We use cookies and other tracking technologies to improve your browsing experience on our website, By clicking "Accept All," you agree to allow cookies to be placed to enhance your browsing experience on this website to show you personalized content and targeted ads, to analyze our website traffic, and to understand where our visitors are coming from. You can manage your cookie settings below. Clicking "Confirm" indicates your agreement to adopt the current settings.
How to Reprocess Highly Printed Films? PE, PP, BOPP
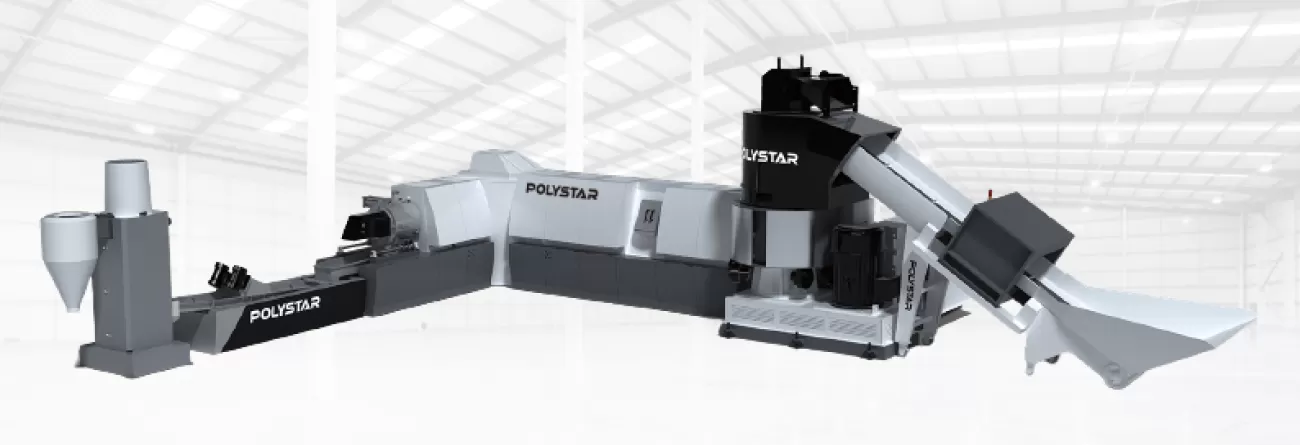
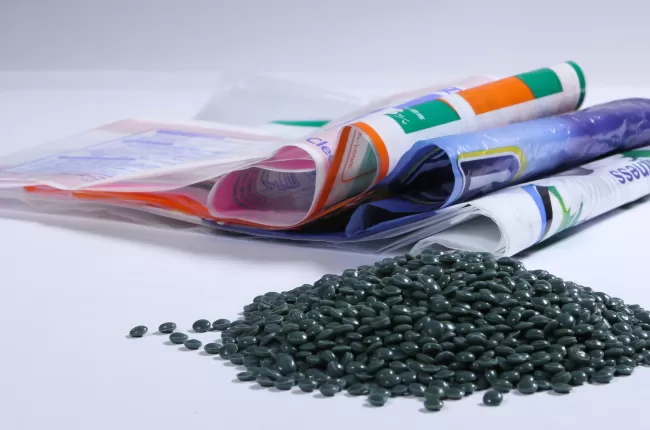
The laws toward plastic have become stricter, which require the producers to use a higher percentage of recycled material in their final products. The benefits of these laws are for lowering the production cost of the producers and reducing the plastic waste in our environment.
New standards for plastic pellets
Plastic producers and professional recyclers started to pay more attention to products that can be recycled but were difficult to reprocess.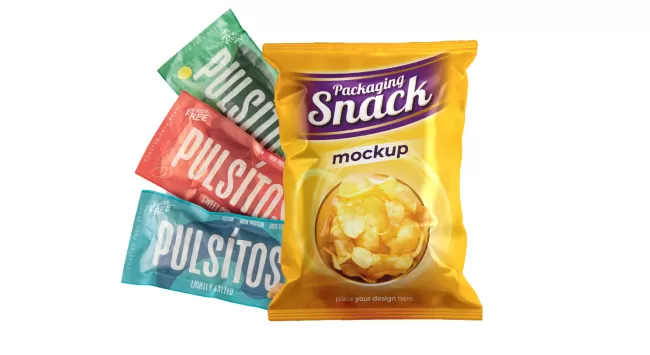
Here are the examples:
- Highly printed film (PE and PP)
- Flexible packaging
- Laminated film
- Multilayer film
- BOPP film
Producers can notice this when pellets are used again in the production line (blown film machines and injection machines). In other words, getting better quality pellets has become the priority for plastic producers.
Why should you reconsider a Two-stage recycling machine?
POLYSTAR, through reengineering, designed the perfect solution: Repro-Flex Plus.
Repro-Flex Plus is able to reprocess the highly printed material and improve the quality and productivity of the recycled pellets. With a two-stage recycling system, two filtration and three degassing steps ensure the minimal degradation of the material, which produces uniform pellets for reprocessing directly into your production line.
