We use cookies and other tracking technologies to improve your browsing experience on our website, By clicking "Accept All," you agree to allow cookies to be placed to enhance your browsing experience on this website to show you personalized content and targeted ads, to analyze our website traffic, and to understand where our visitors are coming from. You can manage your cookie settings below. Clicking "Confirm" indicates your agreement to adopt the current settings.
What is PET Plastic? PET Recycling Machine Selection Guide
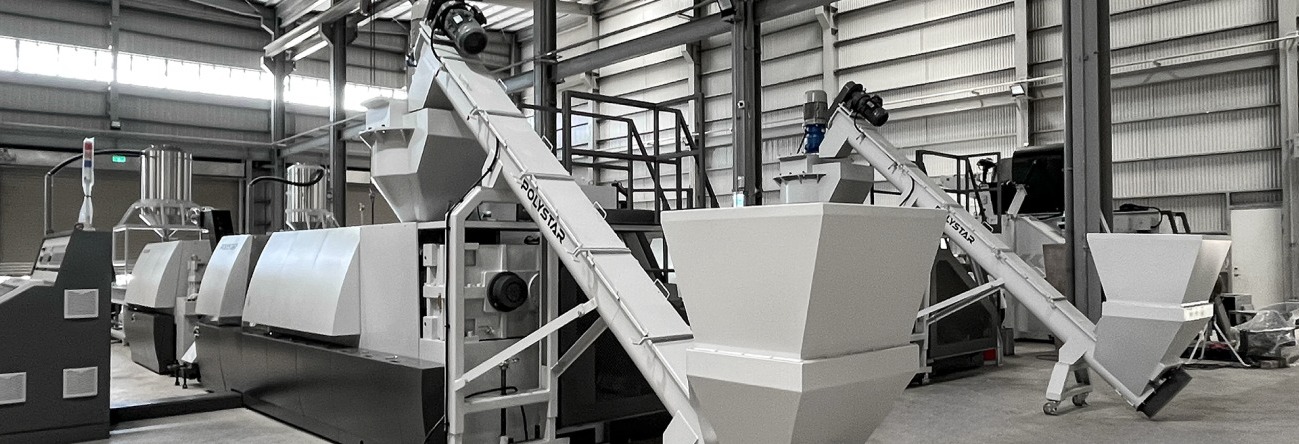
Introduction
PET (Polyethylene terephthalate) is a thermoplastic polymer used in the production of plastic bottles and films. Compared with other plastics, it has good strength, light weight, thermal stability. PET plastic is a thermoplastic polymer commonly used for high-quality packaging applications. It is used for bottles and containers, clothing and footwear, medical devices, food packaging. It also has many other industrial uses.
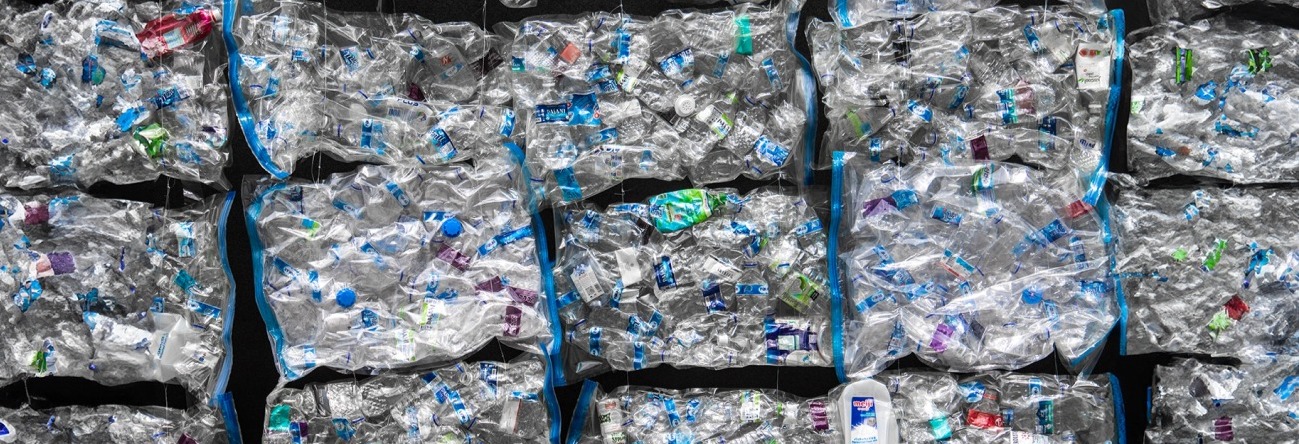
PET is completely recyclable, and it is the most recycled plastic worldwide, and PET bottle recycling trend is expected to increase over the next decade. The demand for recycled PET bottles is increasing due to the growing trend of using water bottles and other plastic containers as a replacement for glass. This trend has been driven by government legislation, non-governmental organizations (NGOs), and retailers.
