We use cookies and other tracking technologies to improve your browsing experience on our website, By clicking "Accept All," you agree to allow cookies to be placed to enhance your browsing experience on this website to show you personalized content and targeted ads, to analyze our website traffic, and to understand where our visitors are coming from. You can manage your cookie settings below. Clicking "Confirm" indicates your agreement to adopt the current settings.
7 Solutions to Common Plastic Recycling Operation Problems
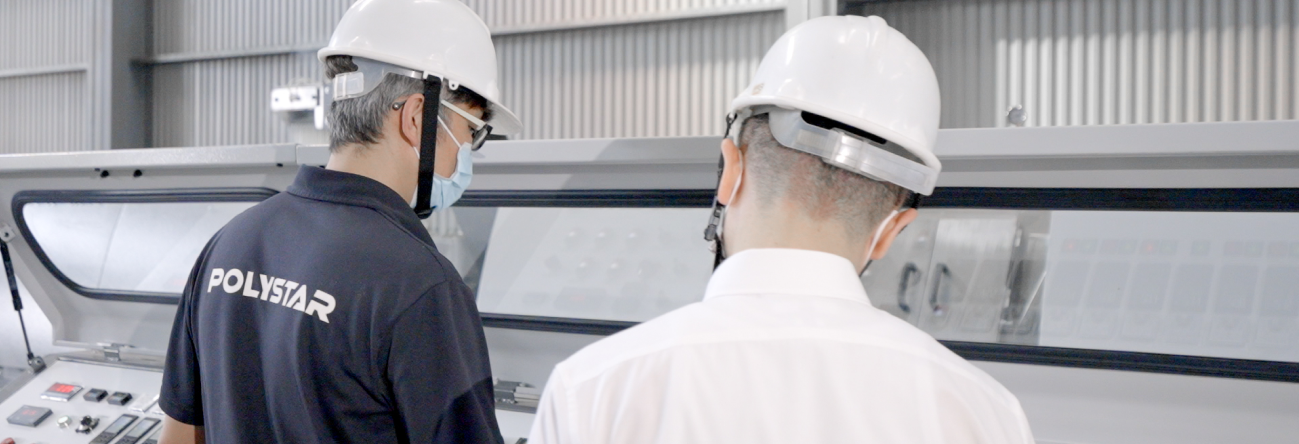
7 Common Plastic Recycling Operation Problems
1. Material Feeding Instability
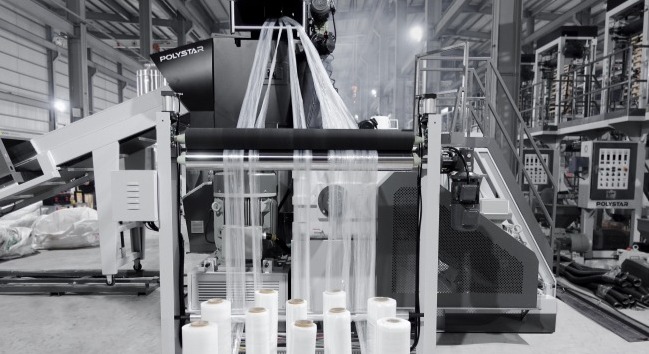
Solution:
2. Contamination of the Plastic Material
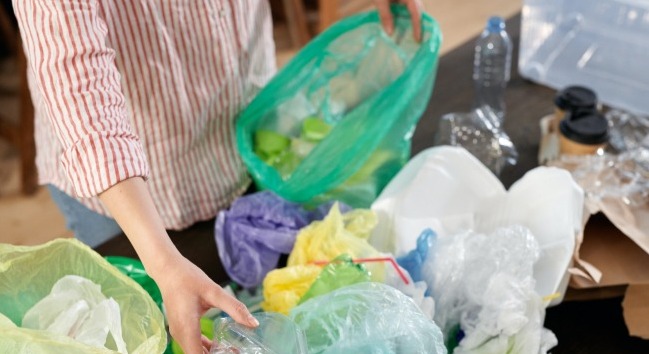
Solution:
3. Blockages and Hopper Bridging
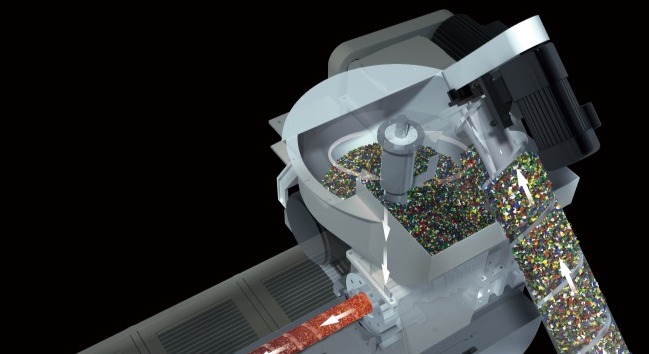
Solution:
Proper preparation based on the type, shape, and condition of the waste material for your specific recycling machine, and using auto-feeding systems can help solve many of these plastic recycling problems related to blockage. Periodic maintenance on the machine components, regularly