We use cookies and other tracking technologies to improve your browsing experience on our website, By clicking "Accept All," you agree to allow cookies to be placed to enhance your browsing experience on this website to show you personalized content and targeted ads, to analyze our website traffic, and to understand where our visitors are coming from. You can manage your cookie settings below. Clicking "Confirm" indicates your agreement to adopt the current settings.
What are the Similarities and Differences Between LDPE and HDPE?
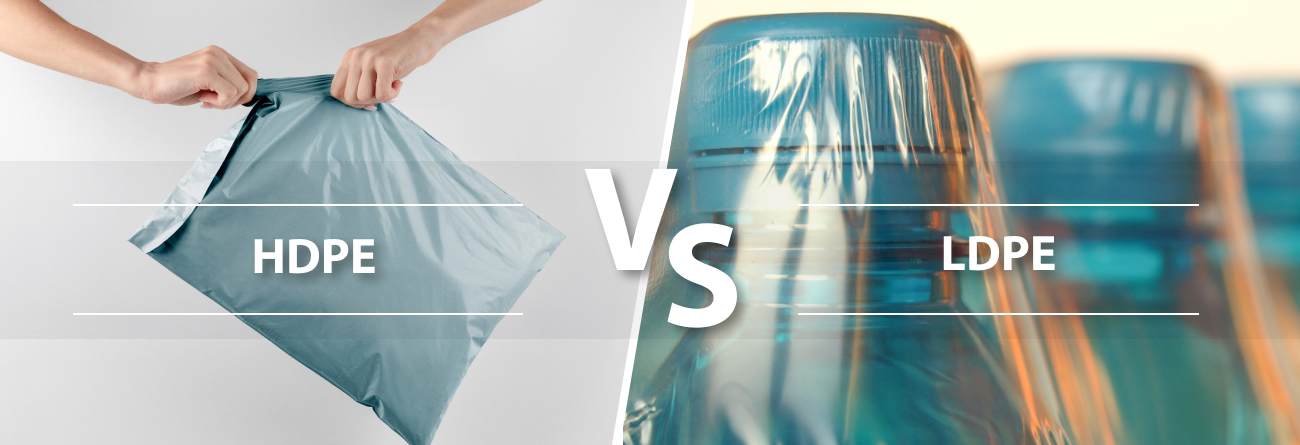
Why do producers choose polyethylene (PE) to manufacture plastic products over other polymers? Over the years, it has become a common type of plastic due to its several advantages in the market. For instance, it has a lower cost than other polymers, is highly resistant to electricity and chemicals, and has valuable properties such as being moldable, flexible, and impact-resistant, making it efficient in every plastic production process.
PE is divided into different types or branches according to their molecular and structural differences. Each type achieves distinct application requirements. In this article, we will briefly explain the similarities and differences between LDPE and HDPE, alongside some suggestions on recommended applications for each.
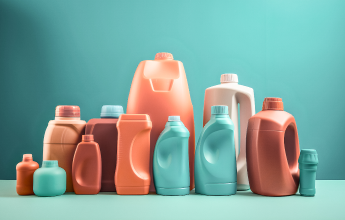
HDPE (High-density Polyethylene)- Strength and Resistance
All these properties have made HDPE one of the most popular plastic materials for different applications, which we will discuss in this article. In contrast to low-density polyethylene (LDPE), HDPE has higher density and less branching, resulting in a more rigid and less flexible material.
Overview of HDPE’s Properties
Properties | Description |
---|---|
Density |
0.93 – 0.97 g/cm3 |
Melting Point |
Between 120°C to 130°C |
Flexibility |
More rigid and tougher due to its linear structure |
Appearance |
Opaque and translucent (depending on its thickness) |
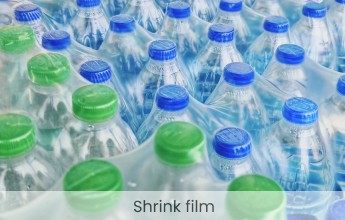
LDPE (Low-density Polyethylene) - The Flexible Plastic
Overview of LDPE’s Properties
Properties | Description |
---|---|
Density |
0.910 – 0.940 g/cm3 |
Melting Point |
Between 106°C to 115°C |
Flexibility |
More flexible due to its branched structure |
Appearance |
Translucent and transparent (depending on its thickness) |
Difference Between LDPE and HDPE: Production and Applications
Plastic film producers may decide which material to use for production according to their application requirements since LDPE and HDPE offer different advantages.
HDPE Applications
As we have mentioned earlier, HDPE is more resistant than LDPE. This is why plastic producers might prioritize applying HDPE when producing rigid materials in different manufacturing processes such as injection molding, blow molding, and 3D printing. HDPE is widely used in the manufacturing of plastic containers and bottles, as well as in the production of irrigation pipes, toys, playground equipment, and outdoor furniture such as chairs and tables.
HDPE is the preferred choice for plastic film applications that require high resistance to punctures or tears and to be able to pack heavy items within it. Some HDPE applications in the plastic film market include:
- Heavy-duty bags
- T-shirt bags
- Construction film
- Courier bags (shipping envelopes)
Most of these applications involve two or three plastic film layers, mostly known as co-extrusion. POLYSTAR offers AB and ABA co-extrusion blown film machines, which consist of 2 extruders to produce plastic films with two layers (AB) and three layers (ABA). In the following pictures, you may find a brief comparison between both plastic film layer structures.
