We use cookies and other tracking technologies to improve your browsing experience on our website, By clicking "Accept All," you agree to allow cookies to be placed to enhance your browsing experience on this website to show you personalized content and targeted ads, to analyze our website traffic, and to understand where our visitors are coming from. You can manage your cookie settings below. Clicking "Confirm" indicates your agreement to adopt the current settings.
Advanced yet Easy-to-Use Blown Film Extrusion Technology – Key to Eco-friendly Packaging
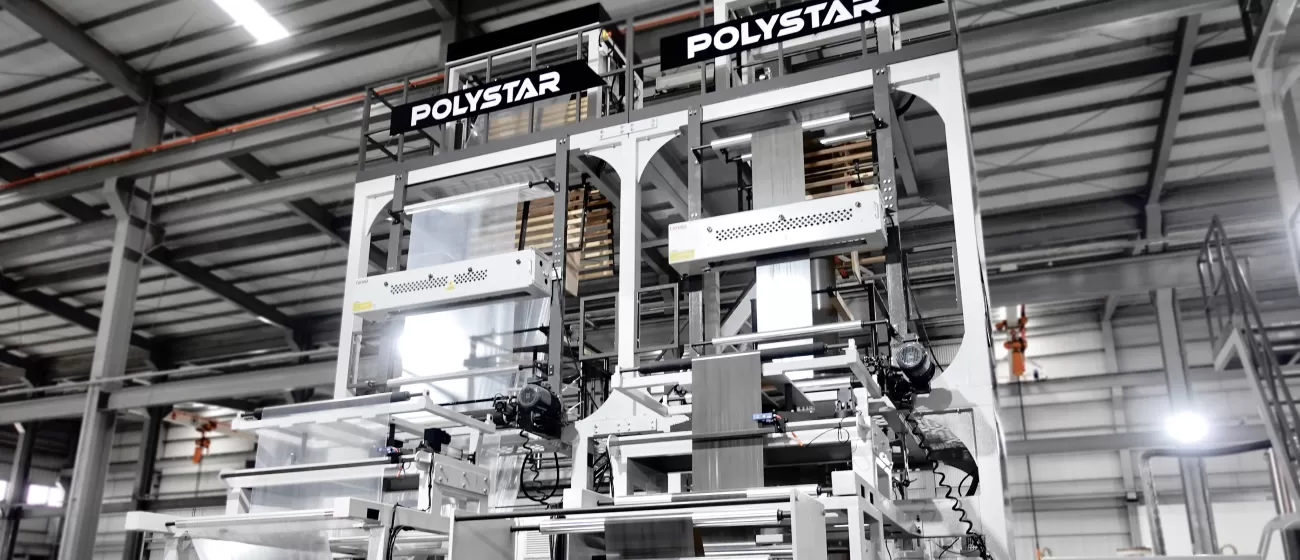
Eco-friendly packaging is a necessity more than a trend, for both environmental and economic sustainability today. As one of the main carriers of packaging film production, blown film extrusion technology must keep evolving to meet the market requirements.
Let’s take a closer look into how POLYSTAR develops its blown film extrusion machine technology to better contribute to eco-friendly packaging.
Stable operation saves material and reduces wastes
Whether monolayer extruders or co-extrusion machines, POLYSTAR blown film machines have gained the fame of stable operation among our customers in more than 110 countries. We witness our customers producing films for their specific product requirements smoothly due to the precision in the screw and die head designs; carefully testing parameters like temperature, heating/cooling rates, film width, thickness, and tension. This operation stability not only saves from defective scraps but also saves energy and labor hours.

Moreover, the simple design of the blown film extruders makes the production process easier for the operators. Hence, the operators can manage multiple POLYSTAR-blown film extruders simultaneously.
Material optimization keeps you sustainable and profitable
PE derivatives are often used in blown film extrusion. These materials are highly recyclable and producers often blend PE, HDPE, LDPE, and LLDPE with each other as well as with the bioplastics, CaCO3, recycled plastics, and color or filler masterbatches.
POLYSTAR designs its screws for excellent blending and melting performance for these various tasks of film producers. As a result, the producers will be more flexible to optimize the materials desired and use more recycled plastics, while they will be less dependent on virgin polymers.
