Para tu mejor experiencia, POLYSTAR utiliza cookies y otras tecnologías que personalizan contenido, analizan tráfico y revelan el origen de nuestros visitantes. Haz clic en "Aceptar todo" o gestiona tus preferencias a continuación. Confirmar implica aceptar la configuración actual. ¡Gracias!
7 Soluciones Clave para Enfrentar Problemas Comunes | Una Guía para una Producción Estable
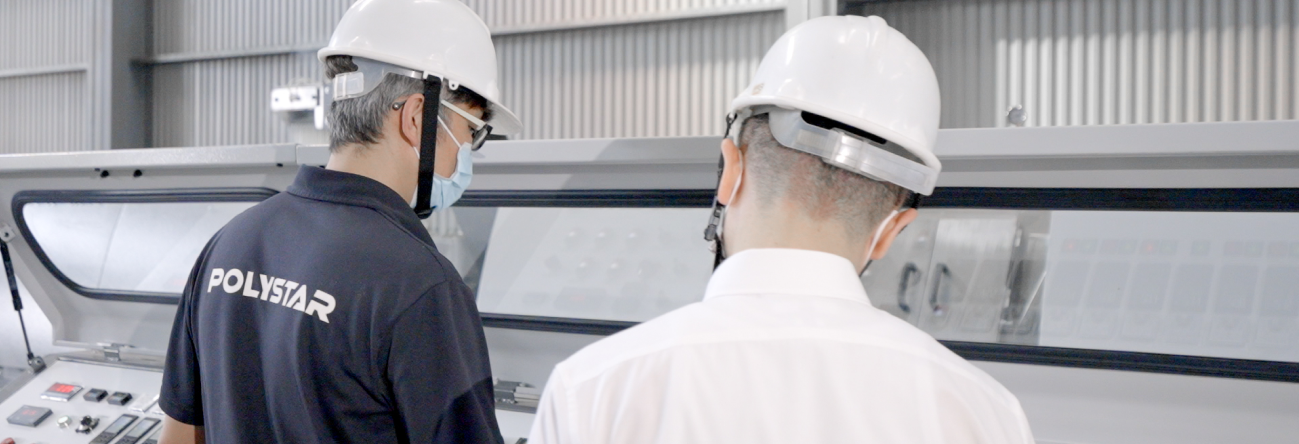
El reciclaje de plástico es un proceso de suma importancia para poder cuidar al medio ambiente de los residuos plásticos. Sin embargo, debido a que cada plástico cuenta con características diferentes, el proceso de reciclaje puede volverse más complejo en ciertas ocasiones. En la mayoría de los casos, los problemas más comunes pueden resolverse con el mínimo esfuerzo al tener una máquina de reciclaje de plásticos flexible fácil de usar y capaz de adaptarse a los cambios en la operación. En este blog hablaremos sobre las soluciones a los 7 problemas más comunes que los fabricantes y recicladores pueden encontrar en el proceso del reciclaje de plástico.
1. Inestabilidad en la alimentación del material
La alimentación de los residuos hacia la máquina de reciclaje debe de ser, en todo momento, estable para poder lograr la máxima productividad posible, previniendo al mismo tiempo la inactividad de la máquina. Si la cantidad de material es demasiado alta o demasiado baja, la producción puede no ser tan eficiente y óptima como debería de ser.
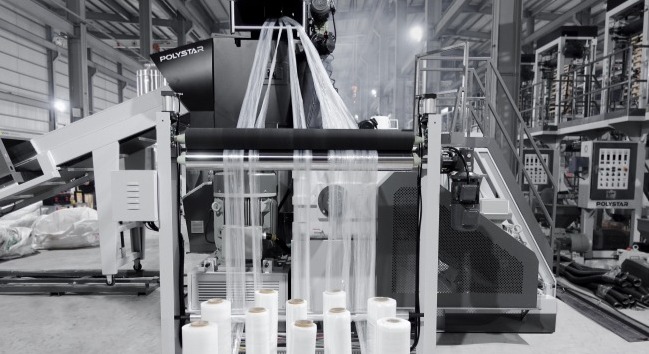
Solución:
2. Contaminación del material plástico
Los residuos de comida, suciedad, aceite, y la mezcla de diferentes tipos de plásticos puede contaminar los pellets reciclados, disminuyendo así su calidad y su reutilización. Esta contaminación tiene un impacto negativo en el proceso de reciclaje, haciéndolo menos eficientes al producir más residuos con un costo más elevado.
