We use cookies and other tracking technologies to improve your browsing experience on our website, By clicking "Accept All," you agree to allow cookies to be placed to enhance your browsing experience on this website to show you personalized content and targeted ads, to analyze our website traffic, and to understand where our visitors are coming from. You can manage your cookie settings below. Clicking "Confirm" indicates your agreement to adopt the current settings.
Leading PE Stretch Film Producer in Taiwan Invests in POLYSTAR Recycling Machine
Source: CRPJ Editorial Team
Date: 25/07/2017
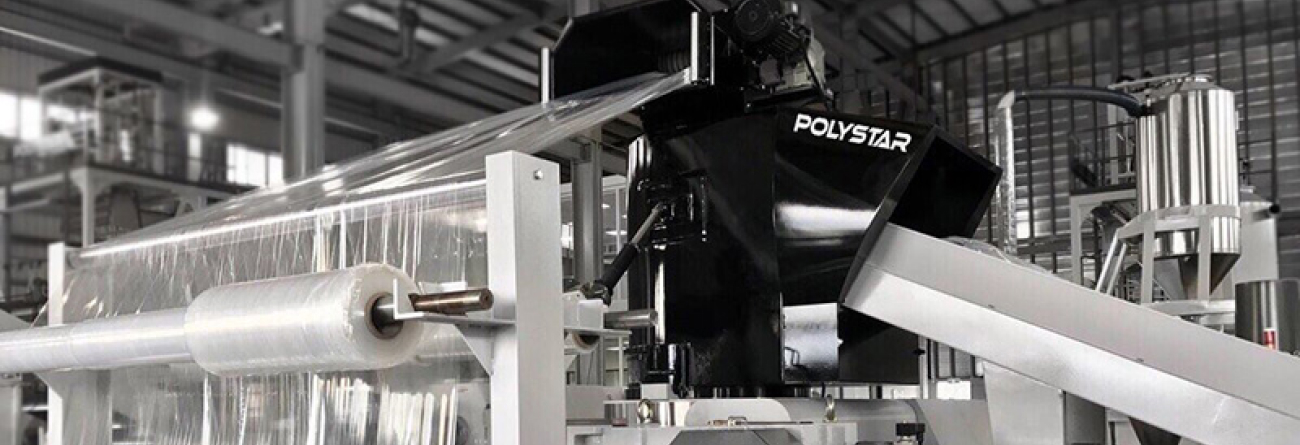
One of Taiwan's leading polyethylene (PE) stretch film producers has invested in POLYSTAR's recycling technology to process in-house waste generated from the extrusion lines.
The film supplier, with a monthly production capacity of 3,000 tons, is said to be the first Taiwanese company to bring in a five-layer casting extruder from Germany and is now equipped with several multi-layer cast film and printing machines from Europe.
In 2016, the film producer opted for the POLYSTAR recycling line to process its in-house waste generated from the extrusion lines. In fact, it was the first equipment that this company had ever purchased from an Asian manufacturer.
The POLYSTAR recycling machine is now running 24 hours a day and 7 days a week in the factory of the ISO 9002 certified film producer, with an average production of 250-300kg/h.
Feeding Process
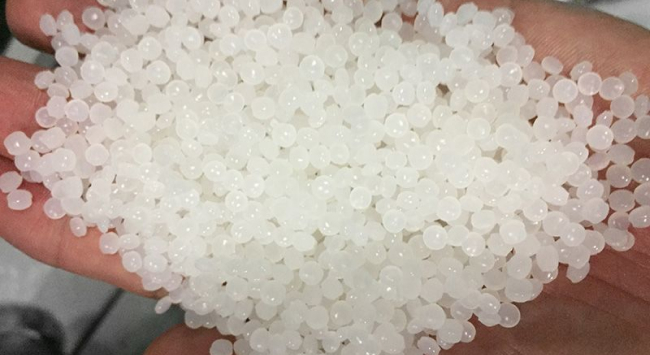
The defected film-on-rolls are fed automatically via the nip rolls on top of the cutter-compactor, which is then compacted and fed directly into the recycling extruder for further processing and pelletizing. The rest of the occasionally generated scraps are fed via the conveyor belt. The two-way feedings are controlled automatically and simultaneously to prevent over-feeding or insufficient feeding of material into the machine.
Despite the difference and variation in film width, thickness, and layer structure (mono, three, and five layers), the machine can handle all these film scraps of different compositions with consistency and produce high-quality and uniform-sized pellets, which are then put immediately back into the cast and stretch film lines.
"The built quality of the POLYSTAR recycling machine, as well as the product (recycled pellets) quality, meet our high standards," commented the Production Manager of the film manufacturer during a visit from POLYSTAR to check up on the user experience after several months of operating the machine. "The level of automation and intelligent control is up there and the operation is so simple."
The design of the POLYSTAR recycling machine is also very compact and takes up very little space. "This was important for us because we had space limitations and we needed a machine that could fit right next to our stretch film line," he added.