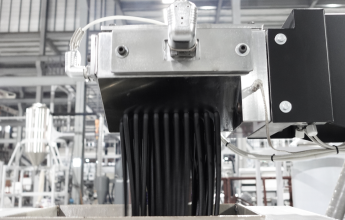
2. Triple degassing
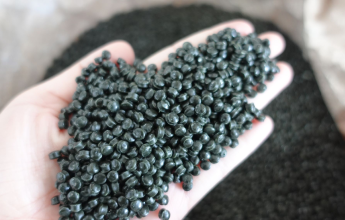
3. Improved cutter-compactor for faster and more stable material feeding
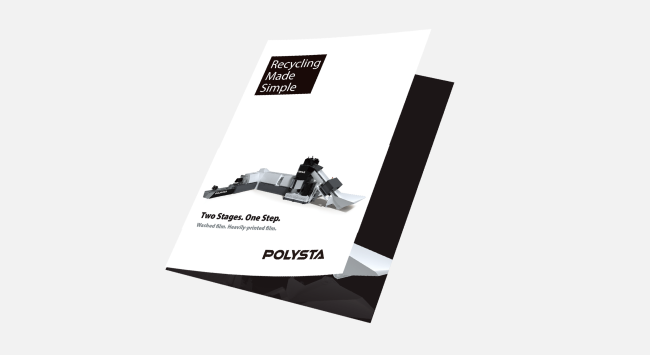
Repro-Flex Plus Catalog
-
PE/PP Printed Film Rolls
-
Printed Waste Bags
-
Humid Pre-washed Flakes
-
Printed Multilayer film
-
Printed Shrink Film
-
Garbage Bag
-
Agricultural Film
-
Printed Food Packaging
-
Printed Woven Bag