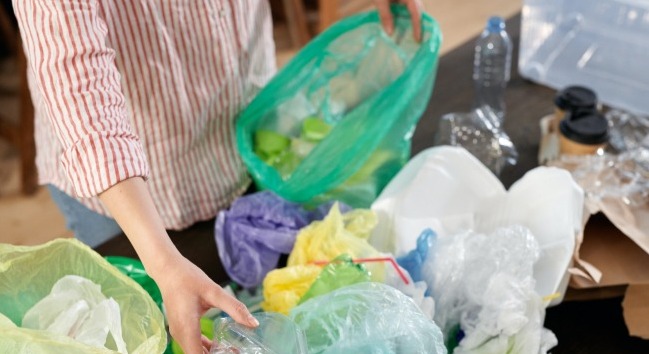
Solución:
La solución más sencilla es de asegurarse de que los residuos plásticos estén limpios y separados por su tipo antes de ser introducidos a la máquina de reciclaje. Los residuos post consumo deben de ser lavados y secados antes de comenzar con el proceso de reciclaje.
3. Obstrucciones en la tolva
Las obstrucciones en la tolva generalmente se debe a la preparación incorrecta de materiales o un mantenimiento incorrecto de los componentes de la máquina. En las máquinas de reciclaje con tolvas, los materiales pueden causar obstrucciones debido a la humedad o al pegarse entre ellos.
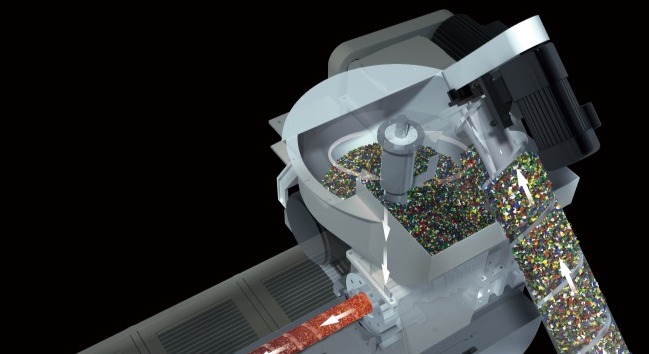
Solución:
Los residuos deben de ser correctamente preparados y separados según su tipo, tamaño y condición. Además, el uso de un sistema automático de alimentación puede solucionar muchos problemas de obstrucciones. Darle un mantenimiento regular a los componentes de la máquina, cambiarle las mallas de los filtros y limpiando el cabezal son acciones que pueden prevenir dicho problema. El uso de un alimentador de fuerza en la tolva también puede prevenir obstrucciones.
4. Sobrecalentamiento
El sobrecalentamiento de los residuos de plástico en la unidad de “preacondicionamiento” (unidad donde se encuentran partes como el cortador compactador o el triturador) o el fundido excesivo de materiales plásticos pueden provocar a menudo la degradación de los pellets reciclados, debilitando la calidad de los productos plásticos finales.
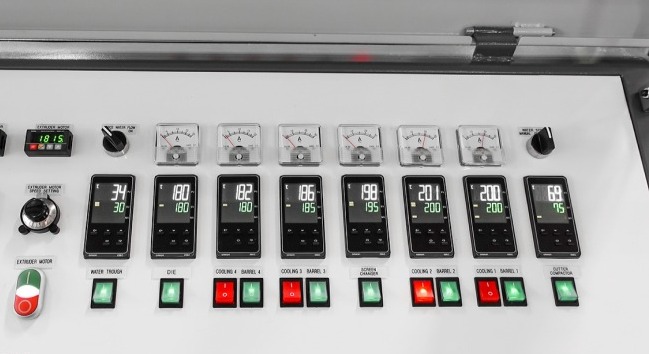
Solución:
Es muy importante establecer la temperatura adecuada en cada sección de la máquina de reciclaje según los materiales que serán reciclados. Calibrar el calentamiento y el enfriamiento de los materiales y usar componentes fiables que no causen ningún tipo de desiquilibrio de temperatura que pueda resultar en problemas de sobrecalentamiento también son dos factores muy importantes de tener en cuenta. De la misma manera, al prevenir las obstrucciones, se reducen las probabilidades de tener problemas de sobrecalentamiento.
