We use cookies and other tracking technologies to improve your browsing experience on our website, By clicking "Accept All," you agree to allow cookies to be placed to enhance your browsing experience on this website to show you personalized content and targeted ads, to analyze our website traffic, and to understand where our visitors are coming from. You can manage your cookie settings below. Clicking "Confirm" indicates your agreement to adopt the current settings.
Recycling - Bigger Pelletizing Extruders in High Demand
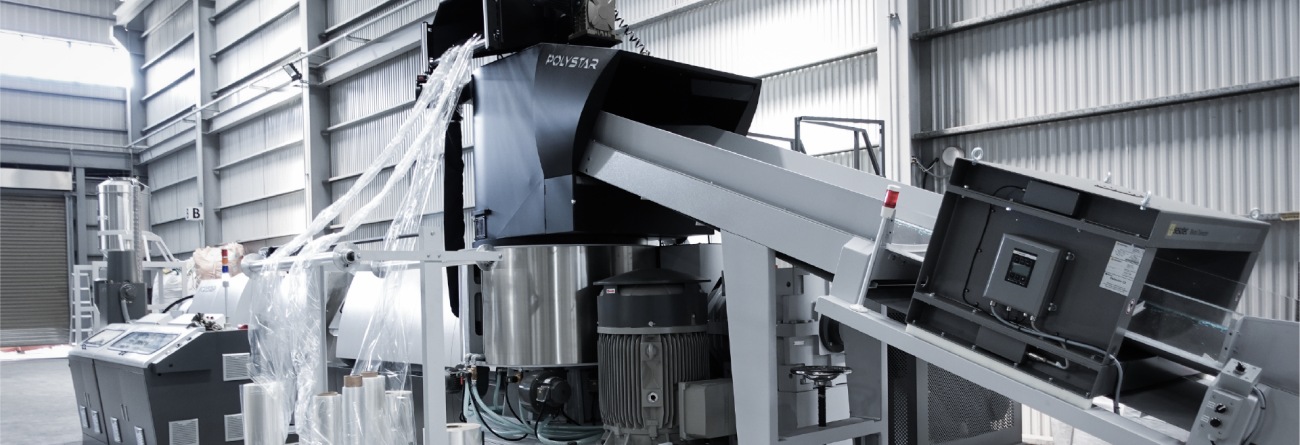
Higher-capacity recycling equipment is required.
With the great importance of recycled-based products for both rigid and flexible packaging, the global demand for plastic recycling is expanding. Recyclers are now purchasing much plastic equipment at once, as well as the bigger pelletizing extruders.
The 800-1,000 kg/hour plastic granulator machine has already become the standard machine for post-consumer and even some post-industrial recyclers.
This new trend is more evident when two post-consumer recyclers - one located in Japan (Kanagawa) and the other one in Mexico City, both placed an order of four 800-1,000 kg/hour machines all at the same time to be able to fulfill the increasing recycling demand of washed PE film, HDPE bottles, and PP woven bags.
In the same period, several recyclers in Australia, India, Colombia, Saudi Arabia, UAE and the US have also repeated their orders with multiple (at least 2) higher-capacity machines from POLYSTAR.
Cutter-compactor increases the output of large plastic recycling lines.
