We use cookies and other tracking technologies to improve your browsing experience on our website, By clicking "Accept All," you agree to allow cookies to be placed to enhance your browsing experience on this website to show you personalized content and targeted ads, to analyze our website traffic, and to understand where our visitors are coming from. You can manage your cookie settings below. Clicking "Confirm" indicates your agreement to adopt the current settings.
Two Types of Plastic Extrusion Process -Recycling and Film Blowing
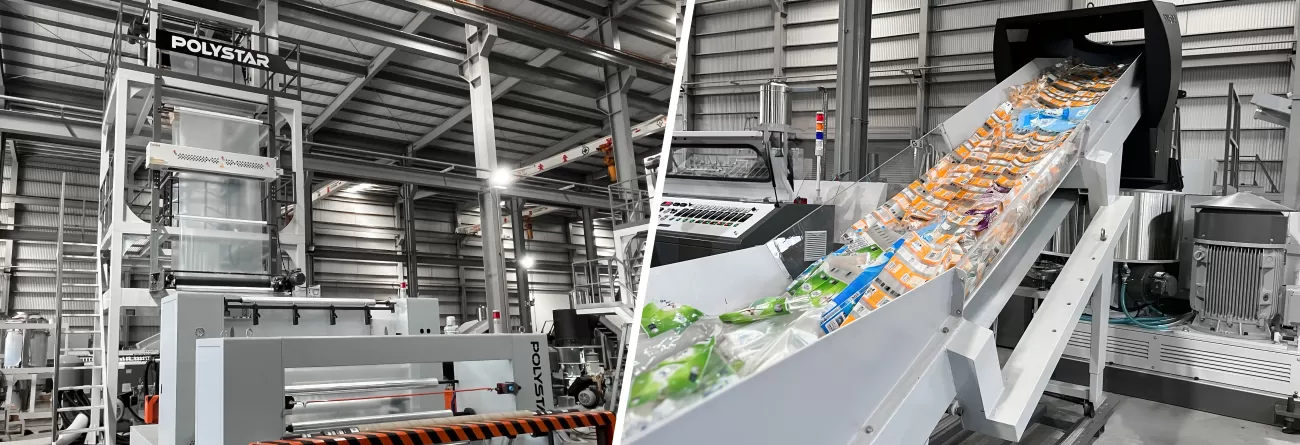
Have you ever wondered how everyday-use plastic film is made by the blown film machine? How can plastic waste in different shapes be reformed like uniform pellets? In this blog, we are going to share two types of plastic extrusion –– Plastic recycling extrusion and blown film extrusion for plastic recycling and film blowing.
Plastic Recycling Extrusion
Plastic recycling extrusion is a process used to transform recyclable plastic materials into plastic pellets to be used in the production of new products. Here is the step-by-step explanation of the plastic recycling extrusion:
1. Before Processing
The first step in plastic recycling involves sorting waste by type (polyethylene, polypropylene, etc.) and removing contaminants like paper, metal, labels, and non-plastic parts. The sorted plastics are then washed and dried to eliminate dirt and impurities.2. When Materials Processing in the Extruder
The dried plastic wastes (large-sized need to pre-crush) are fed into the extruder, which is a heated cylinder with a rotating screw inside. The extruder melts the plastics into fusion type first, when plastic passes through the extruder, the degassing system is there for humidity removal followed by a filtration system used to exclude the dirt. Making plastic melt in the extruder is for the shape reforming, making the plastic easier to process and pelletize.3. Pelletizing and Final Output Product
Once upon exiting the barrel, the molten plastic is forced through a die, which shapes the melt into the desired shape, such as pellet types. Some plastics with a high flow index (extremely runny) will be using a strand-type pelletizing system.4. Cooling and Dry
After exiting the die, the extruded plastic plunges into the water tank for rapid cooling, which helps the recycled pellets remain uniform. Then, they are dried by the centrifugal dryer. After collecting the recycled plastic pellets, the producers can make them for different uses.Plastic Blown Film Extrusion Process
Briefly stated that plastic blown film extrusion is a process used to manufacture plastic films or plastic bags by melting the plastic raw materials or recycled plastic pellets.
The blown film extrusion process involves melting plastic pellets, and then forcing the molten material through a circular die. Air is introduced into the center of the die, causing the molten plastic to expand into a bubble shape. The bubble is then cooled by air to solidify the plastic into a thin film, finally, the film is flattened and winded onto the rolls for further processing or use.
1. Material Preparation
The raw plastic material, typically in the form of pellets or granules, is dried to remove any moisture that may be present. This is crucial as moisture can negatively affect the quality of the final product.2. Extruder
The dried plastic pellets (which can also mix with some % of recycled pellets to reduce the production cost), are fed into the extruder, and then heated by a cylinder with a rotating screw inside. Then, the molten plastic will transfer to the die head in a continuous stream.3. Air Cooling Ring
Immediately after exiting the die, the molten plastics passes through an air-cooling ring, which blows cool air onto the tube's surface, cools down the bubble, and makes it solidity, the bubble-forming section, which is also called bubble stabilizer, holds the plastic tube and take the films up to the folding part.
After that, the bubble is collapsed and flattened by a pair of nip rolls or a collapsing frame and wound onto the rolls by the winder to the desired product form. The output product of blown film extrusion is a thin, continuous film or sheet of plastic, this extrusion process is commonly used to produce plastic films with various properties and characteristics
Recycling Extrusion | Blown Film Extrusion | |
---|---|---|
Plastic Types | PE, PP, EPS, PS, PC…etc | Mostly PE/PP |
Purpose | Recycle waste to create new products | Make plastic films/sheets for bag production or film application |
Processing Way | Melt plastics to form new shapes | Melt plastics to form new shapes |
Output Materials | Plastic Granules/Pellets | Plastic Film |
Conclusion
The plastic recycling extrusion process allows for the conversion of post-consumer or post-industrial plastic waste into new products, reducing the need for virgin plastic materials and promoting a more sustainable and circular economy, while the blown film process is commonly used to produce plastic films for packagings, such as supermarket bags, and garbage bags, and industrial applications like greenhouse films, agricultural films and heavy-duty tarpaulins.
Thinking of starting your own business in the plastic recycling or blown film industry? Contact POLYSTAR today to explore the exciting possibilities of plastic recycling and blown film technology!
Learn More
About the Author
Sandy Kuo
E-Marketing SpecialistSandy follows up on the market demand and analysis data in the plastic industry, promoting the brand and doing digital marketing activities by e-commerce.