5. Pellets plásticos pegajosos
Los pellets reciclados a menudo se pegan entre sí debido a varias razones, como por ejemplo temperaturas excesivamente altas en el extrusor, problemas en el proceso de enfriamiento de los pellets o las propiedades de ciertos materiales.
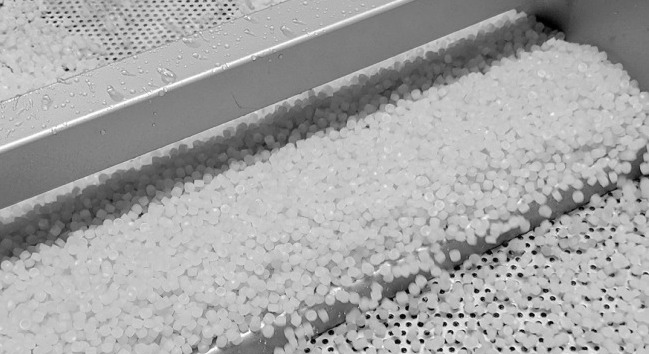
Solución:
Al igual que las soluciones que recomendamos anteriormente para el sobrecalentamiento, para evitar este problema es escencial establecer los parámetros correctos en la extrusora según el material que se esté reciclando. También es importante garantizar que la temperatura del agua de enfriamiento (o en ciertas ocasiones, la temperatura del aire para las máquinas enfriadas por aire) esté controlada. Además, el uso de una centrífuga de secado puede secar los pellets de una manera más efectiva, previniendo que ellos se peguen entre sí. En lugares con climas cálidos, el uso de un enfriador, o “chiller”, también puede resultar ser útil para mantener una producción adecuada.
6. Pellets plásticos huecos
Este tipo de pellets no son muy útiles para la producción de plásticos. Es común que ellos causen que la producción sea ineficiente y que la calidad de los productos finales sea muy baja debido a su baja densidad, resistencia, y tamaño y formas inconsistentes. Las razones más comunes por la que esto sucede incluye una desgacificación o plastificación deficiente e inestabilidad en la temperatura y en la velocidad de la circulación de agua de enfriamiento.
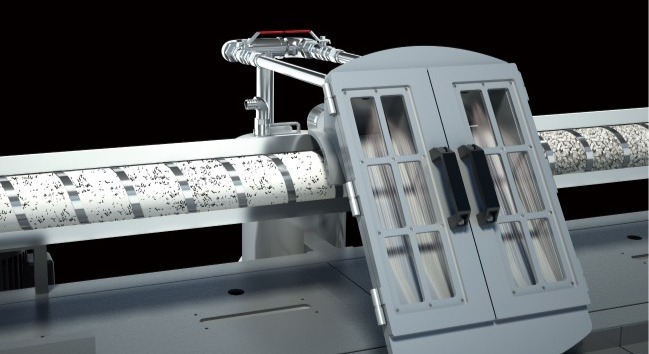
Solución:
El sistema de desgasificación al vacío es una solución eficiente para eliminar el gas y la humedad que suelen causar los pellets huecos. Asegurar temperaturas adecuadas y estables en cada zona de la máquina de reciclaje y en el cabezal es fundamental para lograr una plastificación (o peletización) correcta. Además, ajustar la temperatura y velocidad del agua de enfriamiento evita la producción de estos pellets.
7. Pellets uniformes o pelotas de pellets
La calidad de los pellets reciclados puede notarse en su uniformidad y tamaño. La alimentación inestable, el flujo del material y un sistema de peletización deficiente pueden ser las razones más comunes por las que los pellets resulten siendo de diferentes tamaños o formas. Esta última también es la razón mas común de la producción de trozos o pelotas de plástico en lugar de pellets uniformes.
