We use cookies and other tracking technologies to improve your browsing experience on our website, By clicking "Accept All," you agree to allow cookies to be placed to enhance your browsing experience on this website to show you personalized content and targeted ads, to analyze our website traffic, and to understand where our visitors are coming from. You can manage your cookie settings below. Clicking "Confirm" indicates your agreement to adopt the current settings.
What is rPET Plastic? How can Producers Take Advantage of It?
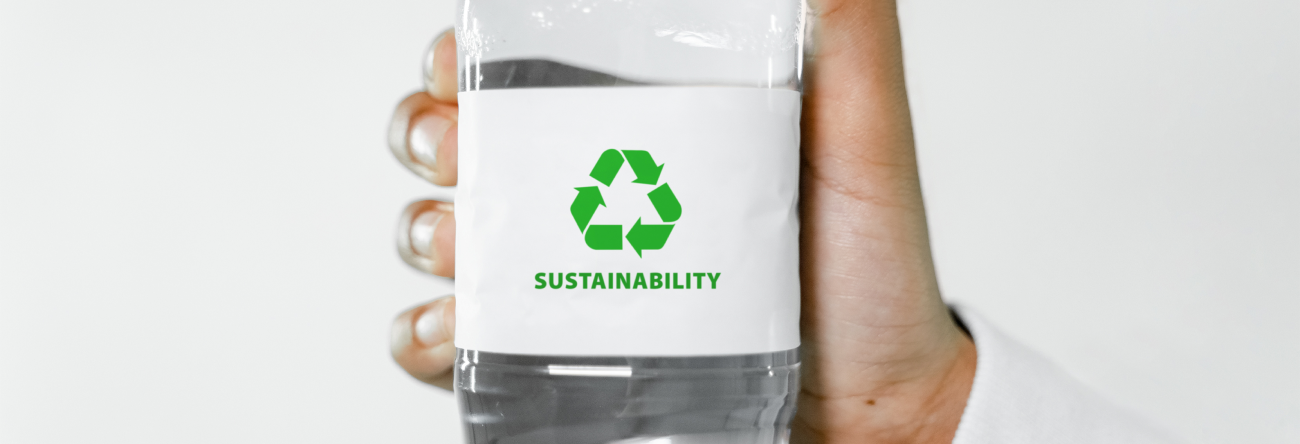
PET plastic is extremely popular with the modern society, resulting in the high demand for PET products. However, this high consumption also creates a need for more comprehensive waste management to mitigate environmental impacts.
Recycled PET, or rPET, is gaining popularity as an alternative. In this article, we will introduce you to rPET and explain why plastic producers should consider incorporating it into their production processes to benefit both the environment and their bottom line.
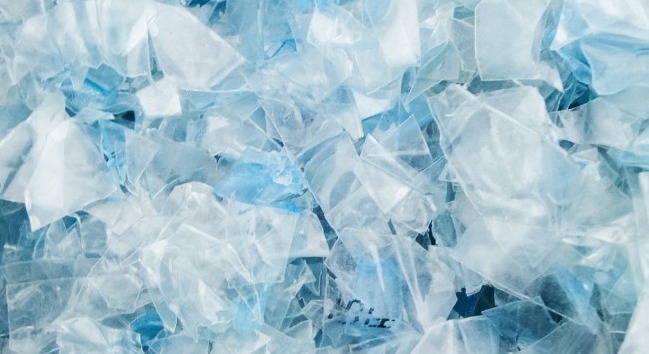
PET vs. rPET.
PET, also known as number one plastic, is a highly prevalent thermoset polymer due to its strength, lightweight, and resistance to gas and moisture. Due to its desirable properties, PET is widely used in food and beverage containers, packaging materials, textiles, and automotive components.
rPET, on the other hand, refers to recycled PET. When PET plastic waste is collected, reprocessed, and made into new items, it is referred to as rPET. The same terminology applies to other types of recycled plastics such as rPP, rPE, or rPS.
rPET not only benefits the environment, but also your brand.
PET is primarily sourced from non-renewable resources, whereas rPET is produced using post-industrial or post-consumer plastic waste that would otherwise end up in landfills. Additionally, rPET requires less energy to produce than virgin PET, resulting in reduced greenhouse gas emissions and a smaller carbon footprint.
Aside from environmental benefits, rPET also offers economic and social advantages. Incorporating recycled PET into production can significantly lower material costs, as recycled plastic is often less expensive than virgin plastic. From a social perspective, companies can demonstrate their commitment to sustainability and environmental stewardship, which can enhance their brand reputation and appeal to environmentally-conscious consumers.