changing filter meshes, and unclogging the die head are also easy and common preventive. Using force feeders for hopper-feeding recycling machines can help prevent the plastic recycling problem of material bridging.4. Overheating
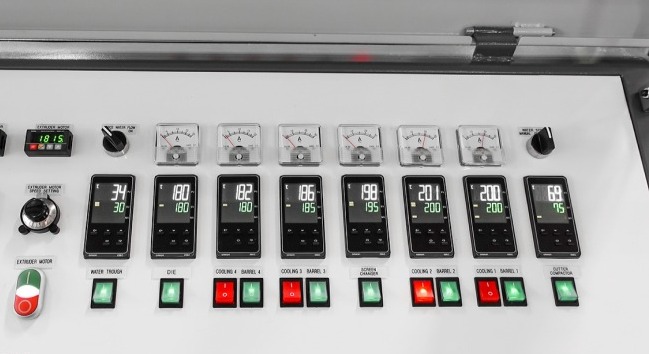
Solution:
5. Sticky Plastic Pellets
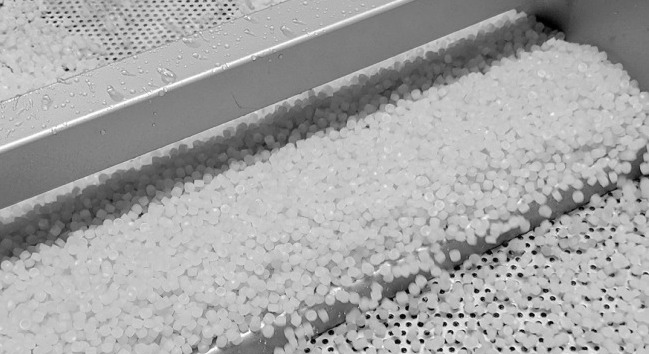
Solution:
Using a centrifuge dryer can also prevent pellets from sticking to each other while also further drying them. tacking another of the plastic recycling problems.
Using a chiller, especially for hot climates, is also suggested.
6. Hollow Plastic Pellets
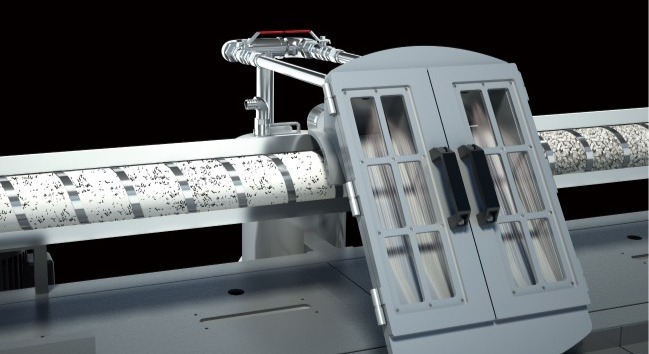
Solution:
Vacuum degassing system options based on the condition of the material is an effective solution to remove gas from the materials which causes hollow pellets.Adjusting the right and stable temperature on particular zones of the recycling extruder and die head provides smooth plasticization.
Adjusting the right cooling water temperature and speed (not too cold and not too fast) prevents recycled pellets from forming a hollow shape, tackling yet another issue among the various plastic recycling problems.
