We use cookies and other tracking technologies to improve your browsing experience on our website, By clicking "Accept All," you agree to allow cookies to be placed to enhance your browsing experience on this website to show you personalized content and targeted ads, to analyze our website traffic, and to understand where our visitors are coming from. You can manage your cookie settings below. Clicking "Confirm" indicates your agreement to adopt the current settings.
3 Benefits of Using a Gravimetric Dosing Device for Monolayer Extrusion
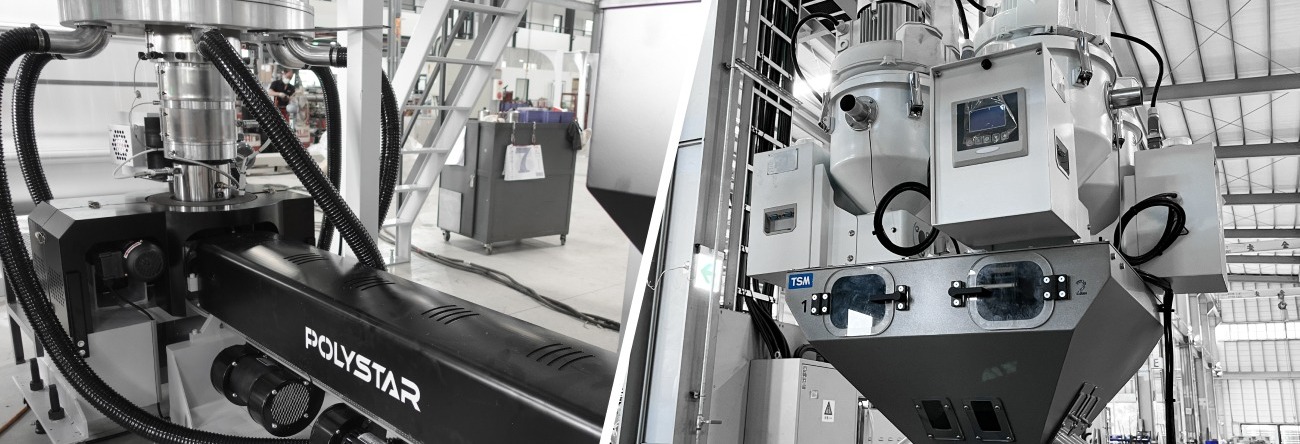
Lately, more monolayer film producers have begun to add gravimetric dosing devices to their blown film machine lines, getting an advantage over their competitors by allowing them to lower their costs. Here we explained 3 benefits of using a gravimetric dosing device for monolayer extrusion.
Gravimetric dosing and mixing devices (or batch blenders) are optional devices added to the feeding unit of blown film machines. These have a hopper form and can accommodate different material components which can be blended and measured by weight.
These devices can be highly beneficial for monolayer extrusion. Although they are usually a standard buy for multilayer extrusion, in this blog we will explain how monolayer film producers can benefit from adding this device to their blown film machines.
How can film producers benefit from using a gravimetric dosing device?
1. Saving masterbatch
Adding a gravimetric dosing device can help producers decrease the amount of masterbatch used in production. Given that masterbatch represents a high-cost percentage for film producers, investing in this device can be highly beneficial. With an inefficient blender or without one, most producers have to add additional masterbatch because the amount used doesn’t get the right results.
This device has a unique mixing screw design, which avoids masterbatch (which is heavier) from staying at the bottom of the mixer by blending it uniformly with the pellets, helping get an even mix and avoiding using extra masterbatch.
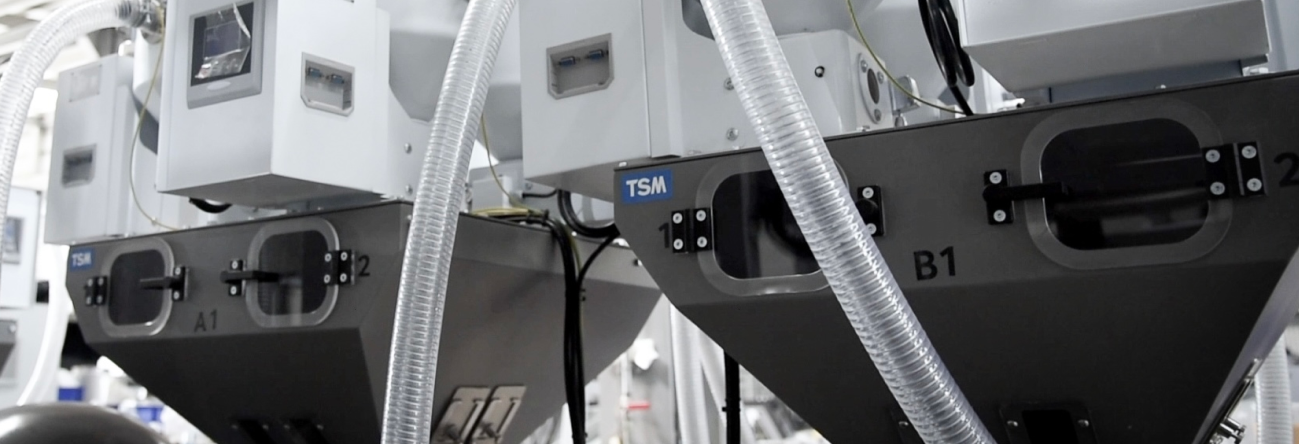
2. Better mixing
Most plastic film producers need the final product to be within a required range, for example, the thickness must be between 20-30 microns. With improper mixing, the granules enter the extruder at a more inconsistent rate, making the film uneven, so producers often have to aim for the highest end of the range to avoid problems with their buyers.With a gravimetric dosing device with extrusion control, producers can ensure the output has a consistent thickness. This can help producers aim for the lower end of the range required, reducing material costs while still providing an end product that meets the standard.
Since the gravimetric device helps material enter the extruder in a more uniform way, it can reduce the material amount needed for production by up to 30% in monolayer extrusion and even help give the film more resistance.
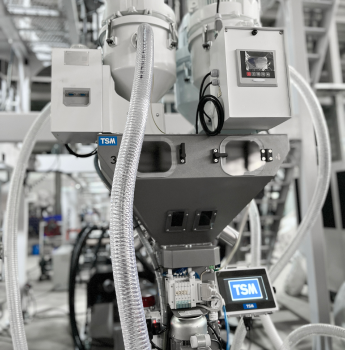
3. Getting precise percentages
Reliable Plastic Extruder with Gravimetric Dosing Device, a Perfect Fit
( Ecuador-based film producer is able to boost the production of his POLYSTAR Star-X, monolayer blown film machine and have better control of its output thanks to the gravimetric dosing device. )
All POLYSTAR machines are simple to operate and maintain, with a design specially tailored to fit the producers' needs, it makes production easy even for operators without experience.
If you are interested in learning more about these machines, don’t hesitate to contact POLYSTAR!
Learn more
About the Author
Renee Castro
Renee is helping plastic producers find simple solutions to their problems. She is interested in topics like the circular economy and the latest recycling trends.