We use cookies and other tracking technologies to improve your browsing experience on our website, By clicking "Accept All," you agree to allow cookies to be placed to enhance your browsing experience on this website to show you personalized content and targeted ads, to analyze our website traffic, and to understand where our visitors are coming from. You can manage your cookie settings below. Clicking "Confirm" indicates your agreement to adopt the current settings.
Types of Plastic Mechanical Recycling: Mechanical Recycling Technologies Explained
Mechanical recycling, one of the main types of plastic recycling, refers to the process of recovering plastic materials through sorting, shredding, washing, drying, and pelletizing. Depending on the type of plastic waste to be recycled and its condition, this process can be adjusted and even shortened, helping streamline recycling operations.
The type of recycling that will be used for your materials will vary depending on where the materials come from, what shape they are in, their humidity or ink content, and other specific properties of each plastic type (such as the melt flow index).
1. Material Source
The source of the material, which influences the types of plastic recycling methods used, refers to the origin of the plastic waste to be recycled. The type of mechanical recycling equipment to be used will vary depending on where the plastic was collected from (post-consumer or postindustrial sources) and its condition.
Post-industrial waste
Post-industrial waste comes from factories and is generally clean and dry, requiring a simpler recycling process, often skipping the washing and drying steps, and sometimes the pre-shredding step. The options for recycling this type of waste will be more flexible and will vary depending on the material’s shape, ink content, and general properties.
Post-consumer waste
Post-consumer waste comes from materials that have reached the end of their life cycle. These are often collected from dumpsters, curbside pickup programs, or landfills. Given that the previous washing and drying steps required usually leave the materials with a small percentage of humidity, additional degassing steps like the ones the Two-Stage Recycling Machine has are mostly recommended.
2. Shape of the Materials
The type of mechanism to feed materials to the extruder screw, which is an important consideration in different types of plastic recycling, will vary depending on the shape that the materials to be recycled have before entering the pelletizing machine. Recycling machines can be equipped with the following units depending on the shape of the material to be processed:
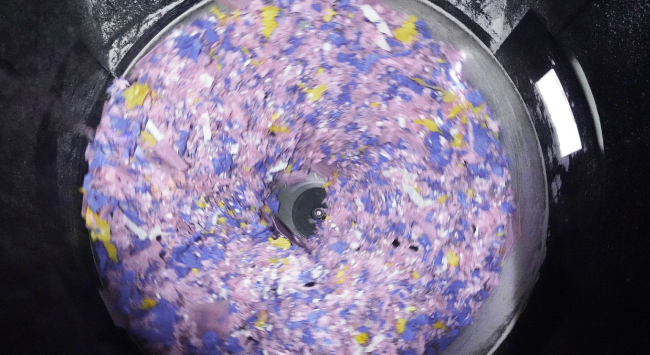
Cutter-compactor
The Plastic Recycling Machines that integrate a cutter-compactor are especially recommended for processing materials such as films on roll, film/bag scraps, fluffy film flakes, irrigation pipes, PE foam, etc. These machines are ideal for processing these materials, as they smoothen the recycling process by ensuring delicate and efficient processing of the materials thanks to the material agglomeration in the cutter-compactor.
This type of machine also works well for post-consumer materials that have previously gone through washing and drying lines since there is usually some humidity left after these steps, and the cutter-compactor helps evaporate some of that remaining moisture for smoother processing. Additionally, since post-consumer materials have already been shredded, the cutter-compactor helps feed materials such as fluffy flakes to the extruder more efficiently by preconditioning them.
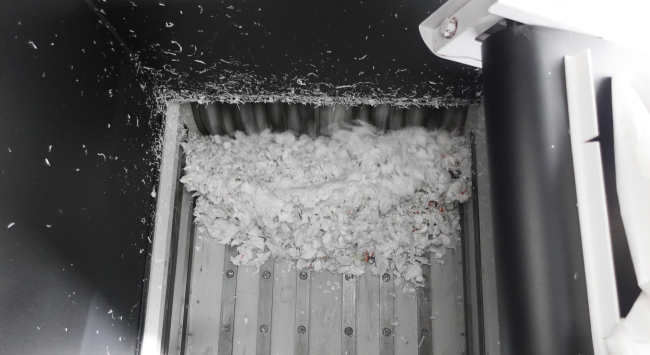
Shredder
Shredder Integrated Plastic Recycling Machines are recommended for materials such as raffia, woven/non-woven bags, sacks, and hard plastics (from post-industrial sources, that haven’t gone through crushing/ cutting steps). Having a shredder integrated into the pelletizing machine helps process materials in a single step by avoiding the need to use a separate crusher in postindustrial recycling.