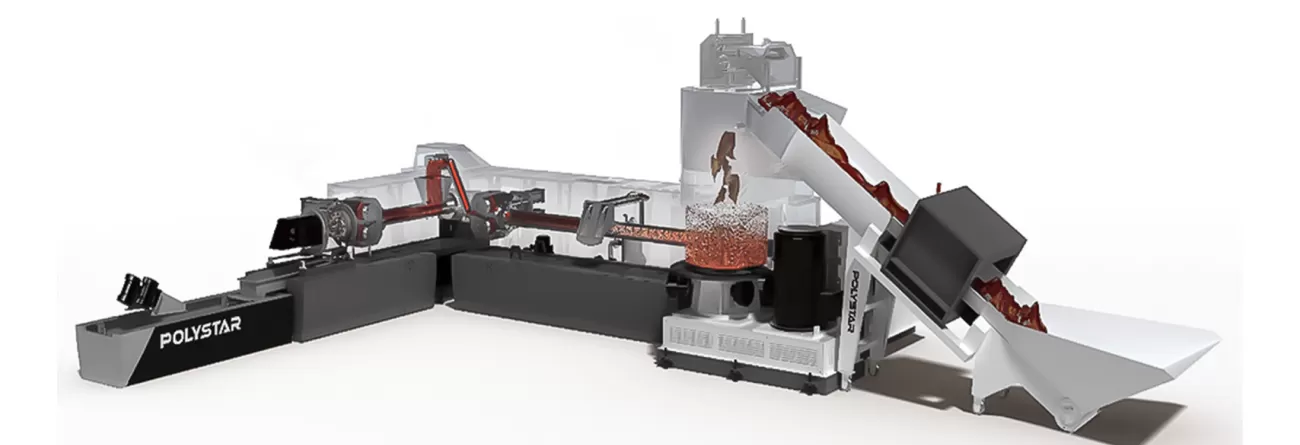
Simple in Design. Simple in Operation.
Two-stage recycling system- Special design on the first and second extruder.
The second extruder stabilizes the process, reducing the degradation of the material.
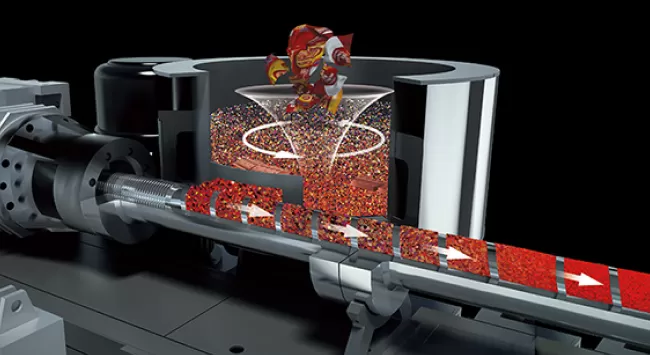
Cutter compactor
This cutter-integrated pelletizing system eliminates the necessity of pre-cutting the material, because the cutter-compactor pre-cuts, pre-warm and mixes the material that will be fed directly into the extruder with a centrifugal force.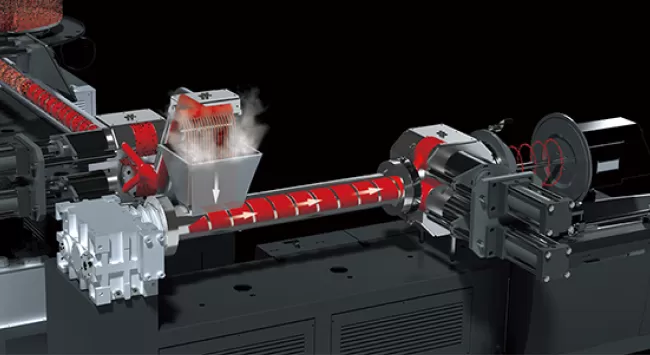
Tripe degassing
In addition to the double degassing in the first extruder, the venting area (the connection between the first and second extruder) serves as a third degassing section to further remove the ink and extra humidity level from the material.Higher capacity and Cost reduction.
Repro-Flex Plus is designed with advanced technology, which reduces the operational cost and energy consumption. Both plastics producers and recyclers have noticed the benefits of Repro-Flex Plus while recycling laminated films, multilayer films, and films with a high percentage of printing areas on the surface.
Finally, Polystar offers not only simple solutions for plastic producers but also instant after-sales services. What’s more, Polystar has agents and technicians around the globe. These representatives specialized in Polystar Machines, giving machine installations and after-sales as well.
About the Author
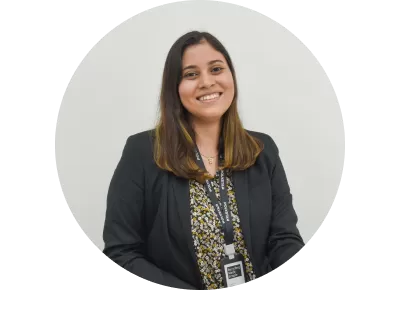
Maria Lopez
Marketing ManagerMaria Lopez is a content marketer at POLYSTAR. She authors in-depth guides that provide solutions to Plastic Producers. Not only to select your machine but also to keep you updated with the new trends.