We use cookies and other tracking technologies to improve your browsing experience on our website, By clicking "Accept All," you agree to allow cookies to be placed to enhance your browsing experience on this website to show you personalized content and targeted ads, to analyze our website traffic, and to understand where our visitors are coming from. You can manage your cookie settings below. Clicking "Confirm" indicates your agreement to adopt the current settings.
Plastic Film Recycling Machine
Simple in Design. Flexible in operation
Recycling Processes of Repro-Flex
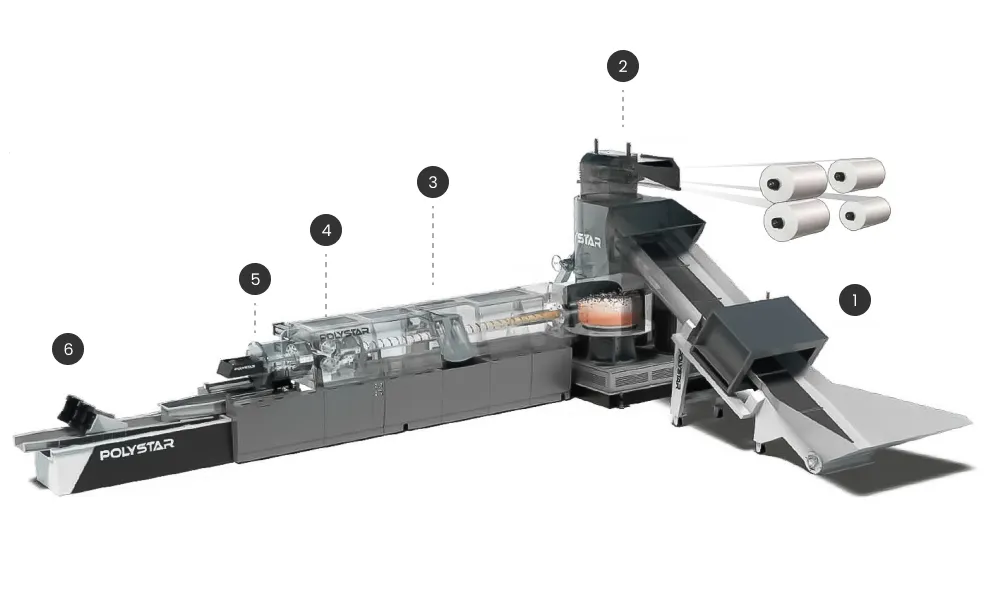
-
1. Feeding System
- With belt conveyor: Feeding of scraps is easy and automatically controlled (the conveyor automatically starts/stops depending on the amount of material input)
- Film-on-rolls: Fed with nip roll feeder at the same time.
-
2. Cutting and Compacting
Cutter compactor with rotary knives & direct feeding to extruder :Cuts, dries and compacts the material which enables a fast and stable feeding from the compactor directly into the extruder. -
3. Degassing
Two-zone degassing (double-vented degasification) : Able to process films with larger printed area and some water content.
-
4. Filtration
Screen change with dual channel system: For non-stop operation and prevents material from leaking. -
5. Pelletization
Hot die face pelletizer: Produces high-quality plastic pellets for reprocessing. -
6. Recycled Pellets
The plastic pellets can be put directly back into the production line such as blown film extrusion and pipe extrusion.
Easy to use, high-performance Plastic Recycling Machine
POLYSTAR's high-efficiency, one-step plastic recycling machine Repro-Flex is designed for the reprocessing of PE polyethylene (HDPE, LDPE, LLDPE) and PP polypropylene flexible packaging material, printed and non-printed. This cutter-integrated pelletizing system eliminates the need for pre-cutting the material and requires less space and energy consumption while producing high-quality plastic pellets at a productive rate.
Re-usable Plastic Pellets
The pellets produced by the recycling machine can be put directly back into the production line, in most cases for blown film or pipe extrusion processes.
1. Pellets from in-house, post-industrial recycling
On average, post-industrial waste makes up 5% or more of the entire production line, making in-house recycling very important nowadays as it can significantly reduce the cost of raw/virgin material purchasing.
The plastic pellets produced from in-house waste are almost like new and can be re-used for producing high-quality plastic products once again.
2. Pellets from post-consumer recycling
The Repro-Flex is also designed to work with washed, post-consumer, and used agricultural film. The cutter compactor, which generates frictional heat during the compacting process, helps to further dry and remove the water moisture from the washed film flakes (processed first by the washing lines). The recycled pellets can be used again in the extrusion process, whether 100% (such as garbage bag, LDPE pipe production and etc) or as part of the mixture to reduce raw material cost. The pellets' quality can also be improved by direct dosing of masterbatch and additives.
The Advantages of Plastic Recycling Machine
One Step, All-in-One direct recycling
The Repro-Flex plastic recycling machine combines cutting, extrusion, and pelletizing into one compact and efficient recycling line. The cutter compactor of the recycling machine prepares (pre-conditions) the material into an ideal condition for the extrusion process and feeds the material directly into the extruder with a centrifugal force. Compared to the conventional recycling machines, this integrated system does not require a separate crusher, and therefore, eliminates the problem of inconsistent feeding (over-feeding or insufficient feeding)
Easy material feeding without the need for pre-cutting
The waste material enters the machine from the belt conveyor (for film scraps and rigid plastic regrind) and the nip roll feeder (for complete film rolls) at the same time. An extra silo tank can also be added to store and feed pre-washed film flakes. The feeding is controlled automatically based on how full the cutter compactor is. The cutter compactor then cuts, dries, and compacts the material into a semi-molten condition (just below the agglomeration point), which is optimal for the extrusion process that follows. The cutter compactor then feeds the material directly and consistently into the extruder screw.
Higher output capacity
The integration of the cutter compactor and extruder ensures extremely fast and stable feeding, the tangentially connected extruder is continuously filled with pre-compacted material. This results in a much higher production output compared to other types of recycling systems on the market.
Higher pellets quality
The stable material feeding together with the hot die face pelletizer produces round-sharped, uniformed-sized plastic pellets that are higher in value and optimal for reproduction (extrusion processes).
Other benefits
- The lower investment cost for a high-quality and durable machine
- Low energy consumption with a high production output
- Fast machine delivery and installation: Polystar produces on an average of 8 sets of Repro-Flex per month and can deliver the machine faster than most manufacturers. The average delivery time of a Polystar recycling machine is 60 days.

Blown film producers

PP woven producers

Recycling Centers

Repro-Flex Catalog
-
PE/PP Film Roll
-
Bags
-
Film Scraps
-
Bubble Film
-
Film Sheet
-
Shrink Film
-
Waste Bags
-
Stretch Film
-
Garbage Bag