-
(Layer structure of an AB blown film machine)
-
(Layer structure of an ABA blown film machine)
LDPE Applications
LDPE plastic films also share these same properties. Producers who wish to bring new, resistant, flexible, and transparent products to the market tend to choose LDPE over HDPE. Even though LDPE and HDPE may be used to produce the same or similar plastic products, LDPE dominates the plastic film and packaging market to protect other products. LDPE has a low heat resistance and melting point, making it an excellent material for heat-sealing packaging applications. It is suitable for the following plastic film applications:
Difference Between LDPE and HDPE: Recycling Code
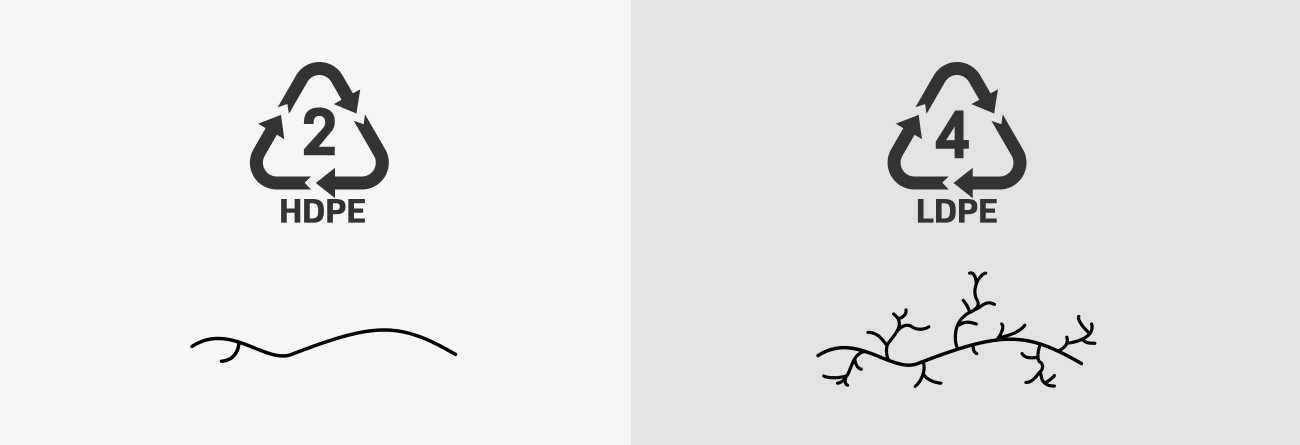
POLYSTAR offers the most optimal solution for recycling these two materials in the same machine! Our recycling machines process several HDPE and LDPE post-industrial waste. For instance, POLYSTAR Repro Flex’s cutter compactor is suitable for recycling plastic film, film scraps, and garbage bags, among other materials. If you want to recycle hard plastic bottles, plastic lumps, or film rolls, our shredder-integrated recycling machine, Repro-One, is the adequate solution! Additionally, if you have any HDPE or LDPE post-consumer waste, Repro-Flex Plus is the machine you are looking for!
Conclusion
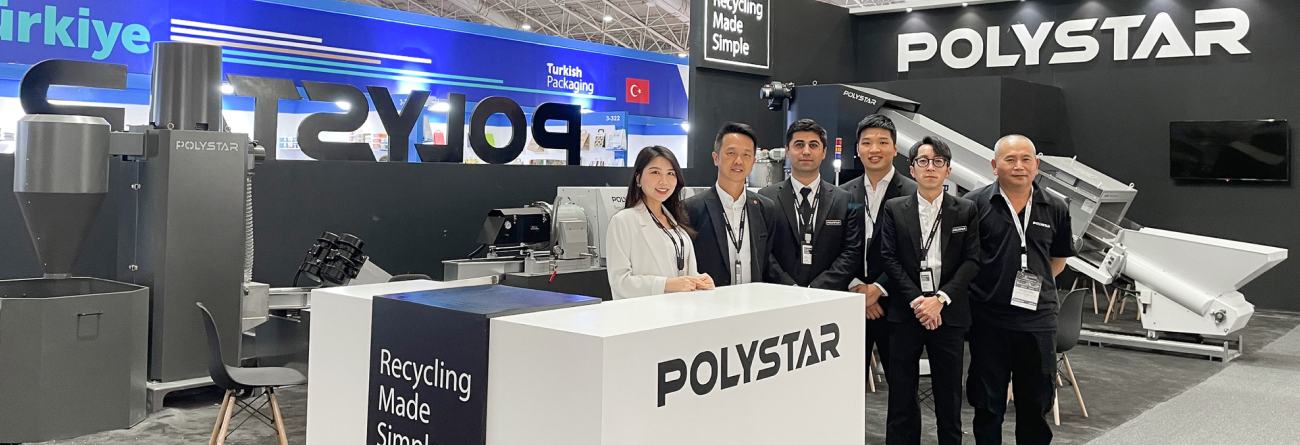
(POLYSTAR provides simple recycling solutions)
Even though their applications might be somewhat similar, the reasons why a producer might choose one over the other will strongly depend on the product’s purposes. For instance, if a producer is looking for a much more flexible and translucent material suitable for packaging, then LDPE would be recommended for his production. On the other hand, if a producer wants a more rigid and resistant product, he might consider HDPE rather than LDPE.
HDPE and LDPE are labeled under different recycling codes, but their recycling process is very similar because they are both thermoplastics. For this reason, some recyclers might choose to recycle them separately. However, POLYSTAR offers you the most efficient and cost-effective recycling machines!
If you wish to know more about HDPE and LDPE plastic film production or recycling, contact POLYSTAR’s experienced sales team! We are here to provide any information and advice regarding your needs and requirements.
Read More:
About the Author
Kevin Umanzor
International SalesKevin advises plastic producers to adopt a circular economy by implementing innovative POLYSTAR machinery. Driven by a commitment to providing the best possible solutions to his clients, Kevin is committed to broadening his learning process by interacting with diverse markets across the globe.