We use cookies and other tracking technologies to improve your browsing experience on our website, By clicking "Accept All," you agree to allow cookies to be placed to enhance your browsing experience on this website to show you personalized content and targeted ads, to analyze our website traffic, and to understand where our visitors are coming from. You can manage your cookie settings below. Clicking "Confirm" indicates your agreement to adopt the current settings.
Hard Plastic Recycling Machine
Hopper Feeding Recycling Machine
Recycling Processes of Repro-Direct
-
1. Direct Feeding
- By screw feeder or conveyor belt
- Stable feeding by level.
-
2. Double Degassing
Able to process both printed and non-printed material. -
3. Two-channel Filtration
- Filter with the dual-channel system.
- For non-stop operation and reducing machine downtime.
-
4. Pelletization
Automatic pelletizing speed adjustment:Produces more uniform-sized pellets without labor intervention.Automatic blade pressure adjustment:Less machine downtime, easier to change and adjust knives. -
5. Recycled Pellets
The plastic pellets can be put directly back into the production line such as blown film extrusion and pipe extrusion.
The Advantages of Hard Plastic Recycling Machine
Machine Details
The Repro-Direct model is a universal recycling pelletizing machine suitable for pre-crushed, heavy rigid regrind scraps such as plastic bottles, pipes, containers, and lumps in the form of granules. Applicable materials are mainly HDPE, LDPE, PP, PA, PC, PU, PBU, ABS, and others.)
It can also process light-weighted soft packaging material such as pre-crushed film flakes, PP raffia, PE/PP woven, PE foam, and many others with the addition of a force feeder on the feeding hopper.
The feeding speed is controlled and adjusted automatically for different types of material shapes and weights to ensure stable feeding and output production. When processing rigid regrind (granule), the force-feeding mechanism can be switched off.Machine Advantages
In the Repro-Direct, the material is fed into the hopper directly without the need for pre-heating before extrusion. When processing rigid regrind or compressed washed flakes (processed by a squeezer dryer), this system ensures a faster and easier machine starting and stopping process compared to other systems (for example, a machine with an integrated cutter compactor which requires pre-heating of the cutter compactor before machine start).
The rigid regrind (or film flakes) fed to the hopper feeder by a screw conveyor (or a belt feeder) are transported directly into the extruder without being pre-cut or compacted.
Flexible add-ons and Customization
- A screw conveyor or belt conveyor can be added to facilitate material feeding
- A large anti-bridging storage tank can be added to the feeding section for storing large-volume waste. The constantly turning rotors can prevent flakes from bridging inside the tank. (Positioned on top of the feeder screw, the anti-bridging silo provides a continuous supply of flakes with a precisely controlled feeding mechanism.)
- A crusher can be added for pre-crushing the material before entering the extruder.
- Unvented, single, or double degassing can be customized depending on material type and condition
- A vacuum degassing system and two-channel filter can be added to the machine
- Water ring die face cutting or strand die (spaghetti type) pelletizers are available depending on preference
- A metal detector can be added to the conveyor belt for additional protection
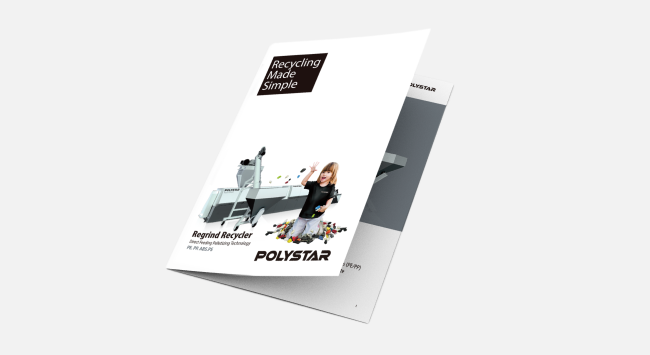
Repro-Direct Catalog
-
Hard Plastic Regrind
-
Washed Material
-
Fluffy Flakes
-
HDPE-milk-bottles
-
Film
-
Scrap