We use cookies and other tracking technologies to improve your browsing experience on our website, By clicking "Accept All," you agree to allow cookies to be placed to enhance your browsing experience on this website to show you personalized content and targeted ads, to analyze our website traffic, and to understand where our visitors are coming from. You can manage your cookie settings below. Clicking "Confirm" indicates your agreement to adopt the current settings.
Maximize Plastic Film Sheet Production with One Machine
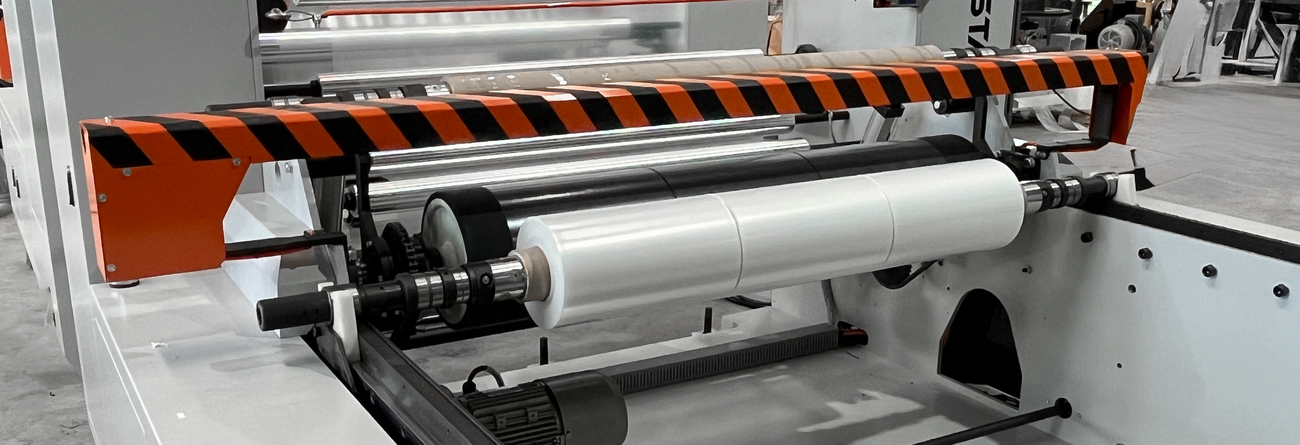
Choosing the right size of blown film machine is crucial when planning your production, and a key factor in doing so is the maximum width of the film you will produce. However, if your goal is to produce narrow plastic film sheets, we have a clever strategy to help you maximize your output.
1. What is the difference between a Film Sheet and a Tubular Film?
Before diving into efficient film sheet production, let's clarify the difference between film sheets and tubular films.
Blown film machines, which produce plastic film, are commonly used to produce tubular film rolls of plastic. These are obtained by simply flattening and winding the entire bubble made during the extrusion process. Winding the bubble as a whole creates a pocket that is used to store goods. Some examples of applications that use tubular films are t-shirt bags, garbage bags, shrink film in tubes, bottom sealed bags, gusseted bags, side sealed bags, disposable gloves, bakery bags, etc.
On the other hand, film sheet rolls are obtained by slitting that same bubble (or tube) on the sides before it is winded, dividing the tubular film into two separate film sheets. Film sheets are used to manufacture products such as table covers, sufra film, furniture covers, agricultural film, shrink film sheets for sleeve wrapping machines, courier bags, and some types of packaging that require only a layer of plastic instead of a tube.
In contrast to film sheets, tubular films (uncut at their diameter) are ideal for bags and similar applications. While film sheets are perfect for processes that require extending the film to cover a surface or object. They're also well-suited for applications where the plastic needs to be folded before filling and/or sealing. For example, some types of packaging like vertical form seal need rolls of film in sheets in order to package goods.
Now, let's explore how to efficiently produce film sheets.
1. Transforming Tubular Film into Film Sheets
To produce film sheets using your blown film machine, you'll need a double winder. These devices take the tubular film and transform it into separate film sheets. They achieve this by using side-opening knives to slit the film and then separating each sheet for individual winding.
Double winders come in both automatic and manual options. Additionally, they can be set up with a back-to-back or up-and-down configuration depending on the size requirements.
How can I produce narrow film sheets efficiently?
For producers aiming to create narrow film sheets, here's a valuable strategy to consider: increasing the overall film width produced by your machine. Instead of investing in a machine specifically for 400mm film, you can multiply the width of the film sheet you plan to produce and opt for a machine that can handle a wider width, for example 1200mm.
