We use cookies and other tracking technologies to improve your browsing experience on our website, By clicking "Accept All," you agree to allow cookies to be placed to enhance your browsing experience on this website to show you personalized content and targeted ads, to analyze our website traffic, and to understand where our visitors are coming from. You can manage your cookie settings below. Clicking "Confirm" indicates your agreement to adopt the current settings.
In-house Recycling with POLYSTAR. Easier than Easy
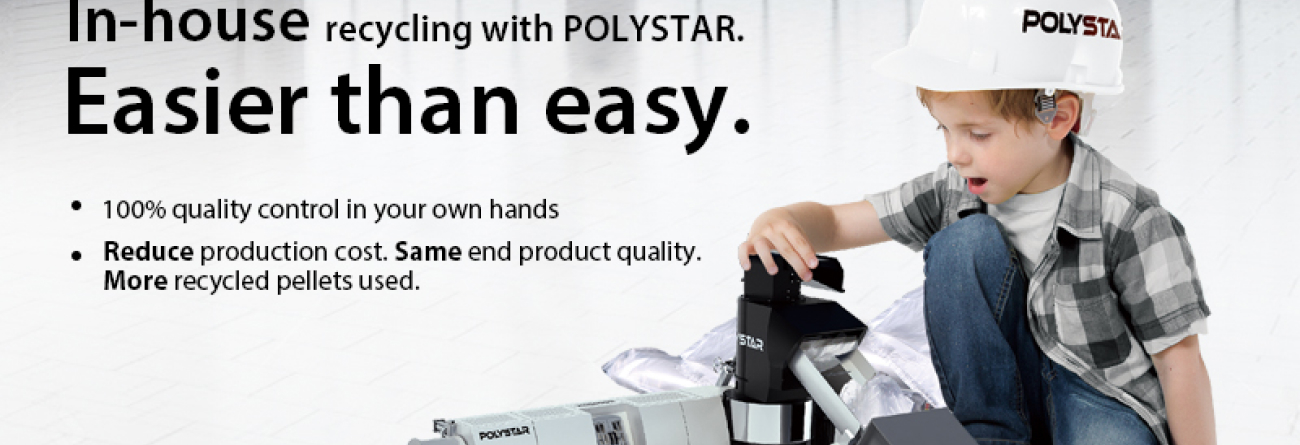
Why In-house Recycling Instead of Out-sourced Recycling?
Better Quality Control Changes Everything
In-house recycling makes sure that the material comes 100% from your own production and does not mixed together with material from other sources. Examples of the in-house scraps are HDPE/LDPE edge trim, cut/punch waste from bag making production, defective film-on-rolls, start-up film scraps, loose leftover film, HDPE, LDPE/LLDPE, stretch film, shrink film, BOPP and many others.Minimal material degradation, pellet quality (size), and consistency can also be achieved and controlled.
"Logistics, transportation, and storage costs can also be reduced
when all the waste is kept 100% in-house instead of out-sourcing it"
-
Maximum Possible Amount of Recycled Pellets
The consistency in quality (uniform in size and minimal property change) of the recycled pellets can ensure that the recycled material can be reused again in the extrusion machines to produce high-end film products with the highest possible quality. -
Fast ROI (Return on Investment) on the Machine Investment
The return on machine investment can be extremely fast, mainly because of the huge savings in raw material costs. When done properly, the quality and reusability of the recycled pellets can be much higher compared to out-sourcing. The extremely simple-to-use machine design requires only one operator at the feeding section of the recycling machine and requires minimal labor intervention.
What Level of Technology is Required for Efficient In-house Recycling?
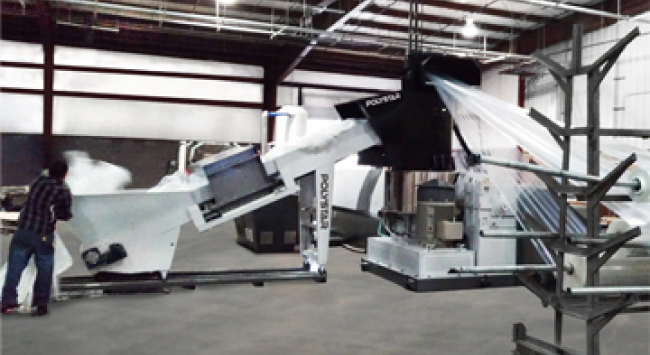
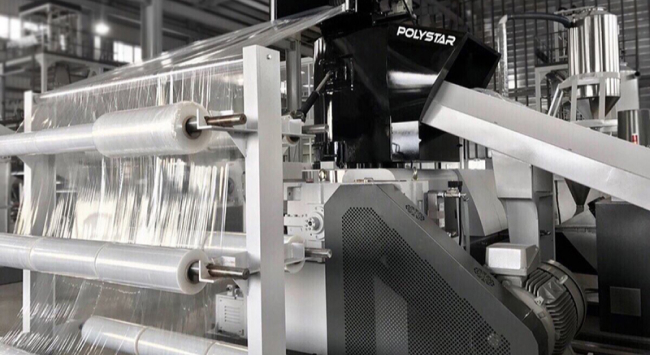
How Simple Are Our Maintenance and Operational Procedures?
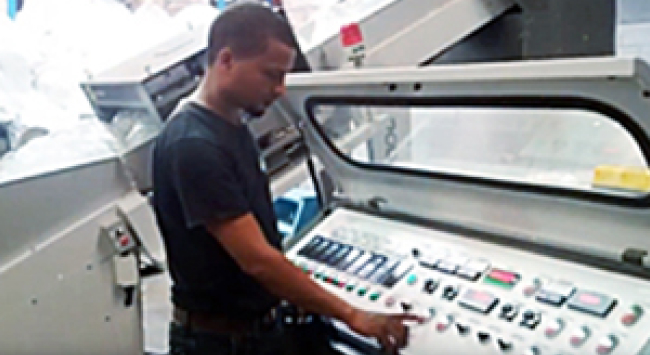
Simplicity throughout the entire machine design - From user interface, machine operation, and maintenance (both mechanical and electrical), to changing consumable spare parts. Even untrained operators can understand how to get the most out of our machines.
"A new operator can learn to work with the machine within a very short period of time"
"The machine is controlled from a simple, clearly displayed, compact control panel that is easy for the operators to understand and work on"
-
A Clean and Simple Process Becomes Part of Your Production
No bad smell. No loud noise.In-house recycling can be done beautifully with a compact and well-designed recycling machine without making your factory wet and dirty. -
Stable Production
Besides a strong and quality mechanical machine, our recycling machines are powered by world-class electrical components (SIEMENS, Fuji, Schneider, and Omron) to ensure operational stability. Electrical breakdown has been a common problem for some producers, and therefore we equip our machines with the best available components for a smooth, 24-hour operation.
__23K23jLqor.jpg)
POLYSTAR provides different recycling solutions (different in production capacity and different shredding and cutting integrated technologies) for packaging film (blown and cast), raffia, injection molded, woven/non-woven, pipe extrusion, and thermoforming. Depending on the user’s material type, industry, capacity requirement, and space limitation, POLYSTAR is able to offer a suitable recycling solution.