We use cookies and other tracking technologies to improve your browsing experience on our website, By clicking "Accept All," you agree to allow cookies to be placed to enhance your browsing experience on this website to show you personalized content and targeted ads, to analyze our website traffic, and to understand where our visitors are coming from. You can manage your cookie settings below. Clicking "Confirm" indicates your agreement to adopt the current settings.
What are the Differences between a Cutter-compactor and a Shredder?
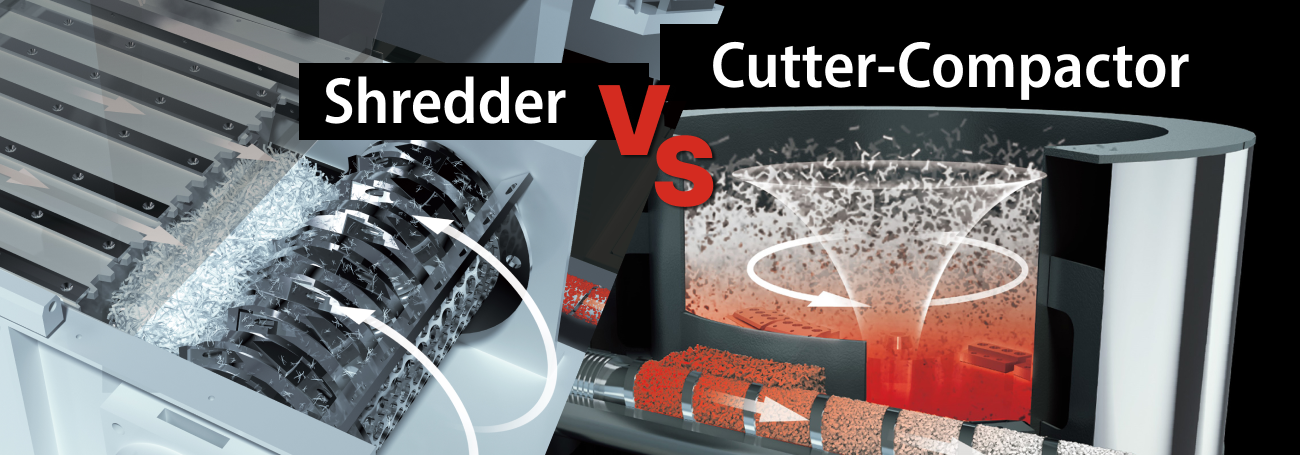
Cutter-Compactor
The cutter compactor as it is called cuts and compacts the plastic material before extrusion. This has two different types of blades:
- Stationary: the stationary (fixed) blades are attached to the bottom of the compactor and can be changed from the outside.
- Rotary: the rotary blades work like a blender.
These types of blades cut the material gently and cleanly. Having them to help the process to cut the waste in less time to increase the end production, giving effective and optimal outcomes.
In this cutter-compactor, the blades rotate constantly, mixing and cutting the plastic waste (post-industrial or post-consumer). In this way, the mixed waste will be easy to process in the extruder.
Shredder
A shredder is a piece of heavy-duty equipment designed to shred dense and light materials to prepare them for recycling. The shredder has a hydraulic plate that continuously pushes the bulky material toward the rotating shredder (rotor). Thanks to the blades that have rotating power and speed, cut and crush the plastic material into small pieces. The shredder reduces the size of the plastic waste with minimal degradation. After that, the plastic waste passes directly to the extrusion.
Different solutions POLYSTAR
With cutter-compactor: Repro-Flex and Repro-FlexPlus
Repro-Flex and Repro-FlexPlus are designed for the reprocessing of PE polyethylene (HDPE, LDPE, LLDPE) and PP polypropylene flexible packaging material, printed and non-printed. This cutter integrated pelletizing system eliminates the need to pre-cut the material, and requires less space and energy consumption while producing high-quality plastic pellets at a productive rate.
These machines combine cutting, extrusion, and pelletizing into one compact and efficient recycling line. The cutter compactor of the recycling machine prepares (pre-conditions) the material into an ideal condition for the extrusion process and feeds the material directly into the extruder with a centrifugal force. Compared to the conventional recycling machines, this integrated system does not require a separate crusher, therefore eliminating the problem of inconsistent feeding.
To know more about these two models:
With integrated shredder: Repro-One
Repro-One has an integration of a heavy-duty single-shaft shredder that is directly connected with the extruder and pelletizing system. It is ideal for PP raffia/PP non-woven manufacturer who process their rejected raffia waste (tapes, fabric, jumbo big bags, lumps) generated from in-house production. The recycled pellets can be put directly back into tape extrusion lines for immediate reprocessing. These recycled pellets can be loaded in high percentages and still produce excellent fabric with good tensile strength and elongation.
This eliminates the need of pre-cutting/pre-shredding large-sized, thick or bulky waste (including hard plastics), feeding the waste directly from the shredder into the extruder at a very fast and constant rate without overheating the material. This technology ensures continuous and uniform feeding to the extruder that produces high-quality recycled pellets.
About the Author
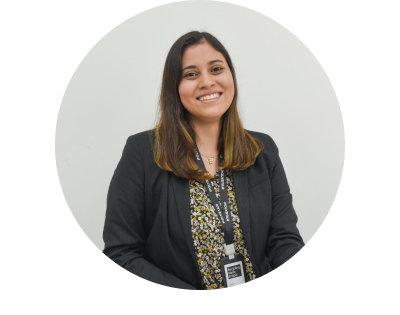
Maria Lopez
Marketing ManagerMaria Lopez is a content marketer at POLYSTAR. She authors in-depth guides that provide solutions to Plastic Producers. Not only to select your machine but also to keep you updated with the new trends.