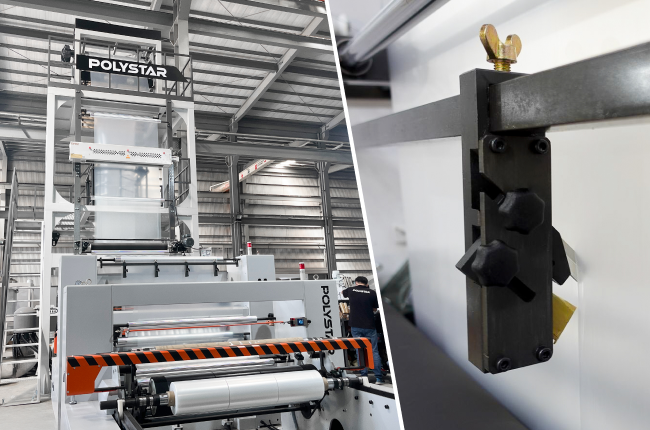
The reason why we recommend this is because our blown film machines can incorporate a device called a cold slitting knife, which helps vertically slit the film sheets to divide them into more narrow rolls before winding. For instance, if you incorporate 2 sets of these knives to your machine, you can slit a 1,200mm film sheet into 3 sets of 400mm sheets (2 sheets are obtained per tube = 6 sets of 400mm film sheets produced per machine). Making this strategy a great option to help you significantly increase your production output.
This technique is widely used by producers of small-width film sheets. It allows them to maximize production space, save energy, and gain versatility by investing in a machine capable of producing a wider film width. One of the main advantages is that if the manufacturer also wishes to produce another product that requires a larger width, the knives can simply be set aside to allow producing a film of the maximum width without needing to invest in a separate machine.
Which machines are recommended for producing wider film sheets?
If you plan to apply the strategy we described above, you can consider any of the following machines depending on the specific characteristics of the film you are looking to produce:

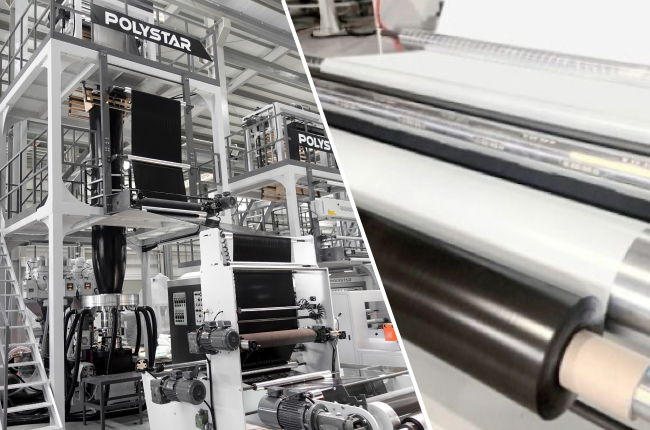
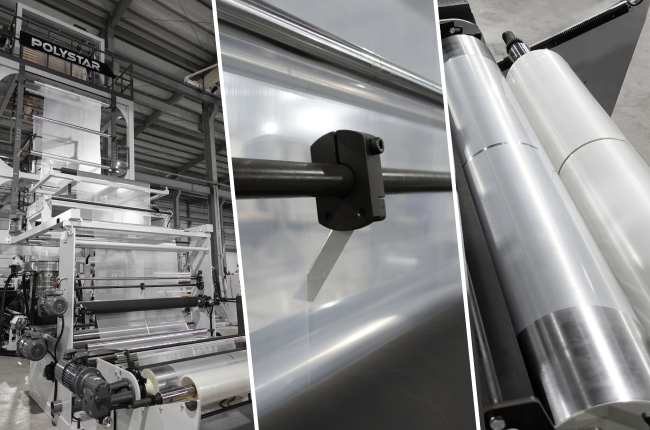
Producing more film sheets on roll with one machine is possible if you use a wider blown film machine and incorporate cold slitting knives. This method will allow you to multiply your film sheet output.
For more information about machine recommendations for your specific products, do not hesitate to contact POLYSTSAR. Our sales team will be happy to come up with a solution to help you make the most out of your next machine.
About the Author
Renee Castro
Renee is helping plastic producers find simple solutions to their problems. She is interested in topics like the circular economy and the latest recycling trends.