We use cookies and other tracking technologies to improve your browsing experience on our website, By clicking "Accept All," you agree to allow cookies to be placed to enhance your browsing experience on this website to show you personalized content and targeted ads, to analyze our website traffic, and to understand where our visitors are coming from. You can manage your cookie settings below. Clicking "Confirm" indicates your agreement to adopt the current settings.
Spain - POLYSTAR Demonstrates Live at Equiplast 2017
Source: CPRJ Editorial Team (JEN)
Date: 16/10/2017
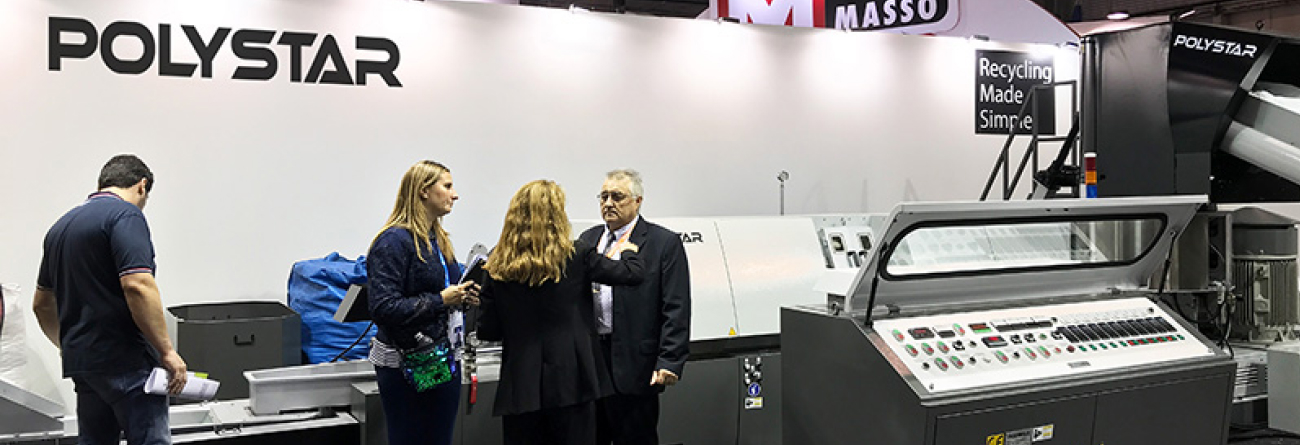
In this year's Equiplast which took place in Barcelona, Spain in October, POLYSTAR had demonstrated live its most popular selling recycling machine Repro-Flex 100.
The recycling line has a production capacity of 300-400kg per hour, designed especially for processing post-industrial polyethylene (PE) and polypropylene (PP) printed and non-printed film waste. The one-step recycling technology turns factory-generated film waste back into high quality recycled pellets, which can be used immediately for reprocessing in blown or cast film lines.
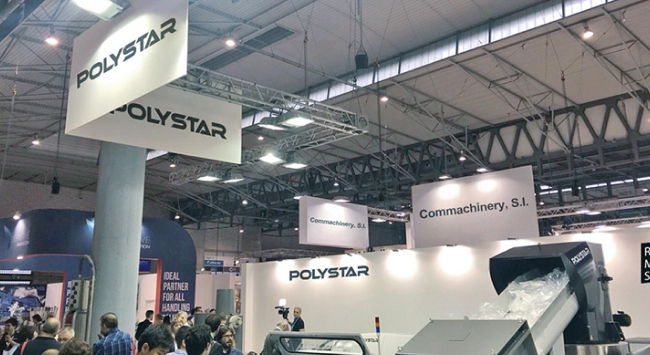
Machine's Advantages
POLYSTAR focuses particularly on easy-to-use technology which makes recycling simple for all plastic producers. It allows operators to rapidly change between different types of material when HDPE, LD/LLDPE and PP film of different sizes and thicknesses need to be processed on the same machine. The compact ECO machine design with cutting integration requires only one operator to run the complete line.
The pelletizing extruder has a double-degassing (double vented) design together with an effective vacuum pump system which is ideal for processing post-industrial waste material, as the machine can process both non-printed and printed waste with minimal material degradation.
Despite the fact that post-industrial film is generally clean and dry from in-house production, some moisture content can be generated during storage or transportation process. In the past a large number of film producers have been using unvented (extruder without degassing) recycling machines, which could affect pellets quality when there is humidity in the waste material.
When degassing is not done properly during the recycling process, the end product (film production) quality is compromised, resulting in "fish eye" on the surface of the film.
POLYSTAR's double degassing extruder design helps to solve this problem with effective degassing ability while making sure that the reusability of the transparent, non-printed pellets is at its highest level possible.