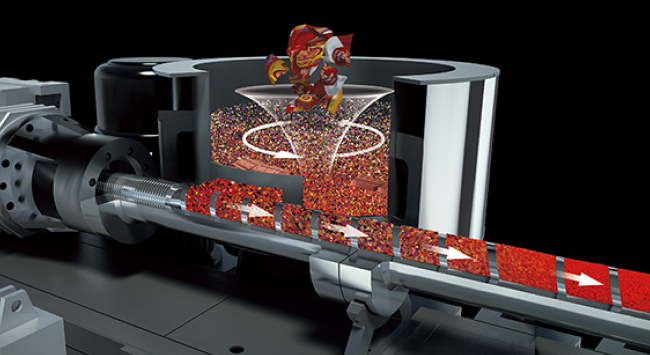
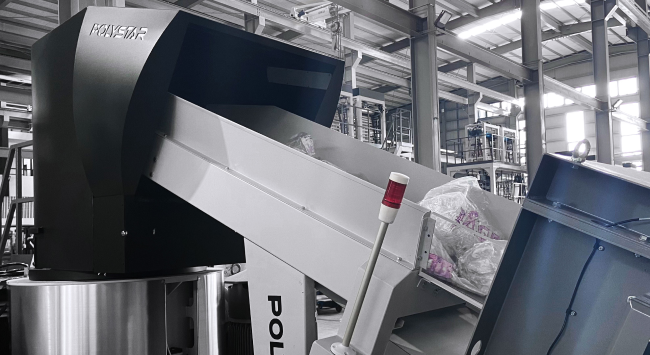
Feeding consistency is key for big recycling extruders
-
( PP flakes fed in by belt conveyor )
-
( Pre-crush PP milk bottle )
When recycling rigid plastics such as PE bottle flakes from milk and shampoo bottles or regrind from injection products, the cutter-compactor functions to regulate the feeding speed of the material and prevents over-feeding to the extruder. It also works well with hot, rigid materials coming from the squeezer dryer, as the constantly-rotating compactor further prevents the material from sticking to each other and bridging. In addition, the pre-conditioning process inside the compactor softens the rigid material, which reduces the shearing force and therefore minimizes the wearing on the extruder screw and prolongs its lifespan.
Two-stage pelletizing machines for post-consumer recycling
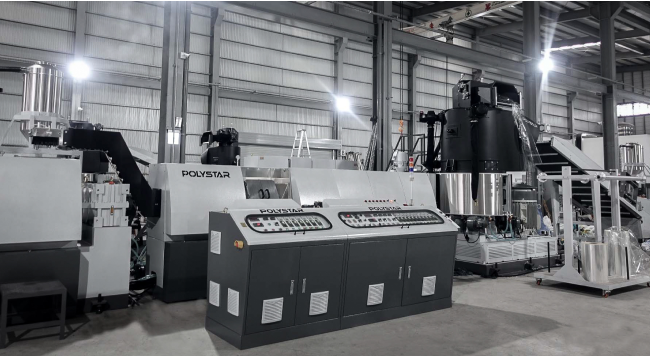
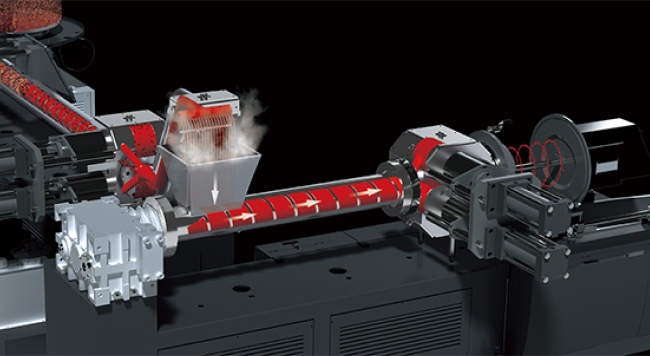
About the Author
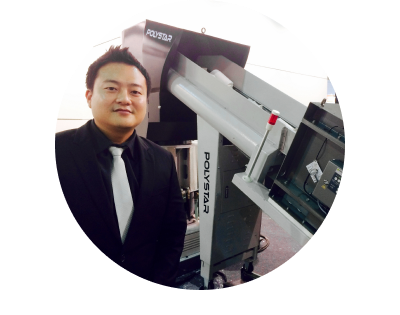
Jack Lin
Sales ManagerJack has visited and spoken to hundreds of POLYSTAR machine users around the world over the last 10 years. Having collected practical information on customer feedback and user experiences, he enjoys sharing the advantages and disadvantages of using different types of machines with others, especially coming from the customers' perspectives.