7. Non-uniform Pellets or Chunks
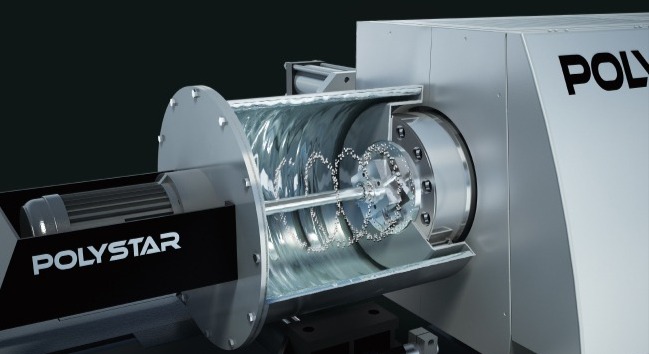
Solution:
Stabilizing material feeding, ensuring smooth melt flow with the right temperature adjustment and preventing clogging, and using an auto speed and pressure-controlled pellet cutting system will solve most of the non-uniform pellet output problems related to plastic recycling.
Such as the POLYSTAR water ring pelletizer automatically adjusts pellet cutting speed based on the speed of the melt coming out from the die head. The system also ensures the pelletizing knives are always positioned on the die head synchronously with the die head pressure.
This results in cutting uniform size and shaped pellets all the time. Dull pelletizing knives or their improper disposition might cause plastic recycling problems of chunk creation. Replacing the knives with original spare parts and maintaining the right position can solve this problem associated with plastic recycling.
How to Choose a Stable Plastic Recycling Machine?
While investing in a plastic recycling machine, recyclers, and plastic producers are suggested to consider the machine's performance, user-friendliness, and ease of maintenance all together to avoid potential plastic recycling problems. A stable plastic recycling machine must work in harmony with its all sections and equipment to prevent plastic recycling problems arising from machinery issues.
Moreover, responsive after-sales service with quick spare parts support provides a big advantage and helps you stay competitive in the market in the long run by minimizing downtime due to plastic recycling problems.
Conclusion
Thanks to continuous re-engineering and using world-class components, POLYSTAR is proud to provide stable machine operation performance along with high-quality outputs, minimizing plastic recycling problems. This is one of the important keys to our customers’ fast ROI by reducing issues from plastic recycling problems.
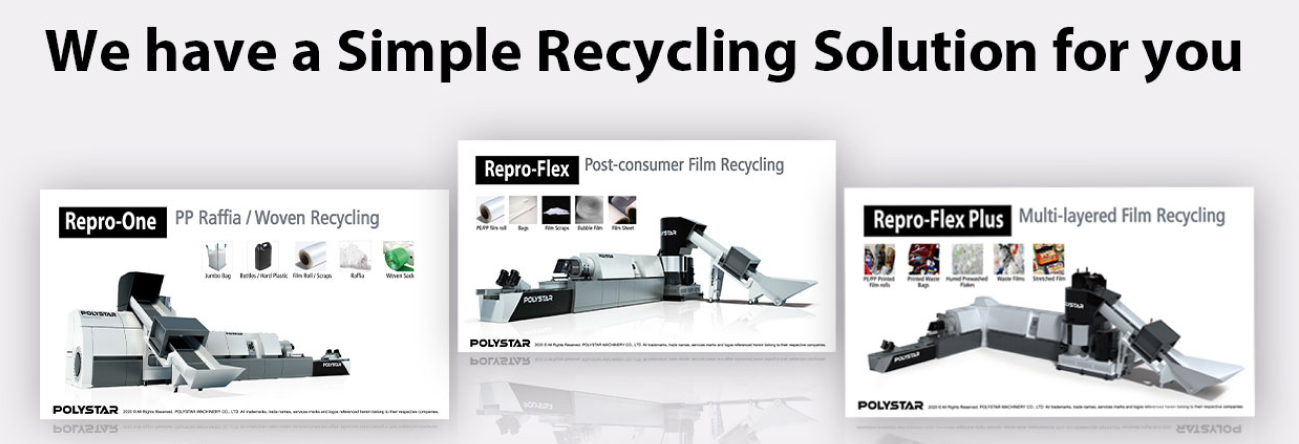
About the Author
Resul Gökpınar
International SalesResul creates up-to-date content based on his experience, gained by solving customers' problems in Turkey and the EMEA market.