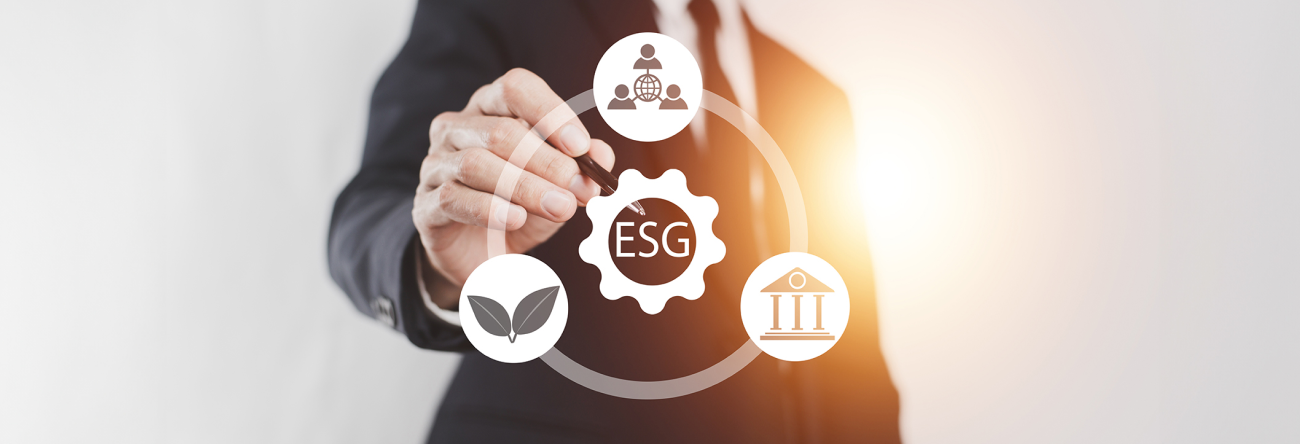
How to obtain rPET and apply it to the products?
To produce rPET, PET waste must be collected, sorted, washed, dried, and crushed. Afterward, these PET flakes will go through extrusion and pelletization processes to transform into pellets.
Companies can use rPET pellets in various production processes, such as blow molding, injection molding, film extrusion, fiber production, and 3D printing. rPET pellets can be used either on their own or blended with virgin PET, depending on the specific requirements of the product.
Work with rPET plastic for diverse product properties
Producers sometimes blend two different types of plastics to manufacture products. By doing so, the final products acquire the properties of both plastics and achieve a better mechanical result, such as increased strength, distinct colors or textures, and so on.
Moreover, combining plastics facilitates recycling. Producers can incorporate recycled materials into new products, promoting sustainability and reducing the environmental impact. Here are the recycling cases of mixed plastics and the recycled pellets are later reused in the production.
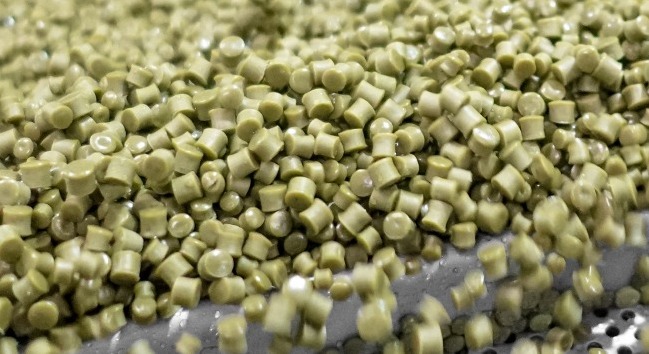
PET + PP printed laminated film recycling
The general characteristics of mixed PET and PP:
- higher impact strength
- heat resistance
- transparency (The results are influenced by the ratio of the two plastics)
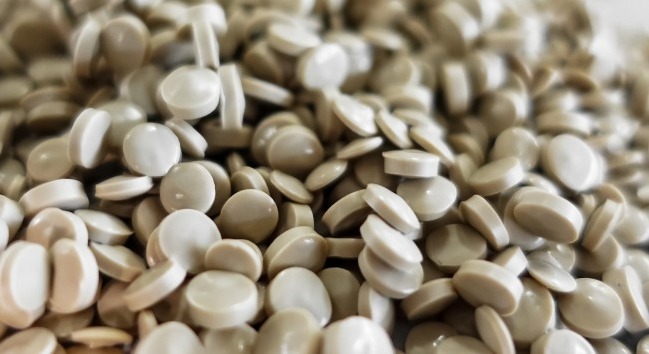
PE + PET woven recycling
The general characteristics of mixed PET and PE:
- higher impact strength
- cost-effectiveness
- processability (The results are influenced by the ratio of the two plastics)
Conclusion
About the Author
Janine Cheng
Marketing AssistantJanine creates engaging content for POLYSTAR’s social media presence, including keeping social media channels updated and brand-focused and seeking ways of connecting with plastic producers and recyclers.