Direct feeding
Machines with direct feeding to the extruder screw, such as the Mini Type Recycling Machine or the Hopper Feeding Recycling Machines, allow direct feeding of films-on-roll, bag precuts, or hard plastic regrinds without any preconditioning or precutting/ shredding unit. A force feeder can be added to these machines to optimize the feeding. Direct feeding machines are usually recommended for simple post-industrial materials that can be fed in a stipulated size (10mm x 10mm for hard plastics regrind) or for clean and dry PE films.
3. Material Degassing
Various types of recycling machines can have either a single stage or two stages (or screws) depending on the humidity percentage or amount of print on the materials to be processed.
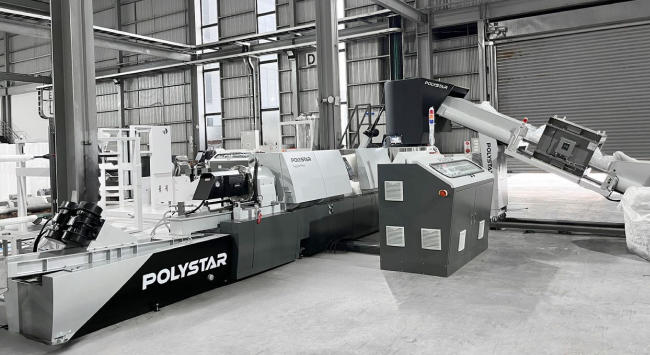
One stage Recycling Machine
Single-stage Plastic Film Recycling Machines are recommended for clean and dry postindustrial materials with no more than 3% humidity and 60% printed surface.
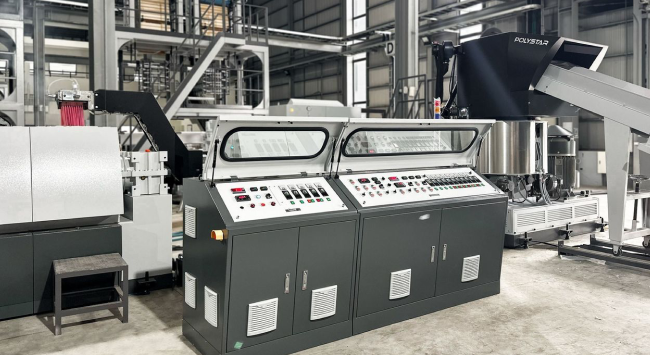
Two stages Recycling Machine
Two- Stage Recycling Machines have two consecutive screws and are also known as mother-baby extruders. They are recommended for post-consumer materials (that have previously gone through washing and drying lines) that have no more than 5% humidity, as well as post-industrial materials that have more than 60% printed surface. The second stage is recommended to incorporate additional degassing and filtering stations to decrease remaining impurities or humidity in the materials from ink or washing lines.
4. Pelletizing type
Pelletizing refers to the process of reshaping plastic materials into pellets by using a die face at the end of an extruder screw. Recycling machines can be equipped with two different types of pelletizing types: hot die face or strand type pelletizing, depending on the materials to be processed.
-
Hot die face pelletizing
This pelletizing method produces circular and flat pellets. They are formed as the plastic melt is pushed out through holes on the pelletizing plate while a knife rotates to cut the material into pellets. Hot die face pelletizing can incorporate a water ring for efficient and instant cooling of the pellets; and in some machines, it can use air-cooling to avoid contamination from water or to allow recycling plastic even in areas that have limited access to water.
-
Strand type
This pelletizing method produces tube-like pellets. They are formed from strands (also called “noodles” or “spaghetti”) of plastic melt coming out from a die head. The strands get pulled and go into a water tank in order to cool the material and blowers remove the water and then get cut into pellet-sized pieces. This pelletizing method is often used for materials with a high melt flow index (MFI) such as PET and some types of PP materials.
POLYSTAR’s Machines and Type of Mechanical Recycling
Recycling Machine Model |
Source
|
Feeding to Screw
|
Stages
|
Pelletizing Type
|
Cutter compactor integrated |
Post-industrial Post-consumer |
Cutter-compactor |
Single-Stage (One screw) |
Hot die face or Strand type |
Shredder Integrated |
Postindustrial |
Shredder |
Single-Stage (One screw) |
|
Two-stage |
Post-consumer Post-industrial |
Cutter-compactor |
Two-Stage (Mother-baby screws) |
|
Hopper feeding | Post-industrial | Direct feeding |
Single-Stage (One screw) |
|
Air-cooled | Post-industrial | Direct feeding |
Single-Stage (One screw) |
Hot die face |
The specific types of plastic recycling, particularly mechanical recycling, employed to process different materials will depend on the source, shape, humidity content, amount of printing on the surface, and melt flow index of the materials to be recycled.
You can refer to our blog posts to learn more information. Feel free to contact us to learn more details about the machine needed to recycle your plastic material.
About the Author
Renee Castro
Renee is helping plastic producers find simple solutions to their problems. She is interested in topics like the circular economy and the latest recycling trends.