In this article, I will explain how to recycle PET bottles, and which machine is the most suitable one for recycling PET materials.
6 steps to recycle PET bottles
Step 1: Sorting process
This is the first step of the whole process. Humans and machines collaborate to sort and remove anything that is not recyclable. Following that, the bottles will be sorted by plastic type and color.
Step 2: Crushing process
After sorting, a crusher crushes the plastic bottles into flakes. This makes the plastic easier to clean.
Step 3: Washing process
PET bottles flakes are sent to the washing machine where they are cleaned and separated from other waste materials.
Step 4: Drying process
This step removes humidity from waste plastics by blowing hot air at high pressure, making them dry quickly.
Step 5: Separation process
The separation process involves using a magnet or sieve to separate different materials from PET plastics. After this stage, the material is ready for pelletizing.
Step 6: Pelletizing process
This is the final stage in the process of producing output pellets from PET bottle waste. With a reliable pelletizing machine, you can produce high-quality pellets with uniform shapes.
PET plastic recycling machine selection guide
PET has a high fluidity, the best way to recycle PET bottles is to use a strand pelletizing system. Here is the process of the strand-type pelletizing machine: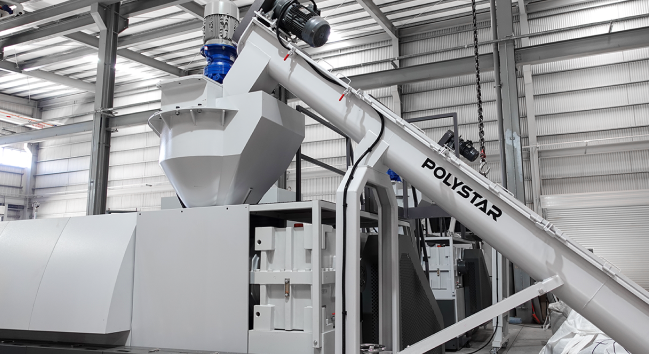
1. Feeding process
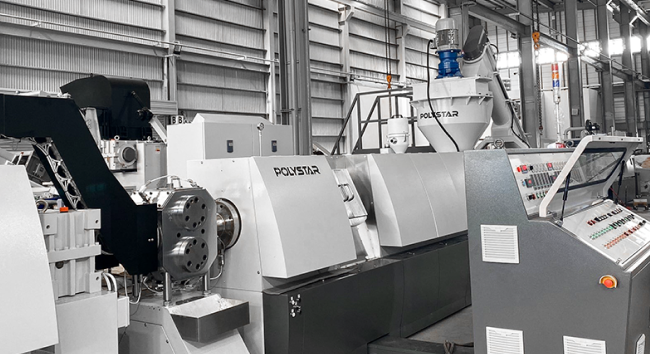
2. Extrusion process
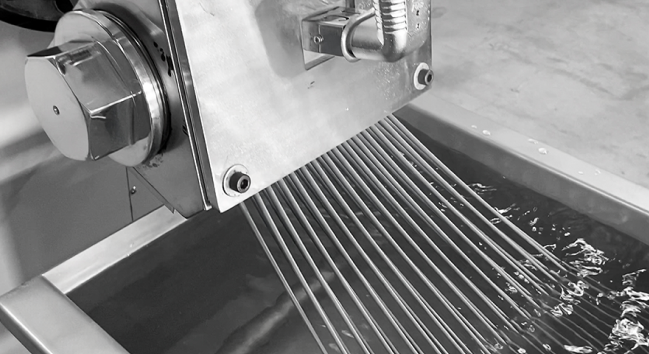
3. Stranding process
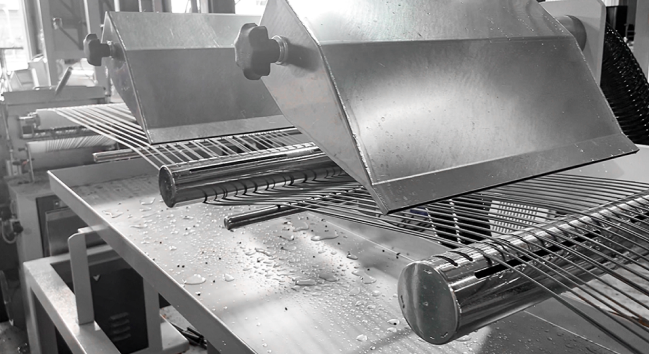
4. Dewatering process
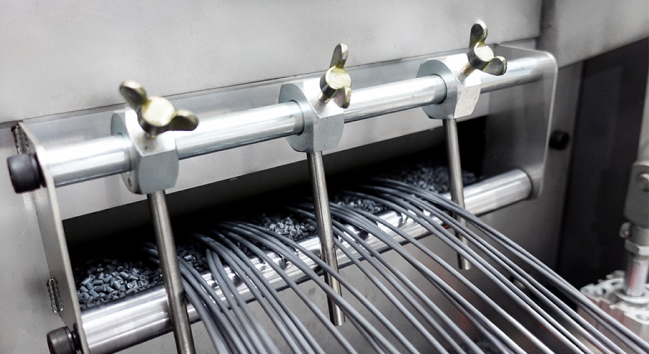
5. Pelletizing process
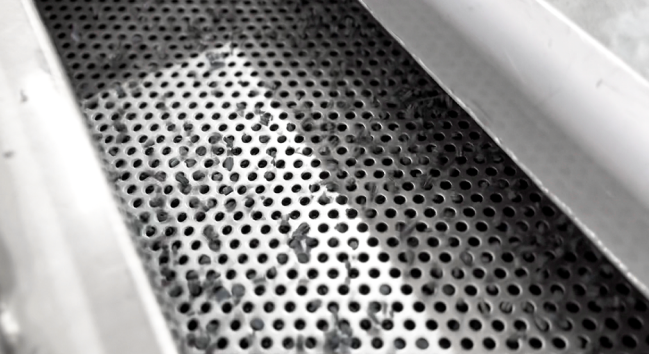
6. Sieving process
Before being transported to the silo tank, the pellets are sieved to make sure they are all the same size.Conclusion
In fact, PET plastic is so widely used because it can be easily recycled into new products. Over 30 million tons of PET plastic are produced each year, but only about 20% of this is recycled. This means there's still a huge opportunity for businesses to get involved with PET recycling and help keep those numbers up.
POLYSTAR offers a reliable strand-type pelletizing machine with a simple design for you to start your PET recycling business. Feel free to contact us for more information.
Learn More
About the Author
Derek Shiao
Derek Shiao is a business development manager at POLYSTAR. He keeps up with the latest trend in the plastic industry and creates content based on his experience offering various solutions to customers.