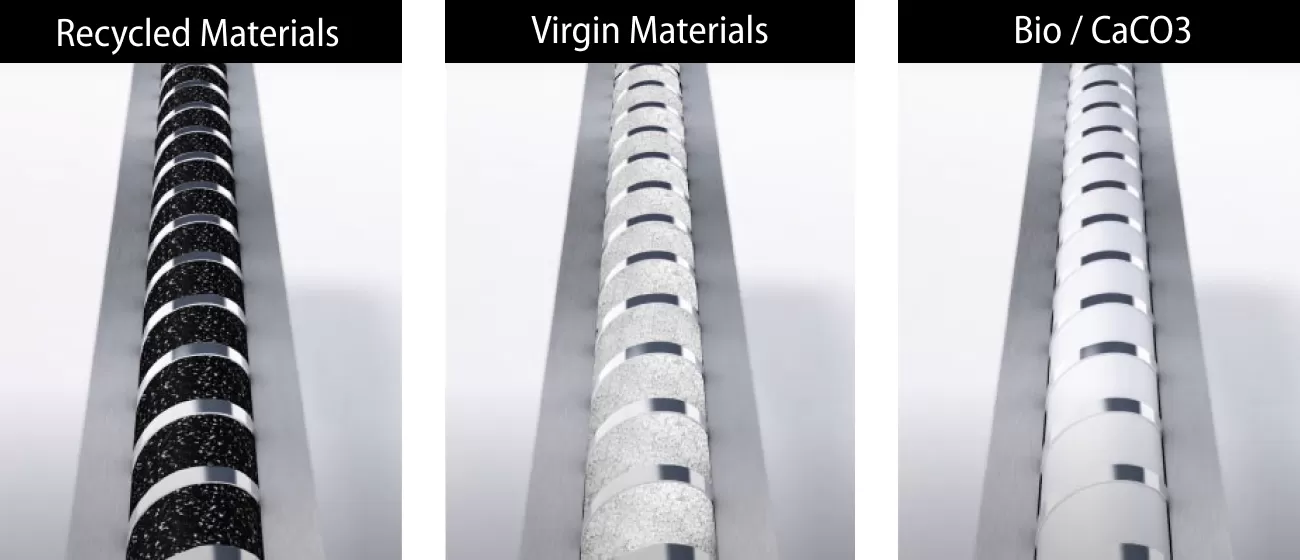
In terms of material saving and reducing carbon footprint, many POLYSTAR customers are upgrading their mono-layer blown film machines to ABA three layer blown film machines. The most prominent advantage of an ABA film extruder is the ability to use more recycled plastics and CaCO3 in the mid-layer (B) while having a smooth surface on the outer layers (A). Producers can manufacture more eco-friendly, 3-layer strong films with only two extruders.
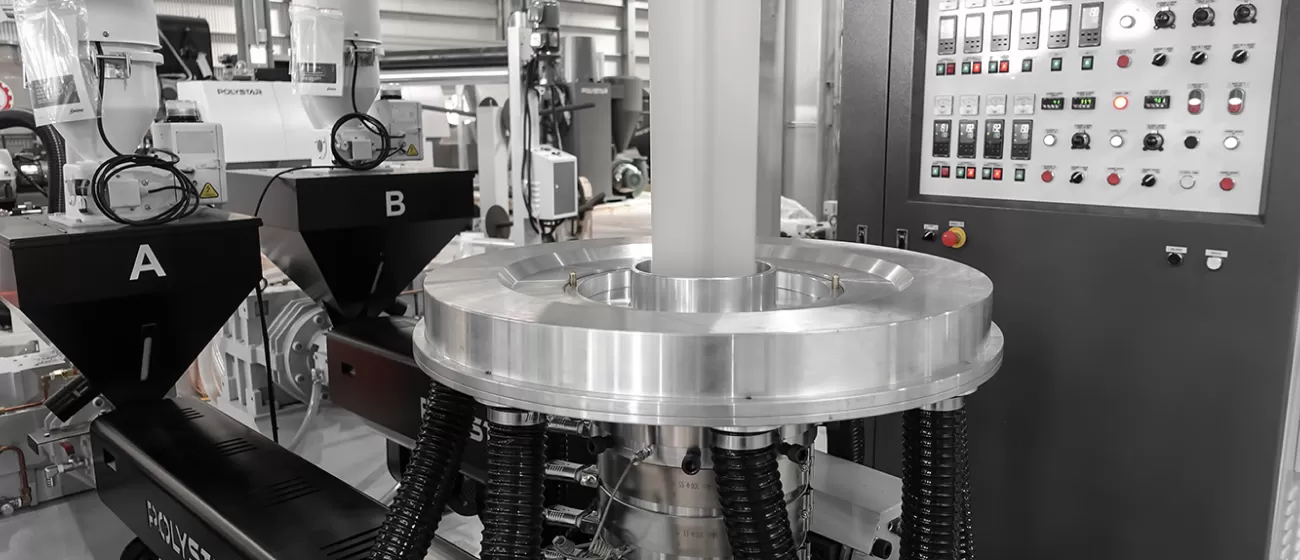
Production flexibility with custom-made machines reduces carbon footprint
Before deciding to purchase a blown film machine, it can be advantageous for you to contact our sales specialists, to get suggestions on what types of machines are more feasible for your production. Because POLYSTAR focuses on highly customizable blown film extruders to save you energy, space, and material.
For instance, twin-head blown film extruders produce two different widths & thicknesses of film rolls at the same time on different winders, while using only one extruder. The optimal width interval of the machine allows it to cover most of the plastic bag applications in the market including t-shirt bags, garbage bags, flat shopping bags, bags on rolls, etc.
About the Author
Resul Gökpınar
International SalesResul creates up-to-date content based on his experience, gained by solving customers' problems in Turkey and the EMEA market.