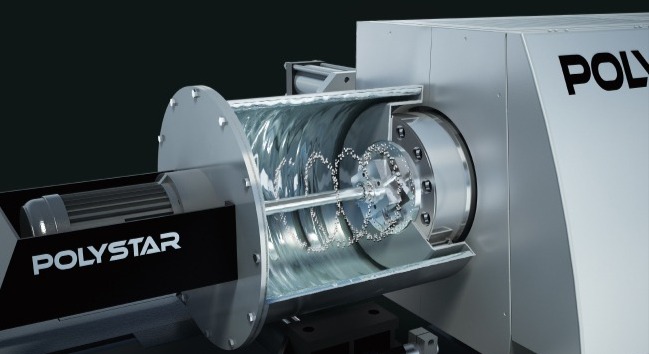
Solución:
Este problema puede ser evitado al estabilizar la alimentación del material, de modo que el flujo del material fundido sea constante, previniendo cualquier obstrucción dentro de la máquina. El uso de un sistema de corte de pellets controlado por velocidad y presión automática también puede ser de gran ayuda. Si tomamos como ejemplo la peletizadora con anillo de agua de POLYSTAR, podremos observar como ésta ajusta automáticamente la velocidad del corte del material fundido saliendo del cabezal, asegurando al mismo tiempo que las cuchillas peletizadoras estén siempre posicionadas en el cabezal y trabajando en sincronía con la presión del cabezal.
Esto da como resultado el corte de pellets de tamaños y formas uniformes. Si las cuchillas peletizadoras están desafiladas, peletizarán trozos o pelotas de pellets. Por eso, es necesario siempre reemplazarlas con los repuestos originales y mantenerlas siempre en la posición correcta.
¿Cómo escoger una máquina de reciclaje estable?
Al invertir en máquinas de reciclaje de plástico, los recicladores y los productores deben de considerar una máquina en base a su rendimiento y su facilidad de uso y de mantenimiento. Una máquina estable debe de trabajar en harmonía en todas sus partes con todos sus componentes. Además, un servicio posventa de atención al cliente que le ayude a resolver sus problemas o buscar los repuestos que necesita es un beneficio que los clientes necesitan a largo plazo.
POLYSTAR se enorgullece de ofrecerle una máquina que cumplen con estos criterios, ya que nuestras máquinas utilizan componentes universales de calidad mundial, y son mejoradas constantementes por medio de la reingeniería. Esto garantiza un rendimiento estable junto con una producción de pellets de alta calidad, solución que contribuye a lograr obtener el retorno sobre la inversión de la máquina.
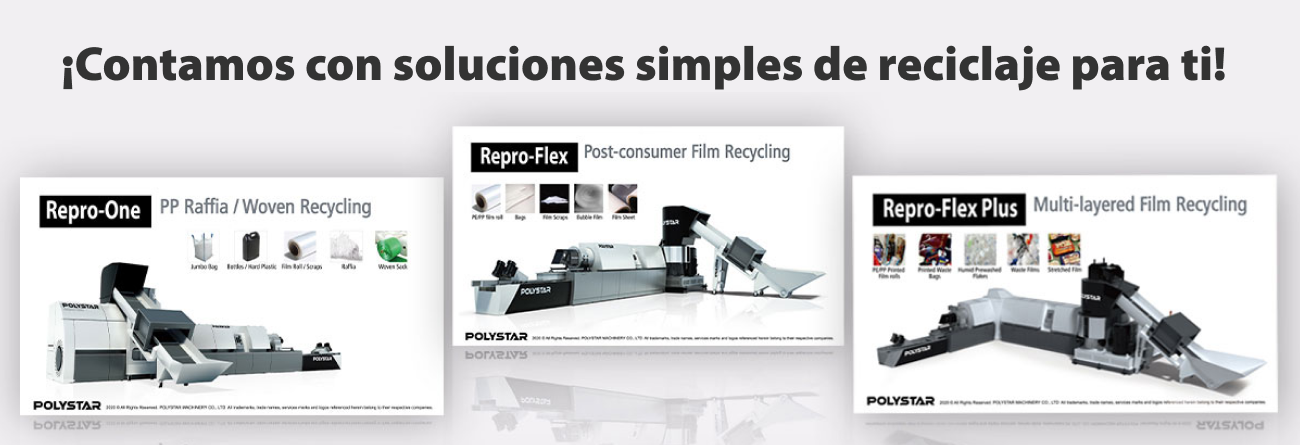
Descubre más
Sobre el Autor
Resul Gökpınar
Resul crea contenido basado en su experiencia obtenida, brinda soluciones a los clientes en el mercado de Truquía y EMEA.